Maschinenbau : Engel: Warum nachhaltige Mobilität eine Chance für den Spritzguss ist
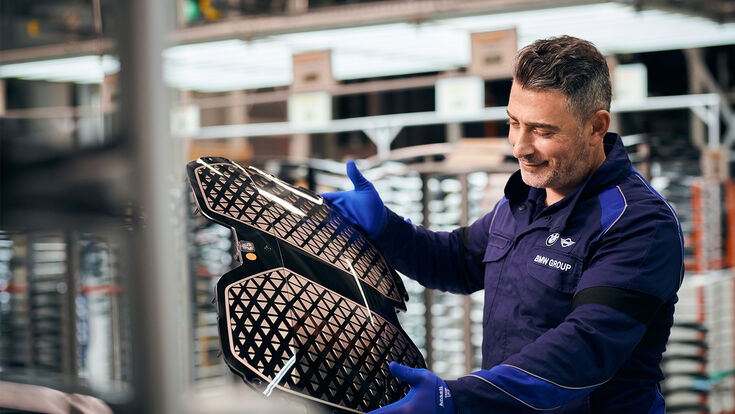
Die Nieren für den neuen BMW iX werden in einer hochintegrierten Reinraumproduktionszelle von Engel produziert.
- © BMW Group"Mobilität völlig neu denken", war das erklärte Ziel von Engel-CEO Stefan Engleder, als er am Mittwoch die Mobility Days 2023 eröffnete. Dementsprechend breit war das Programm der erstmalig abgehaltenen Veranstaltung; die Vorträge reichten von selbstfahrenden Taxis im Silicon Valey über senkrecht-startende Flugzeuge für Megacitys bis hin zu Neuigkeiten in der E-Mobilität und Brennstoffzellen-Technologie. Und für alle Beteiligten schien klar: nachhaltig soll sie werden, die Mobilität von morgen. Dass Kunststoff dabei verstärkt zum Einsatz kommen soll, davon ist etwa Franz Füreder, Leiter der Business Unit Automotive & Mobility von Engel, überzeugt. "Polymere Materialien sind per se Leichtbauwerkstoffe und unterstützen den schonenden Umgang mit Energie und Rohstoffen. Sie lassen sich sehr effizient im Spritzguss verarbeiten, was innovative Technologien für den Massenmarkt zugänglich macht".
Zukunftsthema autonomes Fahren
Beim autonomen Fahren geht es um das Thema Konnektivität, die Kommunikation zwischen den Fahrzeugen untereinander sowie mit weiteren Verkehrsteilnehmern und der Umgebung. Die dafür eingesetzten Sensoren nutzen elektromagnetische und akustische Methoden. Abstandssensoren zum Beispiel arbeiten mit Ultraschall, die adaptive Geschwindigkeitsregelung mit Radar und Nachtsichtassistenten mit Infrarot. Auch hier ist der Einsatz von Polymeren daher unumgänglich, denn wie Michael Fischer, Leiter Business Development Technologie von Engel hervorhebt: „Kunststoffe sind durchlässig für Schallwellen und elektromagnetische Strahlung". Im automobilen Front- und Heckbereich wurden laut Fischer Aluminium und Stahl bereits verdrängt. Er sieht die Weiterentwicklung und Verbreitung des autonomen Fahrens als eine große Chance für den Spritzguss. BMW in Landshut produziert auf Basis der von Engel entwickelten clearmelt Technologie beispielsweise „Nieren“ für den elektrischen BMW iX. Dabei handelt s sich um ein zwei-Komponenten-Verfahren, das In-Mould Decoration mit Polyurethan-Überfluten kombiniert.
>> Immer up to date mit der Branche sein? Hier geht’s zum wöchentlichen Factory-Newsletter!
Eine gesellschaftliche Perspektive auf das Thema selbstfahrende Autos bringt Trendscout Mario Herger aus dem Silicon mit. Auf den Mobility Days schildert er seine Erfahrung mit Robotaxis in San Francisco, die dort bereits komplett fahrerlos im Personentransport eingesetzt werden. "In den ersten Minuten nach dem Wegfahren geht der Puls nach oben, aber dann kann ich mich einfach zurücklehnen und die Fahrt genießen", berichtet er, nicht ohne einen Seitenhieb auf Europa, wo derlei Technologien noch weit vom breiten Einsatz entfernt sind.
Ebenfalls interessant: Batterie-Technologie: Automatisierung, Energiedichte und Recycling als Gamechanger
Thermoplasten und die Recyclingfähigkeit
Engel forscht in seinem eigenen Technologiezentrum in St. Valentin seit mehr als zehn Jahren gemeinsam mit Partnerunternehmen Leichtbau-Composites. Die Entwicklungen zielen besonders auf integrierte und automatisierte Prozesse, um eine kosteneffiziente Großserie zu ermöglichen. Ein Fokus liegt etwa auf dem Einsatz thermoplastischer Faserverbundmaterialien. Denn ein konsequent thermoplastischer Materialansatz ebnet einem späteren Recycling der Bauteile den Weg.
Im organomelt Verfahren von Engel werden in einem einzigen integrierten Prozessschritt thermoplastische Faserverbundhalbzeuge – zum Beispiel Organobleche und UD-Tapes – umgeformt und funktionalisiert. Zum Funktionalisieren werden Versteifungsrippen oder Montageelemente unmittelbar nach dem Umformen im selben Werkzeug mit einem Thermoplast aus der Gruppe des Matrixmaterials des Organoblechs angespritzt. Die erste Großserienanwendung dieser Technologie ging 2018 bei Valeo Front End Modules in Smyrna, Tennessee, an den Start. Engel lieferte hierfür eine duo 1700 Spritzgießmaschine, drei easix Knickarmroboter für die Vorbereitung einer Vielzahl von Metall-Inserts und für das Organoblech-Handling, einen viper 90 Linearroboter und eine IR-Ofen.
Da durch das Automobilrecycling in Zukunft viele glasfaserverstärkte Bauteile aus Polyamid und Polypropylen sortenrein zurück in die Materialkreisläufe kommen, beschäftigt sich Michael Fischer auch mit deren Verarbeitung. "Beim Shreddern der Bauteile werden die Glasfasern gekürzt. Um aus den Rückläufern wieder hochwertige Faserverbundbauteile zu produzieren, muss beim Aufbereiten der Rezyklate neues Fasermaterial zudosiert werden“, erklärt er. Er und sein Team arbeiten an einem zweistufigen Konzept, mit dem das Plastifizieren und Einspritzen in zwei voneinander unabhängige, aufeinander abgestimmte Prozessschritte aufgeteilt wird: Um geshredderte Faserkunststoffverbundbauteile wieder zu mechanisch hochbelastbaren Fahrzeugkomponenten verarbeiten zu können, integriert Engel zusätzlich zum Schmelzefilter eine Glasfaserzuführung ins Anlagenkonzept. Die frischen Langglasfasern werden vor dem Einspritzen der Schmelze zudosiert. „Wir befinden uns hier in der Erprobungsphase“, sagt Fischer
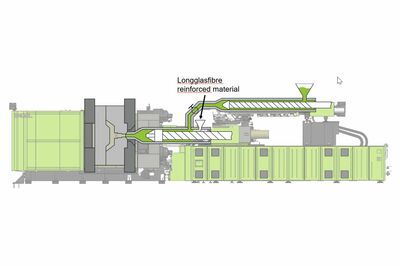
Lesen Sie auch: Welche Antriebsarten werden sich in Zukunft durchsetzen?
Kunststoffe für Brennstoffzellen und Batteriegehäuse
Die alternativen Antriebstechnologien eröffnen ebenfalls neue Potenziale für die Spritzgießindustrie. „Die Wasserstofftechnik wird derzeit in Europa besonders stark vorangetrieben, vor allem im Lkw-Bereich“, berichtet Fischer. „Mit dem Joint-Venture Cellcentric bündeln Daimler Truck und Volvo Group ihre Erfahrung in der Entwicklung und Produktion von Brennstoffzellensystemen". Engel ist einer ihrer Technologielieferanten, wenn es um die Verarbeitung von Elastomeren und insbesondere Flüssigsilikon (LSR) geht. Brennstoffzellen erfordern nämlich viele Dichtungen, die zum Teil direkt auf Metall- oder Kunststoffkomponenten aufgespritzt werden. Hinzu kommen Kabeldurchführungen, die aus LSR produziert werden.
Die Bipolarplatten, von denen pro Brennstoffzelle mehrere hundert Stück benötigt werden, bestehen aus Metall, aber das könnte sich langfristig ändern, ist Fischer überzeugt. „Wir entwickeln bereits Spritzgießlösungen für Bipolarplatten auf Basis von Thermoplasten. Die Herausforderung besteht in der Plattendicke von nur wenigen Zehntelmillimetern, wofür wir Dünnwandtechnologien mit Spritzprägen kombinieren.“
Auch für Batteriegehäuse und -wannen in Elektro-, Hybrid- und Brennstoffzellenfahrzeugen lösen Thermoplaste immer häufiger Stahl- und Aluminiumbleche ab. So entwickelt zum Beispiel Envalior – hervorgegangen aus DSM Engineering Materials und dem Geschäftsbereich High Performance Materials von Lanxess – eine neuartige Batteriewanne aus Polyamid mit einem hohen Glasfaseranteil. Die Wanddicke liegt unter 7 mm bei einem Einzelschussgewicht von 60 kg. „Die Herausforderung besteht darin, die hohen Lasten im Kunststoffdesign stabil aufnehmen zu können“, erklärt Fischer. „Außerdem erfordern das großvolumige Bauteil und das sehr hohe Schussgewicht eine besonders große Spritzgießmaschine. Wir planen mit einer duo Großmaschine mit 8000 Tonnen Schließkraft.“

Neue Megamaschinen für Mobilitäts-Anwendungen
Waren die Engel duo Spritzgießgroßmaschinen lange Zeit mit Schließkräften bis 5500 Tonnen der Standard, hat der Maschinenbauer die Baureihe nach oben erweitert. Neben besonders großflächigen und voluminösen Bauteilen ermöglichen diese neuen Megamaschinen mit ihren extrem großen Werkzeugeinbauräumen eine umfangreichere Prozessintegration – zum Beispiel im Bereich der Verscheibung. "Schließkräfte von mehr als 10.000 Tonnen und Schussgewichte von mehreren hundert Kilogramm sind heute schon technisch möglich“, gibt Stefan Engleder einen Ausblick.