Qualitätssicherung : Innovation in der Qualitätssicherung
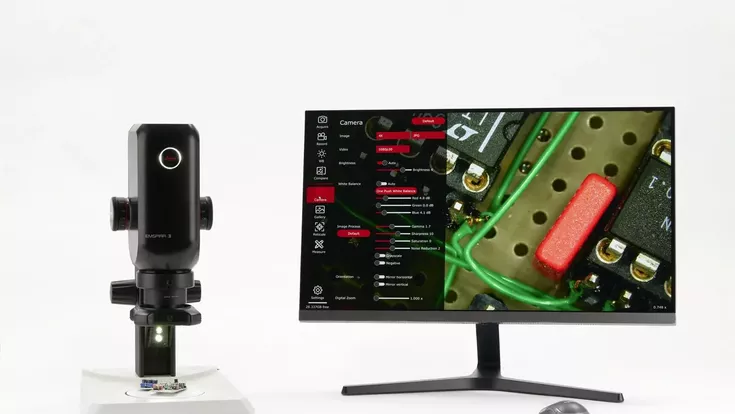
Emspira3, neuestes Produkt in der Digitalmikroskopfamilie von Leica Microsystems
- © Leica MicrosystemMit dem Vormarsch von E-Mobilität und erneuerbaren Energien steigt die Nachfrage nach Batteriezellen und -module. Entlang der gesamten Kette des Produktionsprozesses, von der Elektrodenfertigung über die Zellfertigung bis zur Verpackung mehrerer Zellen in die fertigen Batteriemodule, werden neue Verfahren implementiert.
Prüftechnik – „Made for Automation“
Ein kürzlich realisiertes Prüfsystem des Messsystemherstellers Xarion erlaubt die automatisierte, kontaktfreie Messung der Elektrolytverteilung in einer neu produzierten Batteriezelle. Die gleichmäßige Benetzung der Elektroden und Separatoren mit Elektrolytflüssigkeit ist entscheidend für die Qualität und Lebensdauer der fertigen Batterie. Zur Qualitätsprüfung wird eine Ultraschallwelle mittels eines Laserstrahls im Prüfling erzeugt. Ein optisches Mikrofon detektiert auf der gegenüberliegenden Seite der Batterie, wie gut der Schall von der Batterie geleitet wird. Trockene Bereiche der Batteriezelle reflektieren den Schall, während mit Elektrolytflüssigkeit benetzte Bereiche den Schall leiten. „Wir können hier die deutlich höhere Auflösung und Messgeschwindigkeit unserer Technologie, verglichen mit konventionellen Luftkopplern, ausspielen“, sagt Martin Wallner, Chief Operations Officer bei Xarion.
Früher musste der Wandler genau auf seiner Eigenfrequenz betrieben werden, wenn man Ultraschall für empfindliche Prüfungen verwenden wollte. Für eine gute Signalübertragung war zudem das Angleichen des akustischen Widerstands zwischen dem Piezo-Schwinger und dem Material nötig. Dazu benötigte man entweder direkten Kontakt oder ein Kontaktmittel in Form von Wasser oder Gel. Für das optische Mikrofon fand man bei Xarion einen überraschenden Workaround: Die Innovation ermöglicht es, den Schwinger vollständig wegzulassen. In dem optischen Verfahren verändert der Schall die Wellenlänge eines Laserstrahls, der zwischen zwei kleinen Spiegeln hin und her reflektiert wird. Dadurch ändert sich die Helligkeit des ausgekoppelten Lichtes und es kann über eine mechanische Schwingung gemessen werden. Mit dieser Methode erreicht das Mikrofon ein detektierbares Frequenzintervall, das mindestens zwanzigmal größer ist als das jedes anderen konventionellen Ultraschallsensors.
Einfach auf dem Roboterkopf montiert erreicht man mit der berührungslosen Prüfmethode auch schwer zugängliche Stellen. Der glasfasergekoppelte Sensorkopf des Mikrofons findet Fehler unterhalb der Oberfläche, die für das Auge unsichtbar sind. Mikrorisse, Lufteinschlüsse oder fehlerhafte Verbindungen werden frühzeitig gefunden und verhindern den schlimmsten Fall: das vollständige Versagen eines Bauteils. „Dass die Prüftechnik von Xarion vollkommen berührungsfrei arbeitet, ist ein großer Vorteil in der Automatisierung“, erklärt Balthasar Fischer, Gründer von Xarion, stolz.

All-in-one-Digitalmikroskop
„Unsere Kunden verbringen viel Zeit damit, zwischen den Arbeitsplätzen zu wechseln, um die einzelnen Schritte ihres Inspektionsprozesses sorgfältig durchzuführen“, schildert Markus Lusser, Präsident von Leica Microsystems. Ein System für alles verspricht daher das neue Digitalmikroskop Emspira3 von Leica Microsystems. Damit werden Vergleich, Messung und die Weitergabe der Qualitätssicherungsdokumentation direkt über ein Netzwerk ermöglicht. Bei der visuellen Inspektion kommt man ohne PC-Messung aus, denn das On-Screen-Display lässt sich im Stand-Alone-Modus benutzen.
„Wie können wir komplexe Inspektionsanforderungen vereinfachen?“, war eine Frage, die man sich bei Leica stellte. Den diversen unternehmens- und anwendungsbezogenen Anforderungen versucht das Unternehmen mittels breiten Angebots an Zubehör und Beleuchtungsoptionen entgegenzukommen. Um Variationen in der Tiefe der Anwendung zu ermöglichen, kann die Benutzeroberfläche angepasst werden. Funktionen, die für eine bestimmte Inspektion beispielsweise nicht benötigt werden, sind ausblendbar. Benutzerfreundlichkeit und Zeitersparnis bei Gutteil/Schlechtteil-Entscheidungen schaffte man durch die Ein-Klick Vergleichsmöglichkeit des Live-Bilds mit Referenzbildern oder individuell erstellten Overlays. „Dieses Feature ist besonders hilfreich bei wiederkehrenden Aufgaben, z. B. der Prüfung, ob Teile oder Komponenten innerhalb der spezifizierten Toleranzen liegen“, so Lusser. Gespeichert wird am lokalen Netzwerk. „Unsere Anwender können Emspira 3 entsprechend ihrer Arbeitsweise einrichten, sodass sie ihre Qualitätskontrollziele in kürzerer Zeit durchführen können“, sagt der Leica-Microsystems Präsident.
„Unsere Anwender können Emspira 3 entsprechend ihrer Arbeitsweise einrichten, so dass sie ihre anspruchsvollen Qualitätskontrollziele in kürzerer Zeit durchführen können“Markus Lusser, Präsident Leica Microsystems
Optische 3D-Oberflächenmessung
Geeignete Messsysteme zu finden, ist bei Spezialanforderungen oft gar nicht so einfach. Der Messtechnik-Spezialist Bruker Alicona setzt auf optische Messgeräte. Diese Geräte basieren auf der Technologie der Fokus-Variation. Dies ist ein flächenbasiertes Verfahren zur optischen, hochauflösenden 3D-Oberflächenmessung im Mikro- und Nanobereich. Die Funktionalitäten eines Rauheitsmessgeräts und eines Koordinatenmesssystems werden in den Geräten vereint. Genutzt wird die geringe Tiefenschärfe einer Optik, um die Tiefeninformation einer Probe zu extrahieren. Das Messsystem InfiniteFocusSL erkennt beispielsweise mittels Tiefenmessung und Oberflächenklassifikationssoftware auch kleinste Rauheitsunterschiede der Oberfläche. Eine KI-basierte Automatisierungsoption unterscheidet zwischen i.O. und n.i.O. (in Ordnung/nicht in Ordnung) Oberflächen.
Der Auswertung liegt eine Kombination von 2D Texturdaten und 3D Topografiedaten zugrunde, sie werden während des Prüfprozesses analysiert. Die seriennahe Überwachung und die automatische Erkennung von i.O. und n.i.O.-Druckgussteilen wird durch Machine Learning ermöglicht. So stellt man auch sicher, dass spezifizierte Toleranzen bei Prozessänderungen eingehalten werden. Zeitnahes Reagieren ist daher möglich, indem z. B. Anlagenparameter angepasst werden.
Präzisionsmessung, Robustheit, Messgeschwindigkeit und Wiederholgenauigkeit ermöglichen die Automatisierungstauglichkeit des Messsystems. Den Messablauf haben die Entwickler so gestaltet, dass auch Benutzer ohne spezifische Kenntnisse Messungen durchführen können, sagt man bei Bruker Alicona. Nur so sei ein reibungsloser Ablauf in der automatisierten Produktion möglich.
Geräuschdetektion bei Maschinen
Die Akustik von Maschinen ist oft unberechenbar. Beispielsweise entstehen in Aluminium bearbeitenden Maschinen durch Hohlräume manchmal Schwingungen, die deutlich hörbare Geräusche verursachen. Oft ist deren Ortung schwer möglich. Früher half man sich im Maschinenbau in solchen Fällen mit Schallschutzverkleidungen, die die gesamte Maschine umhüllten. In einem Spezialanwendungsfall des Maschinenbauers Fill war diese Lösung nicht möglich, da ein Fenster in das Innere der Maschine sonst zugedeckt worden wäre. Also versuchte man sich an der nächsten, zeitraubenden Möglichkeit, nämlich am Ausbau der einzelnen Komponenten, in denen man den Geräuscherzeuger vermutet, bis man den Fehler gefunden hatte.

-
„In der Entwicklung unseres Messsystems wurde speziell darauf Wert gelegt, dass man schnell zu Ergebnissen gelangt“
Thomas Rittenschober, CEO Sevenbel
Die Problemlösung und eine immense Zeitersparnis fand man mit dem Einsatz einer akustischen Kamera, des österreichischen Unternehmens Sevenbel. Das Linzer Start-up patentierte eine neuartige Technologie zur Visualisierung von Schall und entwickelte sie zur Serienreife. Die bisherigen Kameras zur Schallvisualisierung in der Anschaffung teuer, begrenzt mobil und verlangten meist Expertenwissen für die Bedienung. Bei der akustischen Kamera von Sevenbel scannt ein Sensor das Schallfeld. Die Schallquellen und akustisch problematische Stellen werden in einer mobilen ähnlich wie bei Wärmebildkameras auf einem Foto oder Video angezeigt. Die akustischen Bilder können direkt am Handy des Anwenders analysiert und sofort in Form von automatisch generierten Berichten geteilt werden. „In der Entwicklung unseres Messsystems wurde speziell darauf Wert gelegt, dass man schnell zu Ergebnissen gelangt“, sagt Sevenbel-CEO Thomas Rittenschober. Inklusive Aufbauzeit für das Messsystem dauert es weniger als fünf Minuten, bis akustische Messergebnisse vorliegen. Weiß man, wo Geräuschquellen liegen, spart man wertvolle Zeit in Entwicklungsprozessen und kann sich direkt der Behebung der Geräuschquelle widmen.
-
"Der Einsatz von KI im Qualitätsmanagement hilft potenzielle Qualitätsprobleme zu erkennen und zu beheben, bevor sie größere Auswirkungen haben“ Patrick Ratheiser, CEO Leftshift One
Patrick Ratheiser, CEO Leftshift One
KI zur Qualitätsvorhersage
Algorithmen, um Qualitäsvorhersagen zu treffen und Verbesserungsempfehlungen zu geben. „Die Produktion ist ein komplexer Vorgang, Abweichungen sind unvermeidbar“, sagt Patrick Ratheiser, CEO von Leftshift One. Der Wettbewerbsvorteil, den er bieten möchte, liegt darin, Abweichungen (Events) adäquat einzuordnen und schnell zu beheben. Die KI-basierte Lösung liefert dem Qualitätsmanagement bereits vorab eine Klassifizierung des Events. Sie stützt sich auf vergangene Ereignisse an den Produktionslinien und textliche Beschreibungen der Mitarbeiter:Innen. Das Clustern unstrukturierter Informationen liefert wertvolle und vergleichbare Datensätze. Der Qualitätsmanager kann anhand dieser Daten fundierte Entscheidungen treffen und frühzeitig Maßnahmen für Valdierungsprozesse veranlassen. „Der Einsatz von KI im Qualitätsmanagement hilft, potenzielle Qualitätsprobleme zu erkennen und zu beheben, bevor sie größere Auswirkungen haben“, sagt Ratheiser. Die rechtzeitige Erkennung und Behebung von Qualitätsproblemen reduziert Ausschuss und Nacharbeit und verbessert die Effizienz in der Produktion. Erkenntnisse, die aus der Datenanalyse gewonnen werden, helfen zudem bei der Produktweiterentwicklung. Anwendungsgebiete sieht man bei Leftshift One etwa in der Automobilindustrie, der Elektronikindustrie und der Lebensmittelindustrie.
Lesen Sie auch: Instandhaltung 4.0: Alles, was Sie darüber wissen sollten