Anwenderbeitrag: Keramikfertigung im Grenzbereich bis 1μ : Kern Micro HD bei Doceram zur Keramikbearbeitung
V.l.n.r.: Kern-Vertriebsingenieur Michael Bette, Doceram-Betriebsleiterin Vanessa Förster, Kern-Vertriebsleiterin Verena Lindner und Stefan Veltum, technischer Leiter von Doceram
- © Kern Microtechnik GmbHBereits im Jahr 1995 hat sich die Moeschter Group als Spezialist für Hochleistungswerkstoffe zusätzliches Keramik-Know-how ins Haus geholt und daraus die Geschäftseinheit Doceram gebildet. Der Bereich ist heute auf allen Kontinenten und in zahlreichen Branchen in der Bearbeitung von Hochleistungskeramiken tätig. Dazu zählen neben der Automobilindustrie auch der Maschinen- und Anlagenbau sowie die Medizintechnik, der Vorrichtungsbau, die Luftfahrt, Uhren/Schmuck und rund 20 weitere.
Vorteile der Werkstoffgattung Keramik gibt es viele. Denn Bauteile aus diesem Material sind extrem hart, steif und verschleißarm, elektrisch sowie thermisch isolierend und chemisch resistent. Eigenschaften, ohne die so manche Hightech-Produkte und deren zuverlässiger Einsatz gar nicht möglich wären. Doch letztlich gibt es selten Vorteile ohne Nachteile: Keramik ist teuer, und die Bearbeitung gilt als extrem anspruchsvoll.
Lesetipp: G520F von Grob kommt bei Druckguss Westfalen zum Einsatz
Beiden Argumenten pflichtet auch Stefan Veltum, technischer Leiter der Moeschter Group/Doceram, bei: „Es stimmt schon, dass der Materialpreis von Keramik deutlich höher ist als der von Metall. Allein die höhere Standzeit relativiert jedoch bereits die anfänglichen Mehrkosten. Noch wichtiger ist, dass so manche Anlagen oder Maschinen dank der verwendeten Keramikbauteile länger ohne Unterbrechung laufen können. Speziell in solchen Fällen rechnet sich der höhere Materialpreis ganz schnell. Letztlich fangen wir da an, Ja zu sagen, wo andere anfangen Nein zu sagen. Unsere Anwendungsfelder und die Probleme der Kunden, welche wir tagtäglich lösen müssen, sind sehr anspruchsvoll. Daher müssen zum einen unsere Materialien höchsten Anforderungen genügen, und zum anderen deren Verarbeitung auf Formel-1 Niveau sein.“
No-Go: Risse oder Abplatzer am Produkt
Bleibt noch die Herausforderung der Bearbeitung des spröden Werkstoffs. Risse oder Abplatzer sind ein absolutes „No-Go“. Solche oder ähnliche Beschädigungen würden bei keramischen Produkten zum Bauteilversagen führen, da hierdurch eine Rissausbreitung initiiert ist. Zudem müssen die Teile mit höchster Präzision gefertigt werden.
Eine Herausforderung, der sich nicht viele Unternehmen stellen, wie Stefan Veltum weiß: „Für die Bearbeitung von Keramik braucht man viel Know-how. Wir haben unsere Expertise über eine Zeit von fast 30 Jahren aufgebaut und daher die Fertigungsprozesse zuverlässig im Griff. Dank unserer jüngsten Investition in die Kern Micro HD noch besser als je zuvor.“
Bis Anfang 2023 setzte Doceram primär auf den traditionellen Herstellungsprozess. Dieser sieht nach dem Fräsen und Sintern noch Schleifen, Läppen oder Honen vor, um die notwendige Genauigkeit und Oberflächengüte zu erreichen.
Damit verbunden war eine gewisse Einschränkung in der wählbaren Form der Bauteile, und trotz aller Expertise war die Ausschussrate bei der Hartbearbeitung höher als heute. Zudem lief der Fertigungsprozess meist über mehr als einen Tag, da die Bauteile teils zwei bis dreimal auf verschiedene Maschinen umgespannt werden mussten.
Keramik-Bauteile in einer Aufspannung herstellen
Den Wunsch, Keramik-Bauteile in einer Aufspannung herzustellen, hatten die Mitarbeiter von Doceram schon lange. Einzig, ihnen fehlte die geeignete Technologie. Als Mitte des Jahres 2022 wachstumsbedingt weitere Investitionen anstanden, machte sich Veltum gemeinsam mit Vanessa Förster, Bereichsleitung Operations, auf die Suche nach einem neuen Bearbeitungszentrum. „Wir wussten, dass die Fünfachsfräsmaschinen der Kern Microtechnik GmbH im Höchstpräzisionsbereich einen sehr guten Ruf genießen,“ berichtet Vanessa Förster und ergänzt: „Dementsprechend nahmen wir mit Michael Bette, dem für uns zuständigen Kern-Vertriebsingenieur, Kontakt auf.“
Kurze Zeit später präsentierte Bette gemeinsam mit Kern-Technologieleiter Marvin Gröb in Dortmund, wie Hartkeramikbearbeitung mit dem Präzisions-Fünfachszentrum Kern Micro HD und dem patentierten Schnittmodus funktionieren kann. Michael Bette erinnert sich: „Am Ende des Vortrags meines Kollegen war es für einige Sekunden absolut still im Raum. Dann sagte Stefan Veltum: ‚Wenn nur die Hälfte von dem zutrifft, was Sie hier vorstellen, haben Sie eben eine Maschine verkauft.‘ Was soll ich sagen, es trifft alles zu, und wir haben eine Maschine verkauft.“
Kern Micro HD mit duktilem Schnitt
Bevor es soweit war, führten die verantwortlichen Mitarbeiter von Doceram und Kern weitere Gespräche und fertigten gemeinsam einige Probe-Bauteile auf der Kern Micro HD. „Alles hat so funktioniert, wie wir uns das gewünscht hatten“, bekräftigt Veltum, „und tatsächlich hatte kein anderer Hersteller ein vergleichbares Gesamtpaket zu bieten.“
Das von Technikchef Veltum erwähnte Gesamtpaket von Kern Microtechnik beinhaltet neben dem Top-Bearbeitungszentrum eine Vollautomatisierung mit dem Erowa Robot Compact 80, eine Comat-Filteranlage zur zuverlässigen Entfernung der Keramikschlämme, die In-Prozess-Messung mit einem BLUM TC52 LF Messtaster und vieles mehr.
Lesetipp: China setzt auf Roboter als Wachstumsstrategie
Darüber hinaus schätzen Stefan Veltum und Vanessa Förster gleichermaßen die umfangreiche Applikationsberatung. Und sie heben in besonderem Maße den von Kern-Ingenieuren entwickelten duktilen Schnitt hervor: „Diese Erfindung bildet die Grundlage dafür, dass spezielle Fräswerkzeuge mit geometrisch bestimmter Schneide in der Lage sind, spröde Keramik mit fließendem Span abzutragen“, erläutern die beiden Führungskräfte.
Auch Siliziumnitrit wird prozesssicher zerspant
Seit Ende des ersten Quartals 2023 ist die Kern Micro HD bei Doceram in Betrieb und wird von den Mitarbeitern gerne als „Königin“ bezeichnet. Sie ist zentral in der Fertigung platziert und begeistert die Belegschaft auch noch nach mehr als einem Jahr Einsatz. Entscheidend dafür ist unter anderem, dass sich tatsächlich alle Keramikwerkstoffe in einer Aufspannung bearbeiten lassen. Sämtliche Silikat- und Oxid-Keramiken ebenso wie die von Doceram eigenentwickelten Materialien Cerazur und EvoCera. Bei EvoCera handelt es sich um eine duktile Keramik, deren maximale Belastung bis zum Bruch sich mittels FEM exakt berechnen lässt. Laut Veltum ist dies mit keiner anderen Keramik möglich.
Und auch die zuverlässige Bearbeitung der Nicht-Oxid-Keramikgruppe, zu denen beispielsweise Siliziumnitrit gehört, stellt für die Dortmunder Keramikprofis kein Problem mehr dar. „Dieses Material ist extrem hart, einzigartig leicht, temperaturwechselbeständig und antihaftend“, erläutert Stefan Veltum. „Leider ist es aufgrund seiner herausragenden Eigenschaften sehr teuer und zudem besonders schwierig zu bearbeiten. Dank der Kern Micro HD zerspanen wir dieses Material jetzt absolut prozesssicher.“
Dabei funktioniert der Serienanlauf mit viel weniger Einstellteilen, als das früher möglich war. Denn die von Kunden geforderten Ergebnisse in puncto Präzision und Oberflächengüte werden schnell erreicht. Selbst bei größeren Serien im hohen vierstelligen Bereich bleibt die Prozesssicherheit durchgängig erhalten. Nach Zahlen zur produzierten Qualität gefragt, erklärt Vanessa Förster, dass die Genauigkeitswerte in ihrem Marktsegment nur selten unter einem hundertstel Millimeter liegen müssen. „Da haben wir mit dieser Maschine einen großzügigen Puffer“, freut sie sich.
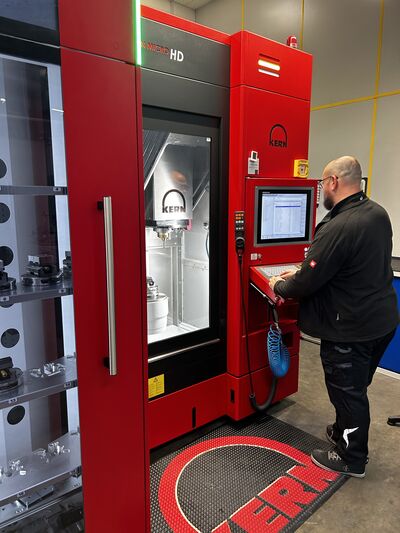
Bei der Oberflächengüte sieht das anders aus. „Um optimales Gleitverhalten oder Dichtheit zu gewährleisten, können die Oberflächen fast nicht glatt genug sein“, sagt die Operations-Bereichsleiterin: „Mit der Kern Micro HD und dem duktilen Schnitt erreichen wir beim Fräsen prozesssicher einen Ra von 0,05 µm. Das haben wir bisher nur durch zusätzliches Gleitschleifen, Läppen oder Honen geschafft.“
Keramikbauteile amortisieren sich oft schnell
Keramikprodukte, die Doceram produziert und die in der Praxis zum Einsatz kommen, gibt es viele. Um nur ein paar wenige zu nennen: Zentrierstifte, Positionierstifte und andere hochgenaue Betriebsmittel für die Automobilindustrie. Zeigen darf Doceram diese nicht, denn sie unterliegen – wie die meisten Bauteile – Geheimhaltungsvereinbarungen.
Eine MIG/MAG-Schweißdüse aus Siliziumnitrit ist da eher die Ausnahme. Gegenüber ihrer Alternative aus preiswerterem Kupfer weist die Keramikdüse eine deutlich längere Standzeit auf und muss viel seltener ausgetauscht werden. Da sie primär in großen, automatisierten Schweißanlagen zum Einsatz kommt, amortisiert sich die Keramikvariante in kürzester Zeit.
Die Herstellung dieser Schweißdüse klappt mit der Kern Micro HD ebenso problemlos wie die Produktion eines Testbauteils mit 48 M4-Gewindebohrungen. Interessantes Detail: Es gab bei dieser Bearbeitung nur sehr wenig Werkzeugverschleiß. „Selbst nach der Bearbeitung von zwei Testblöcken waren die Werkzeuge noch scharf“, stellt Veltum fest.
Dabei freut sich der technische Leiter nicht nur über die gleichbleibend hohe Prozessqualität der Königin. Sie scheint auch gegen abrasiven Keramikschlamm extrem gut geschützt zu sein. Von Langzeiterfahrung will er dabei nach einem Jahr Einsatzzeit natürlich nicht reden, aber die Erläuterungen von Kern sind für ihn überzeugend.
Bald zwei Königinnen im Unternehmen?
Kern-Vertriebsleiterin Verena Lindner dazu: „Generell sind unsere Führungen dank der einzigartigen Mikrospalt-Hydrostatik kaum anfällig für Verunreinigungen. Zudem haben wir Abdeckungen eingebaut, die jegliches Verschmutzen verhindern.“ Zur Beweisführung hat Kern bei einer Testmaschine nach einer knapp zweijährigen Keramik-Bearbeitungsphase das Hydrauliköl der Führungen untersucht. Das Ergebnis: Null Kontamination.
Ähnlich positiv sieht das Fazit von Stefan Veltum und Vanessa Förster aus, wenn man sie fragt, wie zufrieden sie mit der Entscheidung sind, in die Kern Micro HD investiert zu haben. Unisono sagen sie: „Wir sind mehr als zufrieden.“ Und in die Zukunft gedacht, zeigen sie sich nicht abgeneigt, in ein zweites Präzisionsfünfachszentrum dieser Marke zu investieren: „Dann haben wir halt zwei Königinnen in unserem Unternehmen.“