Energiesparen : Niob und Co.: Wie ein Algorithmus die Produktion von Hochleistungswerkstoffen optimiert
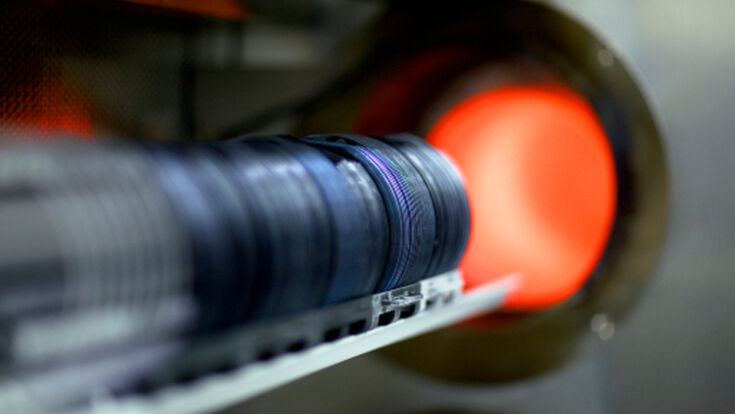
Sie stecken in Computertomografen, in Smartphones oder Photovoltaikanlagen: die hochschmelzenden Metalle Molybdän, Wolfram, Tantal und Niob. Das Tiroler Unternehmen Plansee Hochleistungswerkstoffe (HLW) hat sich vor rund 100 Jahren auf diese Werkstoffe spezialisiert. Ihr Vorteil ist: Sie sind sehr widerstandsfähig und haben einen hohen Schmelzpunkt. Aber es gibt auch einen Haken: sie sind in der Herstellung sehr energieintensiv.
Um ihre volle Leistungsfähigkeit zu erreichen, müssen diese Materialien einer energie- und zeitintensiven Wärmebehandlung unterzogen werden. In vielen Fällen machen Komponenten einen Glühprozess durch. Das geschieht unter anderem in elektrisch beheizten Hochtemperaturöfen, in welche die Produkte eingeschichtet werden und die mit einer Zonentemperaturregelung ausgerüstet sind. Für jede Heizzone gibt es eine Vorgabe, welche Temperatur erreicht werden muss. „Da der Glühprozess einen vergleichsweise hohen Energieeinsatz erfordert, muss dieser Prozess im Sinne der Ressourcenschonung und der Einsparung teurer Energie optimiert werden“, erläutert Gerfried Weiss, Produktionsleiter bei Plansee. Dazu wurde gemeinsam mit dem AIT Austrian Institute of Technology ein Forschungsprojekt aufgesetzt.
Dieses Video könnte Sie auch interessieren: Energiespar-Tipp von Oliver Prang
Glühprozess: Dauer ist entscheidend
Bei einem Glühprozess wird der Ofeninnenraum so lange erhitzt, bis die vorgegebene Zonentemperatur erreicht ist. Danach wird diese Temperatur für eine gewisse Haltezeit auf diesem Niveau gehalten – dies soll garantieren, dass die Produkte auf die vorgegebene Temperatur erwärmt und eine bestimmte Mindest-Glühzeit bei dieser Temperatur geglüht werden. Anschließend werden die Produkte wieder abgekühlt.
In der Praxis ist die exakte Einhaltung dieser Mindest-Glühzeit nicht trivial, da der Temperaturverlauf der Produkte sehr stark von der Beladung des Ofens abhängt und der Temperaturverlauf aufgrund der thermischen Trägheit der Materialien nicht genau der Zonentemperatur folgt. Überdies kann die Temperatur (bis zu 1.800 Grad Celsius) der wärmebehandelten Gegenstände kaum direkt gemessen werden – zum einen sind entsprechende Lastthermoelemente teuer, sensibel und schwierig zu installieren, zum anderen sind Softwaremodelle zur Temperaturschätzung sehr aufwendig. Daher geht man in der Praxis eher auf Nummer sicher und wählt eine längere Dauer für den Glühprozess. Ist diese zu kurz, wird das Glühgut nicht lang genug homogen geglüht, was sich negativ auf die Materialeigenschaften auswirkt. Ist sie aber zu lange, wird Zeit und Energie verschwendet.
Um den Glühprozess zu optimieren, hat Plansee gemeinsam mit Forscher:innen des AIT Austrian Institute of Technology das Projekt ThermoTec gestartet. „In diesem Projekt haben wir das Know-how von Plansee zu Materialien und Prozessen mit unserem Wissen über die Regelung schwieriger und komplexer Prozesse kombiniert“, erläutert AIT-Projektleiter Martin Niederer. Er und seine Kolleg:innen arbeiten am AIT Center for Vision, Automation & Control in der Forschungsgruppe Complex Dynamical Systems an der Optimierung und Automatisierung von Produktionsprozessen.
Energie- und Zeiteinsparung bei gleichbleibender Qualität
Durch aufwendige Messungen, Analysen und Modellierungen konnte nun ein Algorithmus entwickelt werden, mit dessen Hilfe die gewünschte Mindest-Glühzeit für jede beliebige Beladung zuverlässig eingestellt werden kann. Bei der experimentellen Validierung des Algorithmus in mehr als 230 Glühfahrten an einem Ofen über ein Jahr verteilt zeigte sich, dass die Haltezeit des Prozesses im Durchschnitt um 20 Prozent gesenkt werden konnte. Die Reduktion des Energiebedarfs und der CO2-Emissionen entsprechen dem Verbrauch von 15 Einfamilienhaushalten.
In begleitenden Werkstoffprüfungen wurde gezeigt, dass die Produktqualität unverändert hoch blieb. Durch die Optimierung sank überdies die Gesamtdauer des Prozesses um knapp 12 Prozent, was eine bessere Auslastung des Ofens ermöglicht. „Das Verfahren sorgt für eine exakte Einhaltung der Mindest-Glühzeit, woraus sich eine Einsparung von Energie und damit Heizkosten sowie ein verbesserter Durchsatz bei gleichbleibend hoher Qualität ergibt“, fasst Tobias Glück, Leiter der Competence Unit Complex Dynamical Systems zusammen.
Einsatz des neuen Verfahrens in der Praxis
Das Verfahren wird mittlerweile bei Plansee im Produktivbetrieb eingesetzt und trägt damit zur Senkung des Energiebedarfs in der Produktion bei. „Der neue Algorithmus ist in die vorhandene Ofensteuerung integrierbar und kann somit problemlos auf andere Öfen übertragen werden. Dies werden wir in den kommenden Monaten weiter umsetzen“, berichtet Bernhard Mayr-Schmölzer, Entwicklungsingenieur bei Plansee.
(Ebenfalls interessant: Smart Factories: Die Zukunft der Produktion ist intelligent, vernetzt und anfällig)