4D Concepts-CEO über 3D-Druck : "Wir reiten nicht auf ein oder zwei 3D-Printing-Verfahren herum"
Welche Merkmale prägen derzeit den Markt des 3D-Printing und der additiven Formgebung?
Di Maglie: Bei den Maschinen gab es schon länger keine großen Innovationssprünge mehr. Bei den Werkstoffen bestimmen derzeit weniger die Neuheiten als vielmehr die hohen Rohstoffpreise das Geschehen, und bei den Verfahren hat sich inzwischen das Lasersintern an die Spitze gesetzt – insbesondere, wenn es um die Herstellung funktioneller, seriennaher und kleiner Kunststoffteile für non-visible-Applikationen geht, also etwa Klemmelemente für Motorräume oder Schaltschränke.
Wo positioniert sich hier 4D Concepts mit seinen Modellen und Entwicklungen?
Di Maglie: Im Unterschied zu vielen anderen Dienstleistern der Branche haben wir uns als interdisziplinäre Technologie-Werkstatt mit einem Fullservice-Angebot aus Ingenieurs-Knowhow, handwerklichen Kompetenzen, zahlreichen verschiedenen Formgebungsverfahren und einer großen Werkstoffauswahl aufgestellt. Damit sind wir in der Lage, die komplette Prozesskette von der ersten Produktidee bis zur Serienreife abzudecken. Innerhalb dieses Rahmens haben wir uns zudem auf die Realisierung sehr großer Modelle und sehr kleiner Serienteile spezialisiert.
Wie setzen Sie diese extreme Polarisierung in der Praxis um?
Di Maglie: Indem wir nicht schmalspurig auf ein oder zwei 3D-Printing-Verfahren herumreiten, sondern eine große Bandbreite an additiven und traditionellen Fertigungstechniken einsetzen. Dabei rufen wir das Potenzial der verschiedenen Verfahren, Methoden und Werkstoffe auch treffsicher ab.
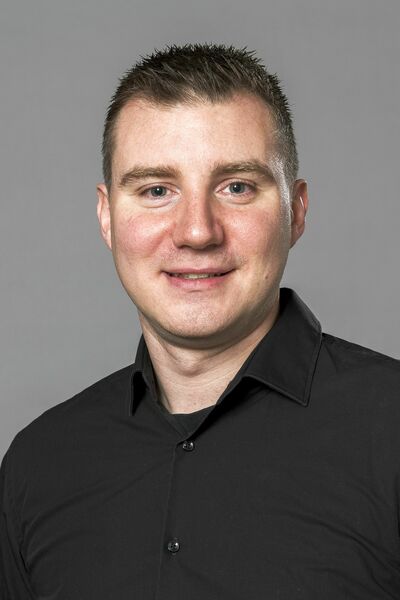
Welche Verfahren setzen Sie denn primär ein?
Di Maglie: Das richtet sich nach dem Projekt. Für Großmodelle – hier sprechen wir über Unikate mit bisweilen mehr als drei Metern Höhe – bearbeiten wir technische Kunststoffe und PU-Schäume vorrangig im CNC-Fräsen, während einzelne geometrisch komplexe Kunststoffteile meist additiv entstehen und Flächenelemente beispielsweise aus Plattenmaterial hergestellt werden. Großmodelle sind oft Baugruppen mit einem bunten Material- und Oberflächenmix, bei dem neben Konstruktions-Knowhow auch viel handwerkliches Geschick gefragt ist. Kleine und mittelgroße Serienteile bis Losgröße 1.000 – etwa Sitzschalen oder Clips aus Polyurethan – realisieren wir primär via Vakuumguss oder Reaction-Injection-Moulding (RIM). Für Kunden, die wärmestabile Prototypen oder Ersatzteile aus PEEK oder ULTEM brauchen, nutzen wir die Fused-Filament-Fabrication Technologie (FFF). Für mechanisch belastbare Prototypen und Kleinserien bis etwa 200 Stück setzen wir das Selektive Lasersintern (SLS) oder die Multi Jet Fusion (MJF) ein. Für Design- und Konzeptmodelle verwenden wir je nach Qualitätsmaßstab die Stereolithographie (SLA), den MultiJet- (MJP), den PolyJet- (PJP) oder den ColorJet-3D-Druck (CJP). Für viele Kunden übernehmen wir zudem die gesamten Vorfeld-Arbeiten.
Was meinen Sie mit „Vorfeld-Arbeiten“?
Di Maglie: Viele Großmodell-Kunden, Designer, Produktentwickler oder auch Werbeagenturen können uns gar keine oder nur unvollständige Konstruktionsdaten liefern. Ausgehend von Fotos oder Handskizzen erstellen wir dann in SolidWorks die CAD-Files und anschließend – je nach Prozess – in Magics die fehlerfreien STL-Datensätze für den 3D-Druck oder in Mastercam die CAM-Daten fürs CNC-Fräsen. Wir können über die digitale Freihand-Modellierung in FreeformPlus sogar „aus dem Nichts“ Objekte schaffen und dafür die 3D-Druckdaten generieren.
(Lesen Sie auch: Reverse Engineering: Wie die Voestalpine mit Nachkonstruktion Prozesse optimiert)
Und wie finden Sie einen Point of Departure, wenn es dann in die konkrete Realisierung des Modells geht?
Di Maglie: Sobald wir mit dem Kunden ins Gespräch kommen, entsteht in unseren Köpfen ein Bild von der Konstruktion, der Werkstoffauswahl und dem optimalen Umsetzungsprozess. Das geht sehr schnell. Wir haben inzwischen fast 30 Jahre Modellbau-Erfahrung und kennen die Möglichkeiten und Grenzen der verschiedenen 3D-Druckverfahren sehr genau – etwa hinsichtlich der erzielbaren Festigkeiten, Oberflächenqualitäten oder chemisch-physikalischen Resistenzen. Wir wissen daher auch, welche Produkte, welche Prototypen und welche Großmodell-Komponenten sich besser konventionell fertigen lassen.
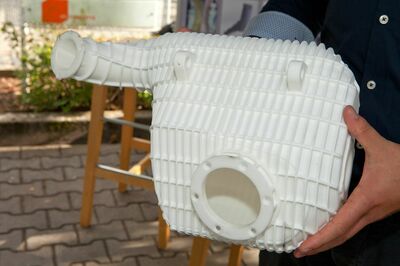
An welchen Großmodell-Aufträgen arbeiten Sie beispielsweise?
Di Maglie: Zuletzt haben wir ein überdimensionales Fahrradkettenritzel, einen übergroßen Photovoltaik-Stecker sowie mehrere Karosserie-Musterteile für einen namhaften Autolack-Hersteller realisiert.
Und welche Serien- oder Kleinserien entstehen derzeit in Ihren Hallen?
Di Maglie: Hier reicht die aktuelle Palette von massiven Dämpfungselementen aus Polyurethan über transluzente und elastische Rahmen für Abfüllanlagen bis hin zu temperaturbeständigen Riemenscheiben aus carbonverstärktem PEEK und on-demand-Ersatzteilen für elektrotechnische Baugruppen – um nur einige Beispiele zu nennen.
Was kann man in den kommenden Monaten von 4D Concepts erwarten?
Di Maglie: Derzeit testen wir ein neues Stereolithographie-Material zur Herstellung transparenter Bauteile – beispielsweise für Befüllsimulationen – und arbeiten an der weiteren Digitalisierung der Lasersinter-Prozesse. Interessante Impulse erwarten wir zudem aus verschiedenen Forschungsprojekten, an denen wir beteiligt sind. Dabei geht es etwa um die additive Fertigung von Leiterplatten mit der bei uns praktizierten Fused-Filament-Fabrication Technik (FFF) sowie um den Einsatz von reaktiviertem Sinterpulver zur nachhaltigen Herstellung antibakterieller Bauteile für die Medizintechnik. Eventuell fließen erste Ergebnisse daraus im kommenden Jahr in unser Portfolio ein.
(Ebenfalls interessant: Additive vs. substitutive Fertigung)