Batterien : Wie AVL List den CO₂-Fußabdruck in der Batterieproduktion optimiert
Verbesserung des CO₂-Fußabdrucks durch Just in Time Messung
AVL List baut in dessen Battery Innovation Center in Graz Prototypenbatterien in größeren Stückzahlen - bis zu über 100 je Prototypen-Baustufe. Dort werden Kernprozesse wie das Stapeln der Batterien zum Modul, das Laserschweißen der Zellverbindungen und die Klebeprozesse voll automatisiert durchgeführt. So kann man bereits in der Prototypenphase robuste Produktionsprozesse und hohe Qualität erzielen. Mittels eingebauten Messgeräten wird die dafür aufgewendete Energie, respektive das CO₂, das beim Schweißen unter Schutzgas entsteht, identifiziert, dem Produkt zugewiesen und in einem Batteriepass dokumentiert. Der CO₂-Fußabdruck des Produktes wird dadurch bereits in einer sehr frühen Phase bestimmt und kann im Produktentwicklungsprozess für das Serienprodukt weiter optimiert werden, erklärt Gerhard Meister, Vice President Electrification, AVL List.
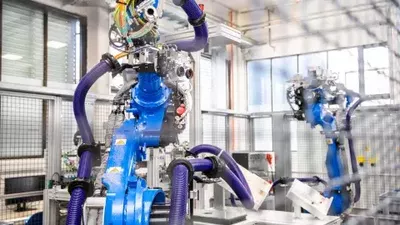
Vorbereitung auf die Anforderungen des EU – Batterie Passes
Die Vorbereitungen zur Einführung des digitalen Batteriepasses sind in vollem Gange. Dazu werden als erster Schritt Daten gesammelt, die entlang der Wertschöpfungskette für verschiedene Beteiligte wertvoll sein könnten. Diese werden im AVL Battery Innovation Center entsprechend gespeichert. Ihre Verarbeitung hilft, um ein Produkt wie die Autobatterie nach ihrem Einsatz im Fahrzeug möglichst sinnvoll und effizient auch für 2nd Life und Recycling nutzbar machen zu können.
Ebenfalls interessant: Wie Bosch Rexroth das Recycling von Batterien effizient machen will
Trends in der Batterieproduktion
Aktuell gehe der Trend in Richtung Lithium-Eisen-Phosphat Zellen, sagt Meister, weil sie wesentlich günstiger als die bekannten NMC (Nickel, Mangan, Kobalt) Li-Ionen Zellen seien. Gleichzeitig kommen vermehrt Natrium-Ionen-Zellen in großen Mengen auf den Markt. Die geringere Energiedichte als die der Li-Ionen Zellen, macht die einfachere Rohstoffverfügbarkeit wett. Zusätzlich nähert man sich dem Start der Serienproduktion von Feststoffbatterien, deren Vorteile eine hohe Energiedichte und ausgezeichnete Schnelladefähigkeit sind. Durch die hohen Produktionskosten werden diese allerdings derzeit nur in Premiumfahrzeugen eingesetzt. „Es wird auch künftig unterschiedliche Batteriebauformen und chemische Zusammensetzungen am Markt geben, für die es unterschiedliche Anforderungen an Zerlegbarkeit und Wiederverwendbarkeit gibt“, sagt Meister. Diese Informationen können End-of-Life-Stakeholdern via digitalem Batteriepass zugänglich gemacht werden.
(Ebenfalls interessant: Bernhard Geringer: „Ich will das Elektroauto nicht schlecht reden“)
-
„Es wird auch künftig unterschiedliche Batteriebauformen und chemische Zusammensetzungen am Markt geben, für die es wiederum unterschiedliche Anforderungen an Zerlegbarkeit und Wiederverwendbarkeit gibt“
Gerhard Meister