Maschinenbau : Fill-Produktionsleiter: "Ein Roboter baut bei uns im Werk keine Maschinen zusammen“
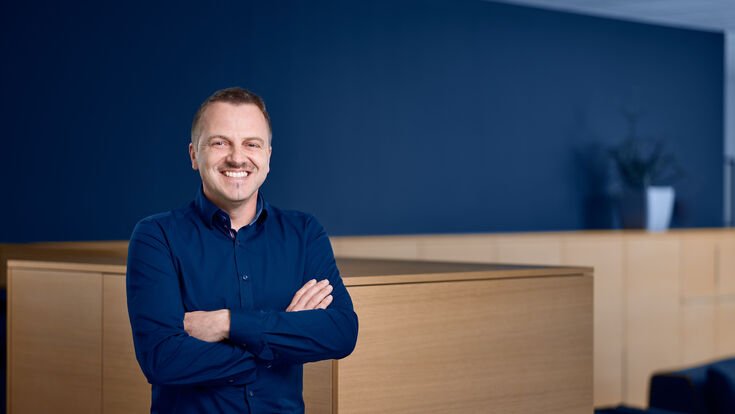
Aktive Mitgliedschaft erforderlich
Das WEKA PRIME Digital-Jahresabo gewährt Ihnen exklusive Vorteile. Jetzt WEKA PRIME Mitglied werden!
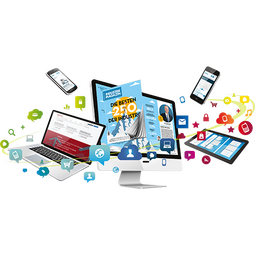
Sie haben bereits eine PRIME Mitgliedschaft?
Bitte melden Sie sich hier an.
Herr Prentner, Sie sind seit kurzem Produktionsleiter bei Fill. Wie war die erste Zeit in Ihrer neuen Position?
Der erste Monat ist natürlich sehr spannend, weil ich damit einen für mich neuen Aufgabenbereich übernommen habe. Ich kenne die Firma und die Mitarbeiter:innen zwar seit knapp 34 Jahren. Aber ich muss mich natürlich erst in alle Prozesse reinarbeiten und reindenken.
Was war damals der Grund, warum Sie zu Fill gegangen sind?
Für mich war klar, dass ich etwas Technisches machen möchte. Ich bin in der Landwirtschaft aufgewachsen und wollte vor allem nicht mehr in die Schule gehen, sondern mich praktisch betätigen. Ich hatte drei Möglichkeiten: Landmaschinenmechaniker, Automechaniker oder eben eine Lehrstelle im Sondermaschinenbau. Fill war mit seinen automatisierten Anlagen aus meiner Sicht immer ein zukunftsweisendes Unternehmen. Das hat auf mich schlussendlich den meisten Reiz ausgeübt.
Was war für Sie die größte Veränderung während der gesamten Zeit im Unternehmen?
Im Jahr 2000 waren wir bei Fill 200 Mitarbeiter, heute sind wir 1000. Das heißt, die Gesamtorganisation hat sich enorm verändert. Wir sind von einem mittelständischen Betrieb zu einem Industriebetrieb herangewachsen. Früher hat es für die gesamte Produktion zwei Meister gegeben, die sich um alles gekümmert haben. Heute wird die Produktion in die verschiedensten fachlichen Abteilungen untergliedert, dazu gibt es je nach Personalanzahl einen oder mehrerer Teamleiter.
Ebenfalls interessant: Das sind Österreichs 50 größte Maschinenbauer
Entdecken Sie jetzt
- Lesen
- Videos
-
Podcasts
- Staubmanagement in der Produktion 16.10.2023
- Automatisierung in der Messtechnik 11.09.2023
- 3D-Druck: Neuigkeiten und Trends 17.01.2023
Unser Maschinenpark hat sich also völlig verändert.
Ist der Maschinenpark von damals noch wiederzuerkennen?
Von den Teilefertigungsmaschinen gibt es heute gar keine mehr, die damals gelaufen ist. Da ist kontinuierlich investiert worden, damit wir am Ball bleiben. Der Maschinenpark hat sich also völlig verändert.
Sie haben ja die Produktionsleitung von Engelbert Gurtner übernommen, der damals Ihr Lehrlingsausbilder war. Was war denn da das zentrale Learning, das Sie von Herrn Gurtner mitgenommen haben?
Engelbert Gurtner selbst hat mir das Fräsen in der Fertigung gezeigt. Als mein Meister hat er meine Ausbildung stark geprägt. Er ist in der Produktion seit 50 Jahren in der Firma tätig, zu 100% Praktiker mit einem gewaltigen Erfahrungsschatz, der von der klassischen Teilefertigung bis hin zur Anlagenmontage reicht - einfach alles, was man in einem breiten Maschinenbau benötigt.
Sie hatten zu Beginn Ihrer Laufbahn viele Montage-Einsätze im In- und Ausland. Gibt es ein Highlight aus dieser Zeit?
In jungen Jahren war ich vor allem in Österreich und Deutschland unterwegs, und zwar bei allen bekannten Automobilherstellern. Der am weitesten entfernte Einsatz war in Brasilien, wo ich fünf Monate lang gearbeitet habe. Am kniffligsten war sicherlich ein Auftrag für einen Automobilhersteller, wo wir eine überaus umfangreiche Transferanlage für die Herstellung von Motorkomponenten installiert haben.
Sie sind dann 2000 nach der Meisterprüfung in die Konstruktion gewechselt. Wie war diese Umstellung für Sie?
Ich habe die gewerbliche Meisterprüfung mit der Unternehmerprüfung gemacht und anschließend im Unternehmen die Chance ergriffen, mich weiterzuentwickeln. Das Montagefahren hat mir Spaß gemacht, aber es verträgt sich schlecht mit dem Familienleben. Vorher war die praktische Tätigkeit klar überwiegend, nach dem Wechsel in die Konstruktion war die geistige Arbeit am CAD-Arbeitsplatz klar bestimmend, was schon eine große Umstellung für mich war. Ich musste mich daran gewöhnen, jeden Tag am selben Ort im Büro zu sein, im Gegensatz zu den Montagen bei unseren Kunden in unterschiedlichen Ländern.
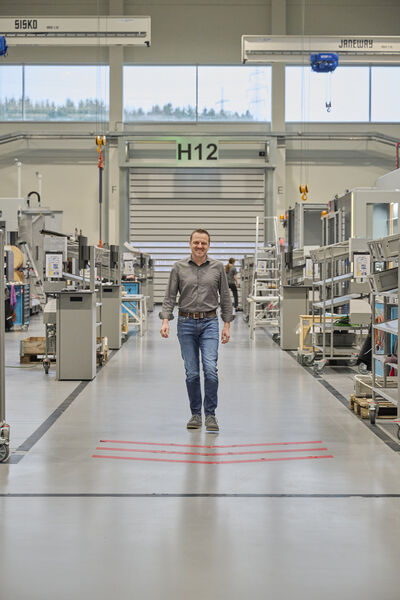
Ein Roboter baut bei uns im Werk keine Maschinen zusammen.
Als Sie Anfang April als Produktionsleiter angefangen haben, haben Sie gesagt, Sie wollen die Produktionsabläufe weiterentwickeln. Wo sind da die größten Hebel?
Weil wir Sondermaschinenbauer sind, haben wir eine hohe Einzelteilfertigungstiefe im Haus. Aufgrund unserer Firmengröße und der entstandenen Produktpalette, die wir herstellen, kommen wir aber auch immer mehr in die Stückzahlfertigung, wo wir uns in Richtung Automatisierung entwickeln werden. In der Teilefertigung wird es Bearbeitungsmaschinen geben, die mannlos über Nacht fertigen. Dazu investieren wir in Schweißroboter und entwickeln uns schrittweise zur papierlosen Fertigung. Über Lean optimieren wir unsere Prozesse mit dem Ziel, die Effizienz zu steigern und Durchlaufzeiten zu reduzieren.
Hat sich durch das Wachstum der Firma auch die Logistik verändert?
Auf jeden Fall. Früher hatten wir 2 Produktionshallen, hier hat die Teilelogistik intuitiv – sozusagen überschaubar auf Zuruf – funktioniert, mittlerweile gibt es bis zu 14 Hallen, die individuell nach Projekten bestückt werden müssen. Aufgrund dieser neuen Dimensionen braucht es Prozesse über die ganze Organisation hinweg, die wir immer weiterentwickeln und entsprechend den neuen Anforderungen anpassen.
Fill-CTO Alois Wiesinger hat angekündigt, dass etwa auch autonom fahrende Fahrzeuge Anwendung finden sollen. Was ist da schon umgesetzt?
Das erste autonome Fahrzeug ist in einem Teilbereich der Montage schon im Einsatz, aktuell im Testlauf. Je nachdem, welche Erfahrungen wir damit machen, werden derartige Transportsysteme schrittweise ausgerollt. Zudem schwebt uns vor, eine automatische Materialbestückung in der produktionsfreien Zeit zu realisieren. Auch neue Software-Tools in der Fertigungssteuerung sind in der Anschaffung, sodass wir einen noch besseren Überblick bekommen und Abläufe aktiv steuern können.
Haben Sie konkrete Beispiele, wo digitale Assistenzsysteme Ihren Mitarbeiter:innen die Arbeit erleichtern?
Es gibt kaum noch 2D-Zeichnungen in Papierform, die meisten Zeichnungen werden digital am Arbeitsplatz zur Verfügung gestellt, somit sind diese auch immer aktuell. Die Anlagenmontage erfolgt nahezu ausschließlich nach 3D CAD-System. In der Montage stehen Laptops bzw. PCs zur Verfügung, von denen aus die Maschine dreidimensional ersichtlich ist. Somit kann sie von allen gewünschten Richtungen aus betrachtet und Schnittebenen können beliebig erstellt werden. Über Barcodescanner können Bauteile identifiziert und zugeordnet werden. So kommt man Stück für Stück weg von den klassischen Zeichnungen in Papierform, die man vor wenigen Jahren noch zu hundert Prozent in der Werkstatt gesehen hat.
Ein weiteres Beispiel: die E-Installation erfolgt nicht mehr klassisch nach Schaltplan in Papierform. Dies wird aktuell über E-Plan Software mittels Tablet erledigt. Hier wird Schritt für Schritt vorgezeigt, wo welches Kabel anzuschließen ist, Änderungen können direkt über Redlining dokumentiert werden.
Wie weit kann in der Montage die Automatisierung noch weiter ausgebaut werden?
Es ist und bleibt viel Handarbeit. Wir haben natürlich Hilfsmittel wie Kräne, aber die gibt es schon seit Ewigkeiten. Hilfsmittel wie Montagetische, die drehbar und höheneinstellbar sind, sodass ein sauberes und schnelles Arbeiten ermöglicht wird, werden produktspezifisch eingeführt. Elektronische Tools sowie Mess- und Prüfvorrichtungen erleichtern den Arbeitsalltag und sichern die Qualität. Solche kommen mehr und mehr zum Einsatz. Ansonsten sind wir als Sondermaschinenbauer klassischerweise noch auf Manpower angewiesen, vor allem auf ausgebildete Fachkräfte. Ein Roboter baut bei uns im Werk keine Maschinen zusammen. Bei den Anlagen, die Fill produziert, ist das anders. Hier kommen viele Roboter zum Einsatz, da ist alles voll automatisiert. Wir verbauen pro Jahr ca. 200 Roboter.
Zu meiner Zeit mussten wir uns viel mehr selbst erarbeiten, heute wird Vieles vorgegeben. Ob das immer so gut ist? Das ist eine andere Frage.
Der Trend geht zu immer mehr Kommunikation zwischen den Maschinen. Wo sind Sie da kundenseitig gerade dran?
Fertigungsmaschinen wie Fräs-, Schweiß- und Schneidmaschinen in der Produktion sind vernetzt. Es wird extern, also offline, programmiert, die Programme werden zur Maschine gespielt und der Fertigungsprozess kann erfolgen. Wenn jemand etwas ändert, wird das geänderte Programm wieder über das Netzwerk zurückgespielt und gesichert. Wenn zukünftig das gleiche Bauteil wieder gefertigt wird, kommt der gespeicherte Programmstand zum Einsatz. Die Vernetzung von Fill Anlagen beim Kunden erfolgt in Abstimmung mit dem Kunden und ist sehr individuell. Von der Erfassung der Produktionsdaten, der digitalen Bauteilverfolgung, der Übertragung und Sicherung von Fertigungsprogrammen, der Sicherung von Prozessinformationen bis hin zur Anbindung für den Servicebereich gibt es viele Möglichkeiten.
Sie haben als Lehrling angefangen. Wie hat sich dieser Lehrberuf in dieser Zeit verändert?
Früher hatte man eine kurze Basis-Ausbildung direkt in der Werkstätte, anschließend wurde man dem Fertigungspersonal abwechselnd zugeordnet und hat mitgearbeitet. Heute gibt es eigene Lehrwerkstätten mit eigenem Ausbildungspersonal und organisiert für jedes Lehrjahr einen eigenen Ausbildungsplan. Die Lehrlinge sind rund 1/3 der Ausbildungszeit in der Lehrwerkstätte, ca. 1/3 der Zeit in der Produktion, abwechselnd in allen Bereichen, und rund 1/3 der Zeit in der Berufsschule. Heute werden neben dem fachlichen Schwerpunkt auch viele weitere Themen wie Arbeitssicherheit, soziale Kompetenz, Suchtprävention oder der sorgfältige Umgang mit Geld vermittelt. Zu meiner Zeit mussten wir uns viel mehr selbst erarbeiten, heute wird Vieles vorgegeben. Ob das immer so gut ist? Das ist eine andere Frage.
Was würden Sie dem heutigen Lehrling sagen, der es einmal wie Sie zum Produktionsleiter bringen will?
Jeder hat die Chance, etwas zu erreichen. Du musst es wollen und du musst etwas dafür tun. Du musst motiviert und wissbegierig sein und vor allem muss es dir Spaß machen, mit Leuten zusammen zu arbeiten und etwas zu bewirken. Egal wie unterschiedlich wir sind, müssen wir einen gemeinsamen Nenner finden, um erfolgreich zu sein. Am Ende des Tages ist es das beste Gefühl, wenn man etwas Besonderes geschafft hat.
(Ebenfalls interessant: Wie Roboter zum Umbruch in der Produktion führen