Batterietechnologie : B&R: Strategien für die Batterieproduktion
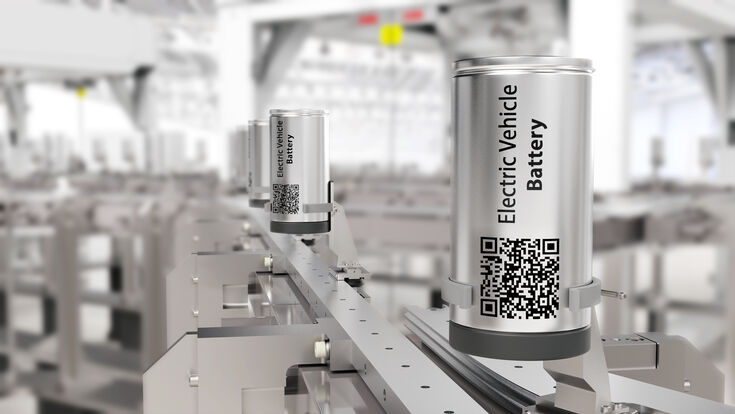
Die Batterieproduktion bei B&R.
- © B&R-AutomationAb 2035 sollen nur noch emissionsfreie Neuwagen in der EU zugelassen werden. Die Nachfrage in der Batterieherstellung ist durch die fortschreitende E-Mobilität exorbitant gestiegen. Die Elektrifizierung birgt Wertschöpfungs- und Beschäftigungspotenziale für den Standort Österreich, sagt eine Studie zur Transformation der österreichischen Fahrzeugindustrie, die das Fraunhofer-Institut durchführte.
Effizientes Nachfragemanagement
„Es ist nicht wirtschaftlich, immer mehr Batteriefabriken zu bauen, um die steigende Nachfrage zu befriedigen“ – sagt Ronny Guber, der 2022 zum Branchenexperte für Elektromobilität bei B&R ernannt wurde. Stattdessen müsse die Fertigung insgesamt effizienter und nachhaltiger werden. Die Automatisierung sei eine Schraube, an der man bei B&R dreht. Zur Durchsatzsteigerung sollen daher Fertigungsprozesse, wie das Markieren oder Schweißen von Batteriestacks, in der Bewegung automatisiert werden. Denn selbst bei langsamer Geschwindigkeiten ist der Produktivitätsgewinn im Vergleich zum getakteten Betrieb hoch.
Dreiklang von Fertigungskapazität, Preisdruck und Produktqualität
Als größte Herausforderung für die Produktion sieht man bei B&R die Fertigungskapazität, den Preisdruck und Produktqualität. Mit einem durchdachten Automatisierungskonzept soll die nötige Balance geschafft werden, um alle drei Anforderungen zu befriedigen.
"Gerade bei kleinen Zellformaten führen die hohen Anforderungen der Fertigungskapazität zu sehr kurzen Zykluszeiten", erklärt Guber. So sei man zum Beispiel bei zylindrischen Batteriezellen je nach Größe mit einem Volumen von 300 bis 1.000 Teilen pro Minute konfrontiert. Trotz Optimierung jedes einzelnen Prozesses ist es notwendig, verschiedene Prozessstationen mehrfach auszuführen. Dieser Herausforderung kommen die B&R-Spezialisten mit modernen Transportsystemen und der damit verbundenen Topologiefreiheit bei. Durch die Reduktion von teuren Rein- und Trockenraumflächen schafft man eine höhere Produktivität pro Fläche und kann dadurch die Kosten senken.
Um den hohen Qualitäts- und Sicherheitsvorstellungen der Automobilindustrie gerecht zu werden, wird Qualitätskontrolle großgeschrieben. Die meisten Prüfungen lassen sich zu 100 % inline durchführen. Als defekt erkannte Zwischenprodukte werden zu einem möglichst frühen Zeitpunkt aussortiert. Dies verhindert unnötigen Ressourceneinsatz und vereinfacht das Recycling. Künstliche Intelligenz wertet die riesigen Datenmengen aus, die dabei anfallen, optimiert und verhindert Ausschuss.
Lesen Sie auch: Welche Antriebsarten werden sich in Zukunft durchsetzen?
Recycling
„Es muss das übergeordnete Ziel sein, die wertvollen Bestandteile der Batterien in einem geschlossenen Kreislauf zu halten“, sagt Guber. Besonders herausfordernd für deren Recycling ist laut dem B&R-Manager die Extraktion einzelner Zellen, da die Zellen in den Modulen oft verklebt werden. Dies erschwere die automatisierte Demontage, die notwendig wird, sobald die Anzahl der zu recycelnden Systeme größer wird. "Effektives und weitgehend automatisiertes Recycling kann nur gelingen, indem man es bereits in der Designphase mit berücksichtigt", betont Guber. Unter dieser Voraussetzung könne man durch den Einsatz von Robotern Kosten sparen und Sicherheitsrisiken reduzieren. Bis Batterien aus dem Einsatz im Fahrzeug in großen Stückzahlen zurückkommen, wird es laut Gubers Einschätzung noch etwas dauern.
-
„Es ist nicht wirtschaftlich, immer mehr Batteriefabriken zu bauen, um die steigende Nachfrage zu befriedigen“
Ronny Guber