Material : Leidenschaft für Draht
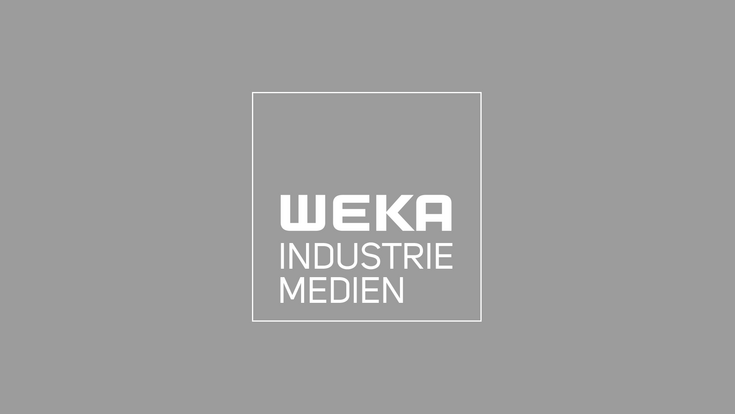
In einer unscheinbaren Seitengasse im fünften Bezirk in Wien produziert man seit 1919 Musiksaiten. Diese umwickelten Stahl- und Kunststoffdrähte haben in der Musikwelt den Ruf, zu den klangfarbenreichsten Musiksaiten der Welt zu gehören. Ca. 200 Mitarbeiterinnen und Mitarbeiter arbeiten in der Wiener Manufaktur. Haupterzeugnisse sind Streichersaiten für Geige, Viola, Cello und Kontrabass. Im Katalog finden sich über 350 Saitensets und mehrere tausend Sondersaiten. Die Herstellung erfordert ungemeines Werkstoff Know-How und hochpräzise Maschinen, die es am Maschinenmarkt so nicht zu kaufen gibt.
Mensch, Werkstoff und Maschine
Damit aus einem einfachen Runddraht ein Produkt für Spitzenklasse-Musiker wird, braucht es Technologie und Menschen mit Fingerspitzengefühl. Um einer Musiksaite gewisse Eigenschaften geben zu können, braucht es auch unterschiedliche Werkstoffe. Damit lassen sich unter anderem Klang (Farben, Bogengeräusch etc.) und Handling (Ansprache, Bogengefühl, Linke-Hand-Gefühl) formen. Das Wissen über das Material brachte dem Saitenhersteller einen Vorteil am Markt. Franz Klanner, technischer Leiter bei Thomastik-Infeld, erzählt: „Grundsätzlich setzen wir alle Materialen ein, die man als Draht herstellen kann. Im Kunststoffbereich eignen sich beispielsweise alle hochfesten Kunststoffe.“ Der Kern aus Stahl oder Kunststoff wird mit mehreren Lagen Runddraht und/oder Flachdraht umwickelt.
In manchen Fällen müssen die Drähte zusätzlich beschichtet werden, unter anderem, da es mit fertigem Produkt intensiven Hautkontakt gibt und keine Allergien ausgelöst werden sollen. „Wir sind der einzige Saitenhersteller, der mit Platin und Titan beschichtet. Demnächst kommt auch ein Produkt mit einer Silberbeschichtung auf den Markt“, verrät Klanner und erzählt weiter: „Für die Drahtbeschichtung setzt man auf einen deutschen Partner mit einem kombinierten PCD/CVD-Verfahren, wie man es aus der Werkzeugindustrie kennt.“ Übliche Elektrolyse-Verfahren eigenen sich nicht, die Säure greift den Draht an und lässt ihn zu schnell reißen. Titan und Platin kann man zudem in der Elektrolyse nicht beschichten.
Von der Manufaktur zur industriellen Fertigung
Werkstoffseitig arbeitet man bei Thomastik-Infeld auf hohem Niveau. In den kommenden Jahren stellt sich der Saitenhersteller der nächsten Etappe der wettbewerbsfähigen Produktion. In den kommenden sieben bis zehn Jahren soll die Hälfte der Produktion vollautomatisiert sein, die andere Hälft bleibt Handarbeit. In vier Gründerzeithäusern sind derzeit die Produktion und die Büros des Saitenherstellers untergebracht. Der Produktionsstandort ist mit dem Erfolg des Unternehmens gewachsen und so finden sich, verteilt über die Häuser und Stockwerke, die Fertigungsbereiche. Für den geplanten Entwicklungsschritt, die Vollautomatisierung mit Roboterzellen ist kein Platz mehr. Daher wird kommendes Jahr ein zusätzlicher Produktionsstandort im Süden von Wien aufgebaut. Die erste vollautomatische Maschine wird nächstes Jahr fertig und etwa 20 Prozent der Produktionsleistung der Manufaktur übernehmen. „Unsere Mitarbeiterinnen und Mitarbeiter können wir erfreulicherweise auf anderen Positionen einsetzen“, sagt Klanner.
Erklärtes Ziel: Null Ausfallzeiten
Die Vollautomatisierung wird bei Thomastik-Infeld bis ins Detail geplant: Die Prozesse für die Saitenherstellung werden komplett in Einzelschritte zerlegt. Jeder Einzelschritt wird später in einer eigenen Automatisierungsstation abgebildet. „Wir decken nicht alle Arbeitsschritte mit einer Station ab, sondern teilen die Stationen sehr genau auf, um im Falle eines Ausfalls die Stillstandzeiten möglichst gering zu halten“, verrät Klanner. Die Logistikanlage ist das Herzstück der künftigen Produktion, sie versorgt die Stationen mit den Teilen. Fällt eine Station aus, wird umgehend die Parallelstation angefahren. Klanner verfolgt mit seinem Team einen ambitionierten Plan: „Ziel ist Null Ausfall bei 24/7 Produktion.“
Bei der Entwicklung des Prozesses haben Klanner und sein Team daher die unterschiedlichen Zeiten der Prozessschritte beschäftigt wie er erzählt: „Bei einem händischen Ablauf ist der längste Prozess eben der längste Prozess. In den automatisierten Linien halten solche Prozessschritte aber extrem auf.“ Darum wurden die Parallelprozesse gründlich geplant, um die Taktzeiten zu erhöhen. In die Planung waren auch die Saitentechniker des Hauses eingebunden. Sie konstruieren die Saiten und arbeiten an neuen Produkten und Verbesserungen. „Die Saitentechniker müssen verstehen, was an der Maschine passiert und welchen Einfluss der Werkstoff, die Maschine und die Person hat. Nur so lässt sich die Handarbeit auf den Automaten übertragen“, sagt Klanner.
Keine Maschinen von der Stange
Für den zusätzlichen Produktionsstandort übernehmen die Wiener die Maschinen vorprogrammiert von Partnern und programmieren sie im Haus fertig. Eher untypisch für das Unternehmen, denn in den vergangenen Jahren war das Unternehmen beim Maschinenbau sehr auf sich gestellt. Kein Hersteller konnte Maschinen liefen, die den Ansprüchen an die hohe Präzision genügten. Vermutlich hätte man bei Thomastik-Infeld die Roboterzellen selbst hergestellt, wenn nicht der Platz für den Maschinenpark fehlen würde. Denn auch der überwiegende Großteil der Halbautomaten, die derzeit im Einsatz sind, wurden im Haus konstruiert und gebaut.
Perfekt abgestimmte Maschinen
Durch die selbst hergestellten Maschinen konnte die Technologie laufend verbessert werden. „Als man 1969 begann, unsere beliebtestes Produkt, die Dominant Saite, mit Kunststoffkern zu entwickeln, gab es Ausschussraten von 95 Prozent“, erzählt Klanner und sagt weiter: „Im Vergleich dazu sprechen wir heute von Ausschussraten von maximal 1 Prozent. Und wir prüfen 100 Prozent der Saiten.“
Auch an anderer Stelle setzte man bei der manuellen Herstellung auf laufende Verbesserung. In der Produktion, mit 90 Prozent Frauen wurden durch ergonomische Verbesserungen die Bedingungen und damit die Produktivität sukzessive erhöht. Der Punkt, an dem die Aufwandsgrenze erreicht ist und mit Verbesserungen keine merkliche Veränderung erzielt wird, ist erreicht. Klanner sagt: „Wir wollen unsere Leute nicht ausbeuten und pressen, sondern es muss lebbar sein. Wir lassen diejenigen Prozesse beim Menschen, die der Mensch besser kann. Es gibt Manufakturen, die immer mehr Druck auf das Personal ausüben. Doch irgendwann lassen sich die Stückzahlen nicht mehr linear erhöhen, sondern nur mit sehr großem Druck im kleinen Prozentbereich. Das ist nicht unser Weg, deshalb gehen wir dort, wo es Sinn macht, in die Vollautomatisierung.“