3D Druck : Leicht gemacht: Leichtmetallbauteile aus dem 3D Drucker
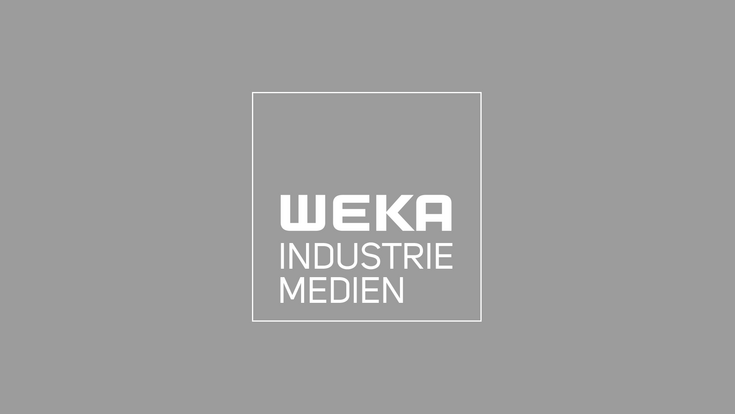
Die 3D Druckindustrie wächst in den letzten zehn Jahren stetig an. Obwohl der 3D Druck immer noch weniger als ein Prozent des globalen Fertigungsmarktes ausmacht, wird die Technologie immer wichtiger. Im Jahr 2019 wuchs der weltweite Markt für additive Fertigung auf über 10,4 Milliarden US-Dollar an und überschritt damit zum ersten Mal in seiner fast 40-jährigen Geschichte die zweistellige Grenze.
Analysten rechnen zudem mit einem jährlichen Wachstum zwischen 18,2 und 27,2 Prozent und damit, dass sich der Markt für den 3D Druck alle drei Jahre verdoppeln wird. Wo 3D Drucken die höchste Akzeptanz und die höchsten Investitionsquoten findet, ist in den USA, Großbritannien, Deutschland, Frankreich und China.
Die Zahlen versprechen einen Boom, doch diesem verleiht Franz Haas, Institutsvorstand der Fertigungstechnik an der TU Graz, einen kleinen Dämpfer: „Nach einer Phase des Hypes hat sich die Meinung durchgesetzt, dass 3D Druck sehr wichtig ist, aber nicht um jeden Preis, nicht für alle Bauteile und nicht für alle Anwendungen.“ In der Industrie wird 3D Druck nicht eingesetzt ohne ausreichend wirkungsvoll zu sein. „Gerade im Leichtbau wird die Methode des Additiven Fertigens eine stark steigende Bedeutung haben. Wenn das Additive Thinking gelebt und der richtige Werkstoff verwendet wird, dann sind 3D-Drucker in der Industrie effizient“, so Haas.
3D Druck: Was man braucht
Apropos richtiger Werkstoff. Ein besonders nützlicher Werkstoff ist Aluminium, 3D Druck eignet sich aber auch ideal für den Einsatz von Titan und Magnesium. Alle drei Elemente zählen zu den Leichtmetallen. „Titan hat eine Dichte von 4,5 g/cm³. Dann folgt Aluminium mit 2,7 g/cm³und Magnesium mit 1,7 g/ cm³“, erklärt Stephan Ucsnik. Er ist Senior Research Engineer beim AIT und thematischer Koordinator für das Themenfeld WAM (wire-based additive manufacturing) beim Leichtmetallkompetenzzentrum Ranshofen (LKR). Je nachdem welche Anforderungen man an das Bauteil hat, setzt man eines dieser Strukturmetalle ein. Das Gewicht des Bauteils ist in der Folge abhängig vom gewählten Werkstoff.
Wie leicht können Leichtmetallbauteile werden?
„Es wäre schön, durch die Anwendungen durchaus auf zwei Drittel der ursprünglichen Masse verzichten zu können. Und das bei gleichen Festigkeitseigenschaften. Könnte man 60 bis 70 Prozent einsparen, bedeutet das auch für den Green Deal enorme Einsparungen an Energie, Treibstoffen und CO2“, erläutert Haas. „Wenn man Schaumstrukturen zulässt, kann man ein Bauteil theoretisch auch so leicht werden lassen, dass es auf Wasser schwimmt. Das macht aber in den seltensten Fällen einen Sinn, da mechanische Eigenschaften, Dichtigkeit und Robustheit stark beeinträchtigt werden“, fügt Ucsnik hinzu. Neben der Leichtigkeit spielen heute auch die Themen Energieeffizienz und Rezyklierbarkeit eine wichtige Rolle.
Vorteile 3D Druck
Leichtmetallbauteile aus dem 3D Drucker heizen durch ihre Effizienz, Materialfreundlichkeit und Kostenschonung den Wettbewerb an. Sie stehen dabei in Konkurrenz zu klassischen zerspanenden und umformtechnischen Technologien wie Fräsen, Drehen, Tiefziehen oder Schmieden. Bei zerspanenden Prozessen wird für gewöhnlich das Vollmaterial bearbeitet. Bei der Fertigung des Bauteils entsteht viel Abfall, der wieder recycliert werden muss und mit einem Wertverlust einhergeht. Hier soll die drahtbasierte additive Fertigung eine neue Möglichkeit bieten zukünftig Material dort aufzubauen, wo es notwendig ist und nicht den überwiegenden Anteil an Material abzutragen, wie es in der Frästechnologie typisch ist“, meint Ucsnik.
Durch die drahtbasierte additive Fertigung (im Englischen wire-based additive manufacturing, kurz WAM) erreicht man laut Ucsnik in mehreren Punkten einen Benefit: „Durch WAM kommt weniger Material zum Einsatz, wir produzieren weniger Abfall und profitieren von schnelleren Fertigungszeiten sowie einer verbesserten Rezyklierbarkeit.“
Zudem führt er aus, dass man am LKR an aktuell noch nicht zertifizierten, aber prozess-spezifisch adaptierten Legierungen arbeitet, die zukünftig höhere Performance zeigen werden, die Herstellungsprozesse besser und schneller machen und das gleiche Bauteil somit bei höherer Leistung geringere Produktionskosten aufweisen wird. Weiters kann man automatisiert arbeiten wodurch zukünftig weniger Personal benötigt wird.
Warum 3D Druck nicht ohne Schutzgase auskommt
„Ohne Schutzgas geht’s nicht“, stellt Haas klar. Ohne Schweißgase würde es sofort zur Oxidation des Metallpulvers kommen. Aber auch bei drahtbasierten Verfahren ist Schutzgas erforderlich. Die Kosten des Schutzgases und der Aufwand, der in der Maschine rund um das Schutzgas betrieben werden muss, sind laut Haas nicht zu unterschätzen.
Die Lage ist also nicht unbedingt ideal, weshalb in diesem Bereich auch intensiv geforscht wird. Haas hält es außerdem für durchaus überlegenswert, auf das Fluten der gesamten Kammer mit Schutzgas zu verzichten: „Wenn man den Raum, für den Schutzgas verwendet wird, minimiert und nur auf die Schmelzzone konzentriert, kann man einiges an Gas und technischem Aufwand reduzieren“, sagt er.
Der 3D Druck heute
Derzeit steht der 3D Druck bei Pulvertechnologien bereits im Bereich von kleinen und mittleren Serien von bis zu 30.000 Stück. Im Fachgebiet der drahtbasierten additiven Fertigung befindet man sich noch beim Prototypenbau und Kleinstserien bis maximal 100 Stück. Hier bedarf es noch einiger Schritte in Bezug auf Qualifizierung, Standardisierung, Reproduzierbarkeit und Skalierbarkeit.
3D Druck: die Chancen von morgen
„3D Druck von jeglichen Werkstoffen ist bereits heute in jedem Lebensbereich denkbar und wird über kurz oder lang überall Einzug halten. Für WAM sehe ich für die nächsten drei bis fünf Jahre die Anwendungsgebiete in Branchen wie der Luftfahrt, Oil & Gas, Energietechnik und weiterführend auch der Automobiltechnik“, blickt Ucsnik in die Zukunft des 3D Drucks. Auch Haas geht von einem verstärkten Einsatz der 3D Drucktechnik aus: „Ich sehe die Zukunft in der Produktion, nicht nur im Prototyping, und hier vor allem in den Zukunftstechnologien, den neuen Mobilitätsformen und der Medizintechnik.“