Kolumne von Sebastian Schlund : Schiri, wir wissen, wo dein Behälter steht!
Dass damit jede Menge komplexer Informationsprozesse einhergehen, versteht sich heutzutage von selbst. Damit das auch bei immer kleineren Losgrößen, zunehmender Produktdiversifikation und anspruchsvollen Lieferzeitanforderungen funktioniert, steigen die Anforderungen an die Beherrschung der damit einhergehenden Komplexität des innerbetrieblichen Materialflusses von produzierenden Unternehmen und deren Wertschöpfungsnetzwerken.
Lange galt menschliche Arbeit als einzige Möglichkeit, mit dieser Komplexität umzugehen, bringt sie doch die notwendige Flexibilität mit. Gerade im Handling- und Kommissionierbereich fristeten Automatisierungslösungen ein Nischendasein; auch weil die Intralogistik Arbeits- und Aufstiegschancen für viele An- und Ungelernte bot. Die demographische Entwicklung, durch die sich aller Voraussicht nach der aktuelle Arbeitskräftemangel noch verschärfen wird, verändert aktuell fundamental die Situation. Produzierende Unternehmen werden zunehmend zur Automatisierung des Materialflusses gezwungen. Fahrerlose Transportsysteme (FTS) bzw. Autonomous Mobile Robots (AMR) werden nicht mehr technologisch in die Logistikbereiche gedrückt, sondern durch fehlende Mitarbeiterverfügbarkeit zunehmend gezogen.
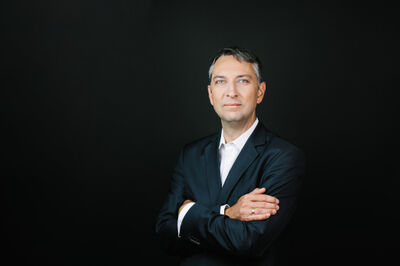
Duck Box: Freischwimmer im Data Lake
Bei der Planung und Implementierung dieser Automatisierungslösungen ist eine strukturierte Vorgehensweise unumgänglich. Die initiale Konzeptplanung befasst sich zunächst mit der Schaffung einer aussagekräftigen und transparenten Datengrundlage. Sehr oft liegen allerdings nur qualitativ unzureichende Daten für quantitative Materialfluss-Berechnungen vor. Als Resultat sind hohe Aufwände zur nachträglichen Datenerfassung erforderlich. Eine Lösung zur Minimierung dieser Aufwände stellt der Einsatz von sensorgestützten, ortungsbasierten Technologielösungen wie beispielsweise der Fraunhofer Austria Duck Box dar. Die Sensorik der Box zeichnet Bewegungsdaten, Handling-Aufwände und Auslastungsgrade der aktuellen Flurförderzeug-Flotte auf und schafft dadurch die Grundlage für datenbasierte Materialfluss-, Layout- und Prozessanalysen.
Die Ergebnisse dieser Analysen zeigen die Schwachstellen und Aufwandstreiber im innerbetrieblichen Materialfluss auf. Zur Optimierung dieser Herausforderungen werden im nächsten Planungsschritt ganzheitliche Grobkonzeptvarianten mit optimal geeigneten Automatisierungslösungen gebildet. Durch eine Kosten-Nutzen-Bewertung kann zum Abschluss der Konzeptplanung das optimale Automatisierungskonzept ausgewählt werden. Danach sollte ein besonderer Fokus auf die detaillierte Ausgestaltung von physischen Prozessen und IT-Schnittstellen gelegt werden, damit Lagerung und Warenfluss auf einer stabilen Datengrundlage automatisiert und hoffentlich genauso unauffällig funktionieren wie ein guter Schiedsrichter.