Presshärtender Stahl : voestalpine-Forscher: Mit Stahl-Fertigungsverfahren Chance auf europäische Auszeichnung
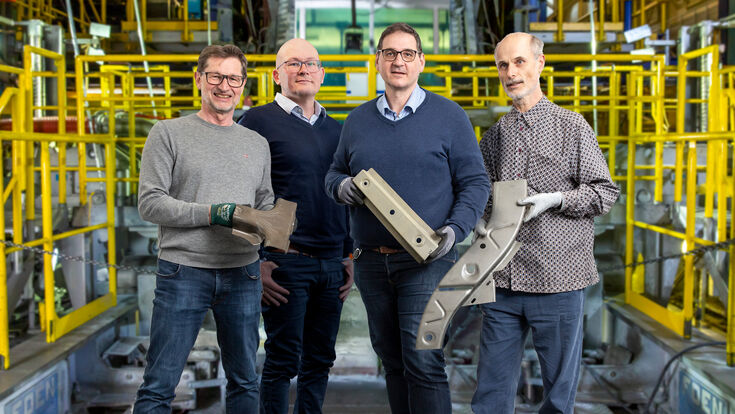
Josef Faderl, Siegfried Kolnberger, Thomas Kurz und Andreas Sommer haben ein Verfahren entwickelt, mit dem leichtere verzinkte Autoteile aus Stahl hergestellt werden können.
- © voestalpinePresshärten ist ein Verfahren zur Herstellung von robustem Stahl, der auch für komplexe Bauteile geeignet ist. Allerdings benötigen solche Bauteile eine zusätzliche Beschichtung, um korrosionsbeständig zu sein. Eine mögliche Beschichtung ist Zink, aber dieses verdampft bei den hohen Temperaturen, die beim Presshärteverfahren entstehen, weshalb die Herstellung einer solchen Beschichtung als unmöglich galt. Eine Lösung auf Zinkbasis wurde dennoch von Josef Faderl, Siegfried Kolnberger, Thomas Kurz und Andreas Sommer entwickelt. Das Team der voestalpine fügte Aluminium hinzu, um die Beschichtung widerstandsfähig gegen hohe Temperaturen zu machen. Das Ergebnis war der sogenannte phs-ultraform-Stahl, der seit 2008 bei der Produktion von rund vier Millionen BMW 5er- und 7er- Modellen eingesetzt wird.
"Am 17. April 2002 trafen wir uns erstmals, um über phs-ultraform zu sprechen", erinnert sich Faderl. "2005 haben wir dann das erste Bauteil mit der Beschichtung produziert und im Herbst 2008 ging die erste Serienproduktion für BMW an den Start."
Formbar trotz Festigkeit
Presshärtender Stahl ist nicht nur extrem fest, sondern auch leichter, formbarer und sicherer als herkömmlicher Stahl. Automobilhersteller können durch die Verwendung dieses Stahls weniger Material beim Bau ihrer Fahrzeuge verwenden, was zu leichteren Autos führt und den Kraftstoffverbrauch senkt. Die Emissionen können so um bis zu 5 % reduziert werden. Zudem ermöglicht die gute Formbarkeit des Stahls die Schaffung von komplizierten Geometrien, die aerodynamischer und damit kraftstoffeffizienter sind und einen besseren Aufprallschutz bieten. Der widerstandsfähige Stahl bietet den Insassen im Falle eines Aufpralls lebensrettenden Schutz.
Das Erfinderteam
Das Team, das phs-ultraform entwickelt hat, besteht aus Experten mit jahrzehntelanger Erfahrung in der Stahlindustrie. Jedes Teammitglied trägt sein spezielles Wissen und Können bei. Siegfried Kolnberger und Josef Faderl sind Absolventen der Johannes Kepler Universität in Linz und haben sich auf technische Physik spezialisiert. Thomas Kurz ist Materialwissenschaftler und Andreas Sommer ist ein erfahrener Ingenieur mit besonderen Kenntnissen in der Finite-Elemente-Simulationstechnologie. Zusammen arbeiten sie an der Weiterentwicklung der Produkte und Verfahren der voestalpine.
Faderl und sein Team gehören zu den drei Finalisten in der Kategorie „Industrie“ des diesjährigen Europäischen Erfinderpreises. Der Preis würdigt die Arbeit von Erfindern herausragender und kommerziell erfolgreicher Technologien, die sich große europäische Unternehmen patentieren ließen. Die Gewinner der Ausgabe 2023 werden am 4. Juli 2023 in Valencia (Spanien) im Rahmen einer feierlichen Zeremonie bekannt gegeben.
(Lesen Sie auch: Stahlerzeugung: Smelter von Primetals und RHI Magnesita soll CO2-Emissionen deutlich reduzieren)