EMO Hannover : Worauf es bei Predictive Maintenance ankommt
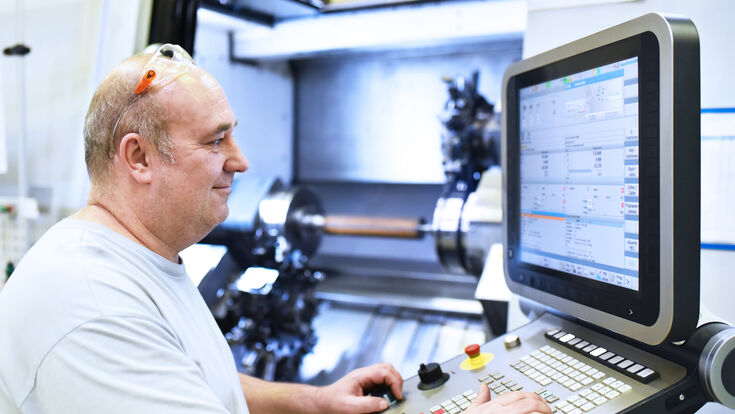
Herr Hohwieler, wie unterscheiden sich Predictive Maintenance (PM), also die vorausschauende Wartung, und Condition Monitoring?
Eckhard Hohwieler: Condition Monitoring erkennt und überwacht den Verschleißzustand, während Predictive Maintenance die voraussichtliche Entwicklung des künftigen Maschinenzustandes vorhersagt und Instandhaltungsmaßnahmen plant.
Herr Geisert, was und wie nützt PM dem Besitzer von Werkzeugmaschinen?
Claudio Geisert: Die Wartung und Instandhaltung orientiert sich am Zustand der Maschine. Die Mitarbeiter führen also genau die Instandhaltung und Wartung durch, die tatsächlich erforderlich ist. Effektive PM senkt die Anzahl an Wartungsarbeiten und erhöht die Verfügbarkeit der Maschinen. Es kommt außerdem zu einer besseren Planbarkeit der Nutzung von Anlagen, weil Wartungs- und Instandhaltungsarbeiten nun zu festgelegten Terminen stattfinden.
Ein Spezialgebiet von Ihnen ist das Prozess-Monitoring und die Zustandsdiagnose: Können Sie uns ein Highlight aus Ihrer Forschungsarbeit nennen?
Hohwieler: Wir haben für einen Maschinenhersteller eine Werkzeugüberwachung ohne zusätzliche Sensoren oder andere Elektronik verwirklicht. Ein in die Steuerung integriertes Softwarepaket kontrolliert Werkzeugverschleiß und -bruch. Auf dieser Basis entwickelten wir weitere Algorithmen, mit denen sich der Zustand und das Verhalten der Maschine checken lassen. Damit kann ein Mitarbeiter anhand der Kennwerte der Antriebsachsen erstaunlich genau Schwachstellen ermitteln: Auf diese Weise wurden sogar Textilfehler in Riemenantrieben entdeckt.
Wo liegen hier die Daten- beim IPK oder dem Unternehmen? Wem gehören die Daten bzw. wer darf sie wie nutzen?
Geisert: Die an der Maschine während der Nutzungsphase anfallenden Daten gehören – sofern nicht anders vertraglich geregelt – dem betreibenden Unternehmen. In der Regel geben die Unternehmen diese Daten nicht nach außen, da sie befürchten, dass sich darunter auch sensible Informationen befinden bzw. sich daraus ableiten lassen. Eine gängige Lösung ist die Installation eines entsprechenden Servers innerhalb des Firmennetzes. Damit geht dem Hersteller allerdings auch wieder die Möglichkeit verloren, zusätzliche Erkenntnisse über das Verhalten seiner Maschinen im Feld zu gewinnen. Um diesem Problem Herr zu werden, ist grundsätzlich eine vertrauensvolle Partnerschaft zwischen Hersteller und Betreiber notwendig; eine vertragliche Absicherung zur Nutzung der Daten ist aber sicher hilfreich.
Wie hat sich diese neue Form der Überwachung bei Ihnen zu PM weiterentwickelt?
Hohwieler: Wir nahmen bei einem Projekt zu eMaintenance unter die Lupe, wie sich Informationen aus dem Condition Monitoring zum Planen von Wartungsmaßnahmen nutzen lassen. Als Hilfsmittel diente ein elektronisches Service-Check-Heft, das die nötigen nächsten Arbeitsschritte angibt. Es erklärt auch, wie der Anwender die Wartungsarbeiten vorbereiten und durchführen soll; und wo er die dazu nötigen Werkzeuge ordern kann.
Gibt es ein Praxisbeispiel für eine PM-Lösung, die Sie mit einem Werkzeugmaschinenhersteller entwickelt haben?
Geisert: Die Automobilindustrie verlangt von den Maschinenherstellern Garantien zur Verfügbarkeit und Angaben zu den erwarteten Lebenszykluskosten. Das erfordert jedoch eine lückenlose Überwachung der Maschine. Unsere mit dem Schleifmaschinenhersteller Schaudt-Mikrosa entwickelte Lösung – eine elektronische Überwachung der Antriebselemente über die Maschinensteuerung – erfasst und wertet sämtliche Meldungen und Signale der Anlage aus. Daraus ermittelt das System das dynamische Verhalten der Antriebsachsen und -spindeln über einen längeren Zeitraum. Diese Lösung kommt mittlerweile in allen Maschinen zum Einsatz.
Wie nutzt das PM-Tool dem Hersteller?
Hohwieler: Schaudt-Mikrosa setzt es bereits als wichtiges Werkzeug der Qualitätssicherung ein – beispielsweise in der Maschinenabnahme oder in der Garantiephase zum Klären der Ursachen für Schädigungen, wie Kollisionen zwischen Antriebselementen, Werkzeugen und Bauteilen.
Geisert: Die Service-Mitarbeiter nutzen das Tool für den Blick zurück: Sie sehen dank der lückenlosen Datenerfassung und -speicherung, wann und unter welchen Umständen Probleme erstmalig auftraten und erkennen so leichter, wie sie sich beheben lassen.
Beim Monitoring und der Zustandsdiagnose fallen sehr große Datenmengen an. Beim Erfassen von 20 Werten (64 Bit) pro Millisekunde speichert die Elektronik laut Aachener Werkzeugmaschinenlabor bei einer 8-Stunden-Schicht bereits mehr als vier Gigabyte. Wie gehen Sie beim Auswerten von derartigen Datenmengen, sprich Big Data, vor?
Hohwieler: Es ist für uns nicht problematisch, weil wir nicht die Rohdaten erfassen, sondern nach dem Motto „Smart Data statt Big Data“ nur die typischen Kennwerte ermitteln und speichern. Ich habe nämlich den Eindruck, dass Big Data oft erst wegen der Möglichkeit zur Speicherung großer Datenmengen und dem Erzeugen von redundanten Datenkopien entsteht. Es ist sinnvoller, vor dem Speichern in der Nähe der Maschine eine intelligente Vorauswahl zu treffen, bevor dann ein reduzierter Datensatz in die Cloud wandert.
Wie kann man sichergehen, dass ein reduzierter Datensatz nicht Effekte übersieht, die dann nicht mehr nachvollziehbar sind? Welche Möglichkeiten gibt es schon, eine Auswahl zu treffen?
Geisert: Die Komprimierung von Rohdaten auf ausgewählte Kennwerte ist immer verlustbehaftet. Somit ist nicht auszuschließen, dass Effekte übersehen werden. Das gilt allerdings auch schon für die Datenerfassung: Welche physikalischen Größen sollen mit welchen Sensoren mit welcher Genauigkeit überhaupt erfasst werden? Ohne ein gewisses Maß an domänenspezifischem Expertenwissen ist ein Monitoring-Konzept nicht umsetzbar.
Um die richtige Auswahl zu treffen, kann man in der Entwicklungsphase Verfahren des „Machine Learning“ nutzen. Diese helfen dem Experten bei der Auswahl aussagekräftiger Kennwerte. Es gilt eigentlich immer, dass für die Entwicklung eines nachhaltigen Monitoring-Konzepts Know-how zur fundamentalen Theorie, gepaart mit Erfahrungswissen, unumgänglich ist.
Was bringt der Einsatz von Predictive Maintenance dem Hersteller auf lange Sicht?
Hohwieler: Es kommt zu einem Flotteneffekt. Im Laufe des Lebenszyklus‘ der Produktionsanlagen beim Kunden fallen nämlich sehr viele Informationen an, mit denen sich der Herstellerservice verbessern lässt.
Bitte Ihre persönliche Vision: Wie könnte – im Zusammenspiel mit Industrie 4.0 – eine optimale PM-Lösung aussehen?
Hohwieler: Denkbar wäre es, dass die Maschine die entstehenden Informationen selbst nutzt, um ihren Prozess zu optimieren oder um den Wartungsservice zu „rufen“.
Was erwarten Sie – auch mit Blick auf Ihre Forschungsarbeit und Predictive Maintenance – von Ihrem Besuch auf der EMO Hannover 2017, der Weltleitmesse für Metallbearbeitung?
Hohwieler: Ich bin sehr gespannt, wie sich die Maschinenhersteller auf das Thema einstellen und welche Apps sie dazu vorstellen. Vielleicht präsentiert auch schon jemand die Werkzeugmaschine 4.0, die twittert und mit der sich der EMO-Besucher über sein Smart Phone verbinden kann.
Vielen Dank für das Gespräch!
EMO Hannover 2017
Vom 18. bis 23. September 2017 präsentieren internationale Hersteller von Produktionstechnologie zur EMO Hannover 2017 „Connecting systems for intelligent production“. Die Weltleitmesse der Metallbearbeitung zeigt die gesamte Bandbreite moderner Metallbearbeitungstechnik, die das Herz jeder Industrieproduktion ist. Vorgestellt werden neueste Maschinen plus effiziente technische Lösungen, Produkt begleitende Dienstleistungen, Nachhaltigkeit in der Produktion u.v.m.