3D-Druck : Wie Ultraschall die Pulveraufbereitung erleichtert
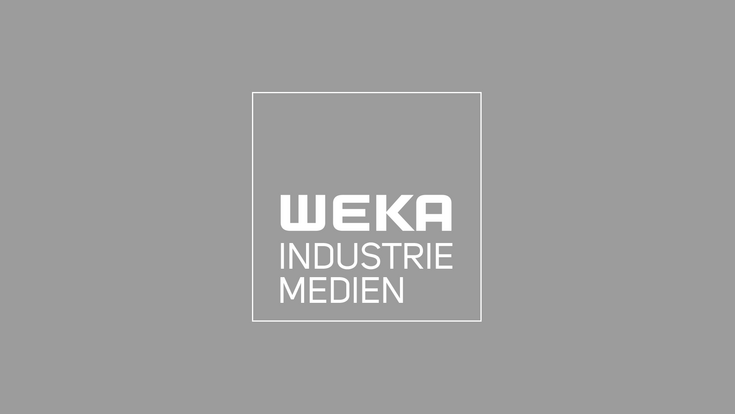
Hinter der Bezeichnung 3D-Druck verbergen sich eine ganze Reihe additiver Fertigungstechnologien. Beim Pulver- oder Pulverbettverfahren werden die Bauteile Schicht für Schicht aufgetragen und abhängig von den Modellkonturen schichtweise verfestig. Bei diesem Verfahren fallen kontinuierlich Pulverrückstände an, die wiederaufbereitet werden müssen, damit die wertvollen Materialien weiterverwendet werden können. Telsonic erleichtert mit seiner Ultraschall-Lösung die Pulverwiederaufbereitung für den 3D-Druck.
Ultraschallsieben für die Pulverwiederaufbereitung
In der Wiederaufbereitungseinheit dieser 3D-Drucker werden die Pulverrückstände deshalb gesiebt, um Verklumpungen oder andere Verunreinigungen zu entfernen. Dabei sind die Anforderungen hoch, da die Pulver sehr fein sind, gleichzeitig aber die Durchlaufzeit kurz und die Trennschärfe hoch sein sollen. Da mechanische Verfahren hier mittlerweile an ihre Grenzen stoßen, bieten sich stattdessen Ultraschallverfahren als Alternative an.
Der Ultraschallspezialist Telsonic hat bereits über 20 Jahre Erfahrung auf diesem Gebiet. Er bietet speziell für den Einsatz in den Pulveraufbereitungseinheiten von 3D-Druckern passgenaue Lösungen für Durchsatzmengen zwischen 10 bis 200 l/h an und unterstützt die Anwender von der Designphase bis zur Integration, damit die jeweilige Lösung perfekt zur Applikation passt. Dabei spielen Faktoren wie Einbaugegebenheiten, Produkteigenschaften und Korngrößenverteilung eine wichtige Rolle. Sind die relevanten Eckdaten ermittelt, lässt sich das optimale Ultraschall-Siebsystem realisieren. Die Effizienz beim Wiederaufbereiten der Pulver steigt dadurch um ein Vielfaches gegenüber den üblichen rein mechanischen Vibrationssiebeinheiten. Die Ultraschall-Siebeinheiten sind zudem einfacher abzudichten als frühere Lösungen und eignen sich dadurch auch gut für den Einsatz in inerten Kreisläufen, wenn mit Pulvern gearbeitet wird, die zur Selbstentzündung neigen, wie z.B. Aluminium-, Magnesium- oder Titanlegierungen. Weitere Argumente, die für die Ultraschalltechnologie sprechen, sind die deutlich geringere Geräuschentwicklung und der durch die Mikrovibration niedrige Verschleiß. Das Verfahren ist umweltfreundlich, energiesparend und vergleichsweise kostengünstig. Dank ATEX- und UL-Zulassung steht zudem einem weltweiten Einsatz der Siebsysteme nichts entgegen.
Funktionsweise des Siebsystems
Ein Ultraschall-Siebsystem besteht im Prinzip immer aus drei Komponenten: einem Generator, einem Konverter und einem darauf abgestimmten Siebresonator mit Einbaurahmen. Der Generator wandelt die normale Netzspannung in Hochfrequenz um und überträgt diese an den Konverter. Der wiederum wandelt die Hochfrequenz mit Hilfe des piezoelektrischen Effekts in Ultraschallschwingungen um, die dann über den Resonator den Siebrahmen zum Schwingen bringen. Die Schwingungen werden an das Siebgewebe abgegeben und dort gleichmäßig verteilt. Die im Bereich zwischen 33 und 37 kHz variierenden Siebschwingungen reduzieren den Reibungswiderstand zwischen dem Siebgut und dem Siebgewebe. Dadurch ist ein effizientes Abreinigen der Siebe ohne Steckkörner gewährleistet, der Durchsatz steigt, die Trennschäfte wird optimiert und der Wiederaufbereitungsprozess läuft schneller ab.