Modellrechnung : Wie Siemens Energie spart ohne zu investieren
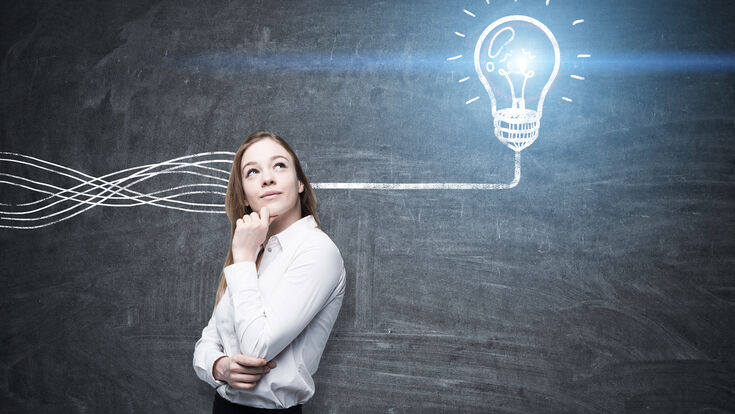
„Mach das Licht aus, wenn du aus dem Zimmer gehst!“ Die familiäre Basisversion eines Energiemanagementsystems dürfte wohl jedem noch aus seinem Elternhaus bekannt sein – simpel, aber effektiv. Legt man das jetzt aber auf ein Unternehmen wie Siemens um, das mehr als 10.000 Menschen an über 20 Standorten in Österreich beschäftigt, ist’s mit einem einfachen Lichtschalter nicht mehr getan. Fertigungshallen, Produktionsanlagen und Bürogebäude mit bis zu 5.500 Mitarbeitern und einem monatlichen Verbrauch im Megawattstundenbereich verlangen ein umfassendes Know-how in Sachen Energieleistungskennzahlen und deren Deutung. Und genau diese Kompetenz ist in der Österreichischen Energieagentur vorhanden. „Deswegen haben wir uns auch zur Zusammenarbeit entschlossen“, erläutert Christian Wölfel, Head of Environmental Protection, Health Management and Safety bei Siemens Österreich.
Verifizierung von Effizienzmaßnahmen
Konkreter Stein des Anstoßes war übrigens eine Schulung der Österreichischen Energieagentur zum Thema Energieleistungskennzahlen, wo Wölfel erstmals auch mit den neuen Ansätzen der ISO 50006 in Berührung kam. Die im Dezember 2014 publizierte Norm liefert Anhaltspunkte, wie der Einfluss von mehreren Variablen durch die Verwendung statistischer Modelle berücksichtigt werden kann. „Bisher wurde versucht den Energieverbrauch meist nur mit Hilfe einer Einflussvariable darzustellen. Dies stellt aber eine grobe Vereinfachung dar, die Ergebnisse weisen dementsprechend nur begrenzte Gültigkeit auf. Für ein seriöses Vorgehen ist es erforderlich, die Einflüsse unterschiedlicher Variablen zu berücksichtigen und voneinander zu trennen“, erklärt Marcus Hofmann, wissenschaftlicher Mitarbeiter und Experte für Messung und Verifizierung von Effizienzmaßnahmen bei der Österreichischen Energieagentur.
Optimieren ohne zu investieren
Bislang hat Siemens – wie die meisten anderen produzierenden Unternehmen auch – mit klassischen Werten gerechnet, à la „Wie viel Energie habe ich pro Stück benötigt?“. „Teilweise hat sich dann aber herausgestellt, dass die Menge der Produktion für den Energieverbrauch völlig unerheblich ist“, erzählt Christian Heckel, Head Governance Environment Protection and Safety bei Siemens. Das ist vor allem dann der Fall, wenn eine Fertigungsanlage über eine hohe Grundlast verfügt, die auch dann anfällt, wenn gar nicht produziert wird. „Ein Trocknungsofen läuft etwa den ganzen Tag, egal ob da zehn oder 100 Transformatoren drinnen liegen“, so Heckel. Nachdem nun quasi nicht mehr nach produzierten Trafos, sondern nach Prozessen „abgerechnet“ wird, fällt es leichter, Energiefresser und Einsparungspotenziale zu identifizieren. „Man schaut jetzt einfach, dass Anlagen effizienter genutzt werden und passt auch seine Fertigungsprozesse dementsprechend an.“
Heckel spricht damit übrigens einen nicht ganz unwesentlichen Vorteil der neuen, modellhaften Berechnung an: Das Optimieren von Prozessen. Für Heckel geht es dabei nicht nur ums direkte Energiesparen: „Wenn ich viel Geld investiere, nur um dann 0,6 Prozent einzusparen, ist das nicht effizient. Effizient ist es, das Vorhandene besser zu nutzen“, fasst es Wölfel zusammen. „Und dank der Modellrechnung kann ich die entsprechenden Hauptprozesse identifizieren“, ergänzt Hofmann. „Wir wären bei einer Werkshalle beispielsweise nie auf die Idee gekommen, dass die Beleuchtung am meisten zur Grundlast beiträgt, obwohl da auch große Maschinen in der Halle stehen“, weist Harald Semper, Energiemanager bei Siemens Gebäudemanagement & Services (SGS), auf ein – durchaus überraschendes – Ergebnis hin. Der größte Benefit ist für ihn, dass die wahre Performance einer Anlage sichtbar wird. So könne er optimieren, ohne etwas investieren zu müssen. So habe man, im Glauben Kosten einzusparen, in einem großen Werk jedes Mal über Weihnachten die Heizung fast abgeschaltet. Nun hat sich aber herausgestellt, dass es mehr Energie kostet, die kalten Räume im Jänner wieder aufzuheizen, als die Heizung (wenn auch reduziert) die ganze Zeit durchlaufen zu lassen.
Strategische Investition
Wenn man sich für ein solches Projekt entscheidet, ist es eine strategische Investition. „Es braucht sehr viel betriebsinterne Bewusstseinsbildung, damit die Leute dann auch dahinterstehen“, erzählt Wölfel aus Erfahrung. Auch sei es nicht immer einfach, die erforderlichen Variablen und Daten im Vorfeld zu identifizieren. „Da muss man manchmal schon sehr kreativ sein“, schmunzelt Semper. Hier ist es sehr hilfreich, wenn einem ein externer Know-how-Träger, wie etwa die Österreichische Energieagentur, zur Seite steht. Der Aufwand halte sich aber in Grenzen und beschränkt sich hauptsächlich darauf die relevanten Daten strukturiert zu sammeln und auszuwerten. Es rechnet sich also, einen detaillierteren Blick auf seinen Energieverbrauch zu werfen – vor allem für Unternehmen, mit entsprechend hohem Energiebedarf.