Condition Monitoring : Wie sich Niederspannungsmotoren überwachen lassen
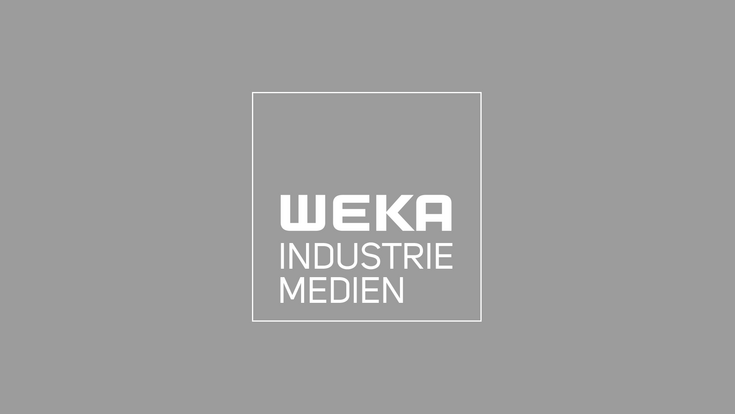
Vorausschauende Wartung spart viel Geld. Nicht zuletzt deswegen hat es Predictive Maintenance inzwischen geschafft, ein zentrales Schlagwort im hippen Industrie 4.0-Universum zu werden. Die Vorteile der Hellseher im Maschinenraum liegen dabei auf der Hand: Mussten Maschinen oder Produktionsanlagen früher erst ausfallen, bis sie repariert wurden, erkennen intelligente Systeme eine Störung heute schon, bevor sie überhaupt auftritt. Somit ermöglicht es diese Technologie, teure Stillstandzeiten zu verringern, Strom zu sparen und in der Folge natürlich auch Wartungskosten zu senken.
Voraussetzung dafür ist aber eine integrierte Maschinenüberwachung, die permanent ein wachsames Auge auf die Bauteile hat – und zwar direkt an beziehungsweise in der Maschine. Das können beispielsweise Sensoren sein, die Vibration, Temperatur oder Feuchtigkeit messen. Diese Messdaten werden von einer intelligenten Wartungs-Software erfasst und ausgewertet. Kommt es zu Unstimmigkeiten innerhalb der Sensordaten, identifiziert die Software den Fehler und warnt frühzeitig vor einem möglichen Ausfall. Defekte Komponenten, die womöglich bald zum Stillstand der Anlage führen, werden so unabhängig von den üblichen Wartungszeiten identifiziert und können ausgetauscht werden, bevor tatsächlich ein Schaden entsteht.
Sensortechnik teurer als Motor
So viel zur bunten Theorie. In der Praxis läuft’s freilich nicht immer so rund. Und wie so oft liegt der Grund dafür in der Wirtschaftlichkeit. Während nämlich aufwändige und teure Motoren inzwischen serienmäßig mit allerlei Sensoren ausgestattet werden, sucht man diese in preiswerteren Modellen vergeblich. „Es würde ja auch wenig Sinn machen, wenn ich in einem Niederspannungsmotor, der vielleicht 600 Euro kostet, Sensortechnik verbaue, die schlussendlich teurer ist, als der Motor selbst“, erklärt Gerald Lippitsch. Er ist Ausbilder beim Berufsausbildungszentrum (BAZ), einer Abteilung des BFI Wien und leitet dort Facharbeiter-Intensivausbildungen mit Lehrabschlussprüfungen in Elektro-Berufen.
Meist nur reaktive Überwachung
Zwar würden solche Motoren freilich kaum in kritischen Produktionsanlagen zum Einsatz kommen, in Lüftungen oder Kühlgebläsen aber beispielsweise sehr wohl. Fällt dieser Motor dann aus, wird’s sehr oft auch mit der reibungslosen Produktion schwierig. „Wenn eine externe Kühlung versagt, hilft es mir auch nichts, wenn ich die teure Produktionsanlage selbst, von A bis Z überwache“, so Lippitsch. „Ziel einer smarten Fabrik muss daher eine flächendeckende Überwachung sein, und da zählen natürlich auch die so genannten mittelkritischen Motoren dazu. Bislang war das aber ein Kosten/Nutzen-Problem, da die Sensoren recht teuer in der Anschaffung und kompliziert zu montieren waren“, erzählt Lippitsch. Das betrifft vor allem Motoren, die bereits verbaut und seit Jahren im Einsatz sind. „Hier rechnet sich eine nachträgliche Verkabelung kaum“, weiß Lippitsch, „Heutzutage werden die meisten Niederspannungsmotoren nicht überwacht und nur reaktiv gewartet. Die Motoren laufen also, bis sie verrecken. Wann das sein wird, kann man natürlich nicht sagen, da die klassische Motorschutztechnik keine Statusberichte liefern kann.“
ROI unter einem Jahr
Eine praktikable Lösung für das Problem könnten also Sensorpakete sein, die kostengünstig sind und sich – selbstverständlich auch nachträglich – ohne großen Aufwand montieren lassen: Im Idealfall rechnet man hier von einem Return on Invest (ROI) von unter einem Jahr. Genau diese Vorzüge will ABB mit seinem Ability Smart Sensor bieten, dessen Schlüsselelement ein kleines Sensortag mit einer drahtlosen Kommunikationsschnittstelle ist, das direkt am Motorgehäuse angebracht wird. Dazu ist noch nicht einmal qualifiziertes Personal nötig, von einer nachträglichen Verkabelung ganz zu schweigen. Außerdem beschränkt sich die Lösung nicht auf Neumotoren oder ABB-Modelle, auch Motoren anderer Hersteller lassen sich problemlos damit nachrüsten. Genau genommen steht der volle Funktionsumfang derzeit für alle dreiphasigen Käfigläufer-Asynchronmotoren (Niederspannung) zur Verfügung. Die Sensoren können an Motoren befestigt werden, die sich im kontinuierlichen, nicht dynamischen Betrieb befinden (S1). Dies ist günstigenfalls ein direkter 50/60-Hz-Netzanschluss, allerdings sind auch Frequenzumrichter-Betrieb ohne dynamische Anwendung und nicht benutzte Dahlander- oder Parallelwicklungskonfigurationen möglich.
Automatischer Datenupload
Einmal am Motor montiert liefert das Sensorsystem Informationen zu den Betriebsparametern wie Vibrationen, Temperatur oder Überlastung und ermittelt zusätzlich auch den Energieverbrauch mit einer Genauigkeit von +/- 10 Prozent. Die Daten werden drahtlos und mit Hilfe von Standardprotokollen an sichere ABB-Server geschickt – derzeit allerdings noch mit einer kleinen Einschränkung: Noch müssen die Daten nämlich mithilfe einer Smartphone-App (via Bluetooth) manuell „abgeholt“ werden. „Noch im ersten Quartal werden wir aber ein Gateway vorstellen, mit dem der Datenupload in die Cloud dann vollkommen automatisch funktioniert“, verspricht Thomas Herdegen, Sales Service Drives & Controls, Motors & Generators bei ABB.
Fitnessarmband für Elektromotoren
In der ABB-Cloud analysiert dann eine spezielle Software beziehungsweise ein spezieller Algorithmus die Daten und verwandelt sie in verwertbare Informationen, die der Anwender dann wiederum auf sein Smartphone oder sein internetbasiertes Kundenportal geliefert bekommt. Tritt ein Problem auf, gibt das System eine Warnmeldung an den Bediener aus und signalisiert über ein Ampelsystem Wartungsbedarf. „Wir sehen den Smart Sensor gerne als Fitnessarmband für Elektromotoren. Ein Servicesystem, dass mit geringem Aufwand und Kosten, Informationen über den Zustand eines Motors liefern kann“, so Herdegen. Dem muss auch Lippitsch beipflichten, der die ABB-Sensoren gerade einem Härte- und Ausdauertest unterzieht. „Eines ist natürlich klar: Die Sensoren liefern keine Echtwerte, aber die brauch ich dafür ja auch nicht. Es werden Trendkurven dargestellt, mit deren Hilfe man aufkommende Probleme erkennen kann.“
Aktuell sind Algorithmen wurden für die Erkennung von Lagerstörungen, Vibrationen und Temperaturwerten im Einsatz. Durch regelmäßige Updates ist allerdings geplant, schrittweise weitere Funktionen hinzuzufügen.
Kosten sparen
Gleichzeitig kann die Analyse der gespeicherten Daten auch neue Wege für die Optimierung von Betrieb und Wartung von Anlagen eröffnen, etwa durch Informationen über den Energieverbrauch der Motoren zur Erstellung effizienterer Lastprofile. „Läuft ein Motor beispielweise immer nur mit 60 Prozent Auslastung, wäre es sicher eine Überlegung wert, diesen gegen einen kleineren zu tauschen“, erklärt Herdegen.
Hinzu kommt natürlich, dass eventuelle Folgeschäden, die durch den Ausfall einer Komponente auftreten können, verhindert werden. Mit dem Ergebnis, dass auch Reparatur- und Stillstandkosten erheblich geringer ausfallen.
3 Gründe, wieso Niederspannungsmotoren heute kaum überwacht werden…
Es ist eine entsprechend anspruchsvolle Infrastruktur erforderlich, die häufig mehr kostet als die Motoren selbst.
Die Überwachungseinrichtungen müssen von Fachpersonal installiert und gewartet werden.
Ohne eine korrekt aufgebaute Infrastruktur hat das Wartungsteam keine ausreichenden Daten für Optimierungsmaßnahmen.
…und 3 Gründe, wieso Sie es trotzdem tun sollten:
Stillstandzeiten werden bis zu 70 Prozent reduziert, indem man Motoren wartet und ersetzt, bevor diese ausfallen.
Die Lebensdauer der Motoren wird bis zu 30 Prozent verlängert, indem Probleme beseitigt werden, bevor Sekundärschäden auftreten.
Der Energieverbrauch der Motorinstallationen wird um bis zu 10 Prozent reduziert, da Lastprofile optimiert und überdimensionierte Motoren ersetzt werden können.