Kennzahlen und Echtzeitinformationen : Wie MES die Fertigung optimiert
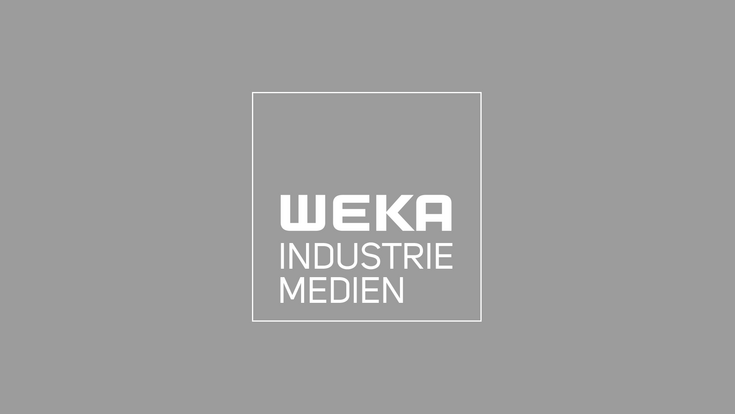
Aus der Vielzahl an Funktionalitäten von MES ergeben sich verschiedene Einsatzmöglichkeiten. Das kann von einer vergleichsweise „simplen“ Maschinendatenerfassung bis hin zu einer vollständig digitalisierten Fertigungsumgebung reichen. “In erster Linie schafft ein MES Transparenz und unterstützt das Erkennen von Optimierungspotenzialen. Dies erreicht man vor allem durch die Schaffung eines digitalen Abbildes der Fertigungsumgebung", erklärt Bernhard Falkner, CTO Industrie Informatik.
Relaistische Planung und aussagekräftige Zahlen
Der Nutzen unterscheidet sich, je nach Anwendungsfall: Stihl Tirol, Hersteller von Rasenmähern und Motorsägen, generiert mit der MES-Lösung Cronetwork automatisch Informationen zu produzierten Geräten. “Bei Stihl wollte man mehr Transparenz für weitere Optimierungsmaßnahmen. Neben der Einzelteilrückverfolgung und transparenten Visualisierung von Fertigungsfortschritten, realisierten wir in den Ausbaustufen die Qualitätsdatenerfassung,” erzählt Falkner. Die Anzahl an Montagelinien und hohe Produktdiversifikation machte es notwendig, dass ein MES bei Stihl flexibel an die Gegebenheiten in der Fertigung angepasst werden kann. “Ein anderes Anwendungsbeispiel ist der Automobilzulieferer Thomas Magnete. Hier unterstützten wir bei der Prozessdatenerfassung", berichtet Falkner. Für den effizienten Betrieb der unterschiedlichen Fertigungsbereiche werden bei Thomas Magnete im Shopfloor-Management OEE-Kennzahlen genutzt. Anfangs wurden die Fertigungskennzahlen manuell erfasst, bald zeigten sich die Schwächen. Seither sind die Daten in Echtzeit über das Produktionsleitsystem verfügbar.
Einfluss von Entwicklungen oder Konzepten
Mit IIoT (Industrial Internet of Things) sind neue Technologien und Disziplinen ins Spiel gekommen, die die Digitalisierung in der Industrie nachhaltig prägen. “Datensammlung und -aufbereitung aus der Fertigung ist seit jeher Hoheitsaufgabe des MES. Ein zukunftsträchtiges und effizientes IIoT hat allerdings die besten Chancen, wenn ein MES-System seine Flexibilität in Datenerfassung und Informationsaufbereitung voll ausspielen kann und gleichzeitig mit dem kaufmännisch führenden ERP-System harmoniert", sagt Falkner. Eine wichtige Basis dafür liefern Standards wie OPC UA und Webservices. Auch die umfassende Interaktion mit der Automatisierungsebene ist erfolgsentscheidend.
Fertigungsplattform der Zukunft
Falkner beobachtet die Entwicklungen am Markt genau. Aus seiner Sicht unterliegt die Automatisierungspyramide einem Wandel und wird sich in kommenden Jahren nach und nach auflösen. Monolythische, abgeschottete Softwaresysteme weichen flexiblen Anwendungen, Prozessen und Microservices. “Ein MES alleine wird die steigenden Anforderungen an eine digitale Fabrik nicht mehr abbilden. Vielmehr wählt der User künftig seine ‚Bausteine‘ aus – und zwar unabhängig von Hersteller und technologischer Basis", erklärt Falkner. Eine zukunftsfähige Fertigungsplattform verbindet (Einzel-)Komponenten und orchestrieret sie. Grundvoraussetzung dafür ist die Öffnung dieser Plattform in Richtung einer wachsenden Systemlandschaft und den damit verbundenen Chancen und Möglichkeiten. “Eigene, periphere und fremde Lösungen müssen problemlos angebunden und integriert werden können. Der Schlüssel liegt in einer, auf Standards basierenden, (z.B. OPC, REST-Services (OpenApi),…) – offenen Schnittstellen- und Kommunikationsebene, die genau das möglich macht,” erklärt der CTO von Industrie Informatik.
Entwicklung von MES
Nach Einschätzung von Falkner sind Unternehmen, die noch gar keine automatisierte Anbindung und Nutzung von Maschinendaten haben, sehr selten: “Am anderen Ende ist eine vollumfängliche Nutzung der MES-Funktionalitäten in allen Modulen ebenso noch die Ausnahme. Dazwischen ist viel Platz und Bewegung.” Aus Sicht des Experten ist einer der nächsten großen Schritte in diesem Bereich die Etablierung von Predictive Analytics. Das Linzer Softwarehaus untersucht in einem gemeinsamen Projekt mit der TU Wien, wie sich anhand erfasster Daten zu Ereignissen und Fakten – beispielsweise Ausschussmengen, Störungen, den Einfluss von Wartungsdurchführungen – etwa Störungswahrscheinlichkeiten und Fertigungsqualität prognostizieren lassen. Dazu werden Methoden der KI angewandt, da Datenkonstellationen je Unternehmen variieren und ein MES-System wie Cronetwork aus verschiedenen Situationen im Live-Betrieb lernen muss.