Eine zu 100% flexible Produktion : Wie könnte eine flexible Fertigung à la smart production aussehen?
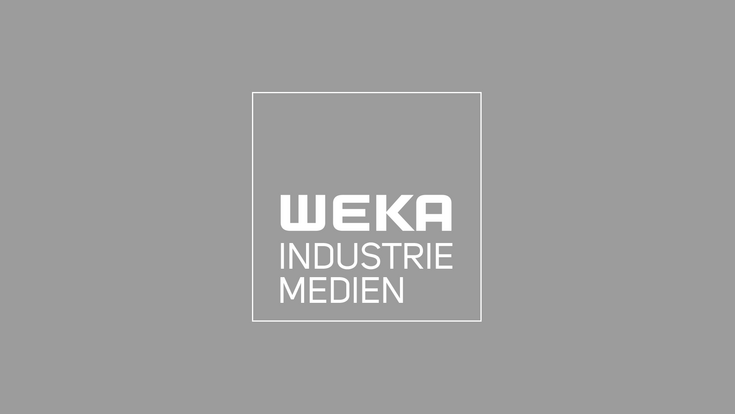
Smart production – flexible Logistiklösungen für die Produktion
Heute sind klassische Fertigungslinien oft nicht mehr wirtschaftlich. Überall dort, wo die Veränderungen groß oder die Stückzahlen gering sind, wird sich eine Investition in eine Produktionslinie auf viele Jahre nicht mehr rechnen. Fertigungslinien müssen sehr dynamisch arrangiert und schnell auf Änderungen anpassbar sein. Das stellt sehr hohe Anforderung an die Logistik, die Technik und auch an den Customer Service-Bereich. Folglich müssen auch die Logistiksysteme immer flexibler werden, um etwaigen Änderungen im Fertigungsprogramm folgen zu können. Flexible und maßgeschneiderte Lösungen von KNAPP sind genau an diese Anforderungen angepasst. Eine Kombination aus 3D-fähigen automatischen Lagersystemen, autonomen mobilen Robotern und innovativen Arbeitsplätzen mit Bildverarbeitungssystemen zur Qualitätssicherung bilden die Grundlage für flexible Logistiklösungen.
Flexibel, skalierbar und leistungsstark – OSR Shuttle™ Evo
Das Kernelement einer flexiblen Lösung bildet ein 3D-fähiges Shuttlelager, wo Teile entsprechend bevorratet sind. Das OSR Shuttle™ Evo bildet das Herzstück von zahlreichen logistischen Anwendungen und ermöglicht das effiziente und platzsparende Lagern, Kommissionieren, Puffern und Sequenzieren von Waren, Aufträgen und Rohstoffen sowie das Versorgen von Arbeits- und Assemblierarbeitsplätzen. Es ist mit der gesamten logistischen Lösung vernetzt, modular aufgebaut und skalierbar. Mit einer maßgeschneiderten Software werden die Prozesse jeder Anforderung abgedeckt.
Flexible Produktionsversorgung durch Open Shuttles
Mit den autonomen mobilen Robotern – den Open Shuttles – werden Materialien direkt und ohne bauliche Maßnahmen zu Arbeitsplätzen, in bestimmte Lagerbereiche oder an die Fertigungslinie transportiert. Die Shuttles navigieren autonom, weichen Hindernissen aus und arbeiten gemeinsam im Schwarm. Eine schnelle und effiziente Auftragsabwicklung ist somit möglich. In Kombination mit dem Lagersystem kann eine optimale Arbeitsplatzversorgung sichergestellt werden. Durch die verschiedenen Open Shuttle-Typen ist es möglich, unterschiedlichste Behältnisse zu transportieren und eine gemischte Flotte für diverse Warentransporte zusammenzustellen.
Zero Defect Production durch Augmented Reality
Neben einer sequenzierten und flexiblen Versorgung der Fertigung, spielt auch die Qualität eine große Rolle. Fehler in der Produktion und Assemblierung müssen möglichst geringgehalten werden. Mit der zero defect production-Lösung von KNAPP wird die Null-Fehler-Strategie Wirklichkeit. Die Produktions- und Assemblierungsarbeitsplätze sind mit innovativen Bilderkennungs- und Bildverarbeitungssystemen ausgestattet und erfassen jede Komponente, die im Produktionsprozess verbaut wird. Der Mitarbeiter erhält dank Echtzeit-Feedbacksystem sofortige Rückmeldung über die Qualität jedes Arbeitsschrittes. Ein fehlerfreier Zusammenbau sowie eine lückenlose Verfolgbarkeit können sichergestellt werden.
Wo Zero Defect Alltag ist
Pankl High Performance Systems oder implantcast setzen bereits auf eine flexible zero defect-Lösung.
https://www.youtube.com/watch?v=TfvYvshrEnE]
Pankl produziert Hochleistungsgetriebe für Motorradanwendungen für KTM. Neben der hohen Leistung spielt optimale Qualität in allen Prozessen eine wichtige Rolle. Halbfertigteile und Schüttgut lagern zentral im 3D-fähigen Shuttlelager. Für die Montage lagern Shuttles die benötigten Teile aus und bringen sie direkt zu den Arbeitsplätzen ivii.smartdesk. Die Montage ist durch ein Echtzeit-Feedbacksystem zu 100% softwaregestützt. Das System erfasst während der Montage alle Teile, prüft ob sie korrekt verbaut wurden und informiert den Mitarbeiter über das Ergebnis. Grün bedeutet: alles korrekt. Rot bedeutet: Fehler. Im Fehlerfall unterstützt ivii.smartdesk bei der Richtigstellung. Die KNAPP-Lösung vereint maximale Leistung und Effizienz mit Null-Fehlerstrategie und schafft ein modernes Arbeitsumfeld für die Mitarbeiter.
Auch das Medizintechnikunternehmen implantcast hat sich für eine flexible Lager- und Kommissionierlösung von KNAPP entschieden. Neben dem skalierbaren und an das Unternehmenswachstum anpassbaren Lager, wurden ergonomische Pick-it-Easy Arbeitsplätze mit Augmented Reality ausgestattet. Das skalierbare automatische Kleinteilelager ermöglicht eine ergonomische und schnelle Zubringung der Teile an die Arbeitsplätze. Auch bei zukünftigem Unternehmenswachstum kann das Lager in Größe und Leistung angepasst werden. Durch die RFID-Technik und die Vision-Technologie konnte die Kommissionierproduktivität und Auslieferqualität wesentlich gesteigert werden. Eine dreifache Überprüfung der einzelnen Teile gewährleistet eine 100%ige Qualitätssicherung und sorgt dafür, dass beim Endkunden das richtige Produkt ankommt. Gerade in diesem sensiblen Bereich der Medizinprodukte, wo jeder Fehler mit großem Leid verbunden wäre, hat die Qualität einen noch höheren Stellenwert.
Interessieren Sie sich für unsere Lösungen im Detail? Dann besuchen Sie uns auf unserer Website.
Wir freuen uns Sie auf der LogiMAT 2020 (10.-12.03.2020, Messe München) in Halle 3 | Stand B05 begrüßen zu dürfen.
(Entgeltliche Einschaltung)