Instandhaltung : Wie Infineon "Predictive Maintenance" gelingt
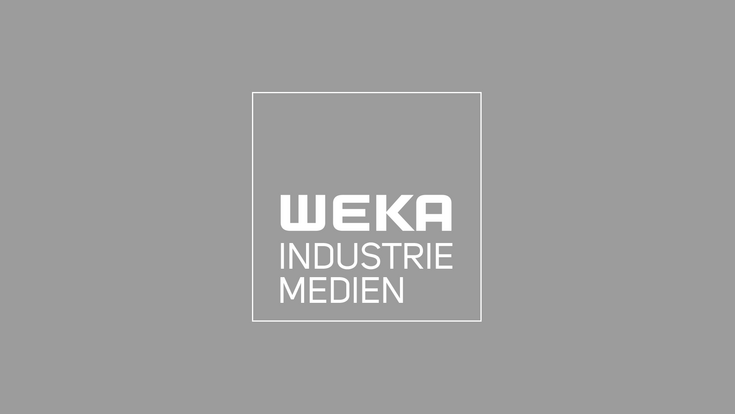
Sie werden geätzt, belichtet, gebacken und gewaschen: Die hauchdünnen Siliziumscheiben, die bei Infineon Austria gefertigt werden, durchlaufen etliche Stationen, bis sie schließlich das Villacher Werk verlassen. Bis zu 1.000 Einzelarbeitsschritte sind bei jedem einzelnen Wafer nötig. Umso wichtiger ist es, dass „das Werkl rennt“: Fällt eine der Anlagen in dem verzweigten Produktionsprozess aus, hat das Auswirkungen auf nachfolgenden Prozesse. Seit jeher ist es daher das Ziel von Infineon, Systemunterbrechungen zu vermeiden. Und die aktuellen Werte können sich durchaus sehen lassen: Die Verfügbarkeit der Anlagen liegt deutlich bei über 90 Prozent. „Das ist schon sehr gut, aber noch zu wenig“, bringt es Peter De Boer, Data Scientist bei Infineon, auf den Punkt. Um die letzten fehlenden Prozentpunkte auszumerzen, wurde deshalb mit Fraunhofer Austria und dem AIT (Austrian Institut of Technology) getüftelt. Unter dem Titel „Smart data 4 maintenance“ analysierte man die Sinnhaftigkeit von vorschauenden Instandhaltungsaktivitäten (Predictive Maintenance). Und das Ergebnis gleich vorweg: Es macht Sinn. De Boer berichtet: „Wir haben gesehen, dass es gut funktioniert und arbeiten nun daran, das Ganze weiter auszurollen.“
Nach dem Sammeln kam das Ordnen
Bis es soweit war, musste man aber wahre Daten-Knochenarbeit leisten. „Unsere größte Herausforderung war das Sammeln und Einordnen der Daten. Wir verfügen insgesamt über eine Unmenge an Daten, dazu sehr viele unterschiedliche Datenquellen und -formate“, so De Boer. Es galt, einen gemeinsamen Nenner zu finden. Oder um es fachlich richtiger zu sagen: „Die Daten mussten aus den unterschiedlichen Datenquellen aufbereitet und in eine gemeinsame Datenbasis gebracht werden“, wie es Robert Glawar, Projektleiter bei Fraunhofer Austria, beschreibt. Erst dann konnte mit der Arbeit an einem Prognosealgorithmus begonnen werden.
Mitarbeiter an Bord holen
Dafür nahm man eine bestimmte Anlage ins Visier – und zwar eine Ätzungsanlage. Es hätte auch eine der vielen anderen Anlagen bei Infineon sein können. Dass es diese wurde, liegt nicht an technischen Parametern, sondern hat menschliche Gründe: Die Instandhaltungsteams wurden gefragt, wer bei einem solche Pilotprojekt mitwirken wolle. Und dieses war das Erste, das sich meldete. „Für uns war es wichtig, Mitarbeiter einzubinden, die offen für das Thema sind“, sagt Peter De Boer. Wie schnell und flächendeckend Predictive Maintenance künftig bei Infineon zum Einsatz kommen wird, hänge ebenfalls von den Mitarbeitern ab. „Wir sind jetzt dabei ein Tool zu bauen, das uns tägliche Vorhersagen für die Anlagen liefert. Danach starten wir eine Testphase, die sicher mehrere Monate dauern wird.“ Der Test solle vor allem zwei Fragen beantworten: „Kriegen wir das technisch hin? Und „Werden diese Vorhersagen tatsächlich genutzt?“
Ungenauigkeit in den Vorhersagen
Spannend werde vor allem die Antwort auf die zweite Frage, meint der Infineon-Data Scientist: „Die Algorithmen berechnen eine bestimmte Wahrscheinlichkeit. Die Vorhersagen sind nicht schwarz-weiß, sondern es gibt immer eine Ungenauigkeit.“ Das könne dann beispielsweise so lauten: „Es gibt eine 70%-ige Wahrscheinlichkeit für den Ausfall der Anlage XY in den nächsten zwei bis drei Tagen.“ Das Zusammenspiel von Technik, Algorithmen und dem Faktor Mensch ist ein noch relativ wenig erforschtes Gebiet. Hier kommt es auf den Versuch in der Praxis an. Auch Robert Glawar sagt: „Ein funktionierender Algorithmus alleine ist zu wenig.“ Erst, wenn der Mensch aus den dadurch gewonnenen Informationen einen Nutzen ziehen könne, mache der Algorithmus einen Sinn. „Wir haben uns bei dem Projekt deshalb darauf konzentriert, worauf es für einen Instandhalter ankommt.“ Das könne beispielsweise die Frage sein, wann bestimmte Ersatzteile benötigt werden oder welche Probleme in den kommenden Tagen höchstwahrscheinlich auftreten werden. Durch diese Informationen könne man Werkzeuge, Material und Mitarbeitereinsatz besser im voraus planen.
Viele Vorteile, aber großer Aufwand
Für ein bestimmtes Zeitfenster können „die besten Algorithmen“ Infos mit einer Wahrscheinlichkeit von bis zu 90 Prozent liefern. „Und das auch nur für einen bestimmten Zeitraum: nämlich für die kommenden zwei bis drei Tage. Sehr kurzfristige Prognosen hingegen sind schwierig, langfristige auch.“ Glawar hat deshalb Verständnis dafür, dass viele Unternehmen dem Thema noch kritisch gegenüberstehen. „Predictive Maintenance bietet viele Vorteile. Man kann Stress-Situationen vermeiden, Maßnahmen gezielt planen und Ressourcen sparen. Aber es gibt rund um die Digitalisierung insgesamt sehr viele Möglichkeiten am Markt. Hier muss man abwägen und sich auch darüber im Klaren sein, dass eine neue Technologie auch mit einem gewissen Aufwand verbunden ist. Schließlich muss man diese auch anwenden können.“ Im Fall von Infineon habe man beispielsweise rund ein Jahr lang an der erfolgreichen Implementierung von Predictive Maintenance gearbeitet – und die Testphase wird nun ebenfalls mehrere Monate dauern. „Wir brauchen eine gewisse Zeit, um die Kollegen damit arbeiten lassen zu können. Erst dann werden wir die Ergebnisse analysieren können“, so Peter De Boer.