Smartes Tracking : Wie BMW Regensburg seine Fertigung vernetzt
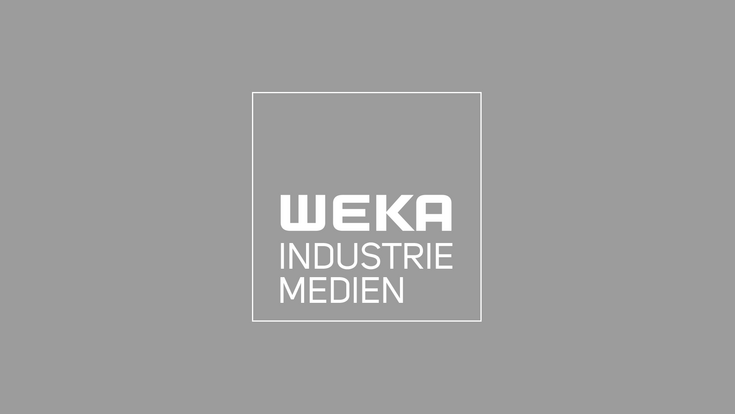
Für die Produktion bei BMW sind neue Zeiten angebrochen: Innovative Technologien im Bereich „Enterprise Location Intelligence“ bringen mit ihren intelligenten Ortungssystemen Klarheit in die Komplexität der Prozesse und steigern messbar die operative Effizienz. Dank der „Smart Factory“-Lösungen von Ubisense ist es somit gelungen, Materialien, Werkzeuge, Komponenten bzw. ganze Fahrzeuge genau zu identifizieren, lokalisieren und nachzuverfolgen. Und die Ergebnisse können sich sehen lassen: Präzise Informationen zum Fertigungsablauf in Echtzeit, Daten zur adaptiven Steuerung sowie datengestützte Einsichten.
Die Herausforderung
Das BMW-Werk in Regensburg produziert pro Tag über 1.000 unterschiedliche Modelle an einer Fertigungslinie für die verschiedensten Kundenwünsche. In einer herkömmlich organisierten Produktion sind Verzögerungen und Ausfälle bei so vielen gleichzeitig ablaufenden Prozessen kaum zu überwachen. BMW beabsichtigte vor dem Hintergrund der technologischen Möglichkeiten der Lösungen von Industrie 4.0, eine Fertigung zu etablieren, die mehr Transparenz bietet. Das heißt, ineffiziente Abläufe eliminieren und von deutlichen Kosteneinsparungen und Produktivitätssteigerungen profitieren.
Die Lösungsfindung
Die „Smart Factory“-Lösungen von Ubisense beziehen sich nicht nur auf eine reine Ortungslösung, die Koordinaten erzeugt, sondern sie bestehen aus einer Hardware- und Software, die u. a. Fahrzeugkomponenten präzise identifizieren und eine automatische Werkzeugkonfigurierung auf der gesamten Fertigungslinie sicherstellen. Die Positionsinformationen werden über den „Angle of Arrival“ (AoA), der Empfangswinkel, und dem „Time difference of Arrival“ (TdoA) gewonnen. „Das ist ein wesentlicher Unterschied zu anderen Systemen, die nur mit „Time of Flight“ oder RSSI arbeiten“, sagt Uwe Zylka, Senior Technical Consultant von Ubisense. „Mit diesen Informationen ist es bereits mit zwei Sensoren möglich, eine exakte 3D-Position des Tags zu berechnen.“
Reporting von Bewegungsdaten
Die 3D-Ortsinformationen der „getrackten“ Objekte werden nun in Bezug zu definierten Zoneninformationen gebracht. Das heißt, das System erkennt, ob sich ein Objekt in eine Zone hineinbewegt oder wieder aus der Zone austritt. Auf Basis dieses Grundprinzips sind die Geschäftsapplikationen in der Software aufgebaut. Dazu gehören: Steuerung der Freigabe von Werkzeugen in der Automobilindustrie, Yard-Management von Fahrzeugen (Automobilproduktion, Depots von Verkehrsbetrieben), LEAN-Production, Unterstützung der papierlosen Fertigungsprozesse, automatische Rückmeldung von Montageaufträgen in das MES, ERP, Steuerung bzw. Optimierung von logistischen Prozessen, Optimierung der Kameraüberwachung von Umschlaglagern, Aufzeichnung und Reporting von Bewegungsdaten (Verweildauer von Aufträgen, Materialfluss etc.) und Kapazitätsüberwachung von Montagebereichen.
Ablaufsichtbarkeit
Die Standzeiten der Tags sind außerordentlich groß. Mehr als acht Jahre hat zB ein Industrial-Tag bei 1Hz Update-Rate. Ubisense stellt Module für die Applikationssoftware zur Verfügung, die die reinen 3D-Ortsinformationen sinnvoll übersetzen. Denn ERP-Systeme können zum Beispiel nichts mit einer x,y,z-Koordinate anfangen. „Durch den Einsatz von Standortdaten, die durch das ‚Best-in-class real-time location‘-System (RTLS) gesammelt werden, sowie von Produktionsdaten aus den Fertigungs- und Enterprise-Systemen, entsteht eine noch nie dagewesene Ablaufsichtbarkeit und –kontrolle“, erklärt Zylka. Auf diese Weise sammelt das Echtzeitortungssystem Standortdaten über den ganzen Fertigungsprozess hinweg, verbindet diese mit Informationen anderer Unternehmenssysteme und liefert so fundierte Grundlagen für Geschäftsentscheidungen.
Kosten der Werkzeugsteuerung eingespart
Mit der Implementierung von „Smart Factory“ von Ubisense konnten die Kosten der manuellen Werkzeugsteuerung vollständig eingespart werden. Insgesamt konnten die Bandstillstände minimiert, Durchlaufzeiten deutlich erhöht, täglich hunderte Stunden Leerlauf eingespart, das Fehlerrisiko reduziert und der Umfang der Nacharbeit minimiert werden. Auf Grund der erheblich transparenteren Herstellungsprozesse und den stets aktuellen Daten sind nun Entscheidungen möglich, die eine weitere kontinuierliche Optimierung der Vorgänge an der Anlage ermöglichen. „Fahrzeughersteller auf der ganzen Welt sind mit den gleichen Herausforderungen konfrontiert“, erklärte Richard Green, CEO von Ubisense. „Unsere ‚Smart Factory‘-Technologie ermöglicht es unseren Kunden, Einzelheiten zu sehen, die vorher nicht sichtbar waren. Dadurch erhalten unsere Kunden die Möglichkeit, Engpässe beim Fertigungsprozess zu erkennen und zu korrigieren, womit sie wesentlich mehr Einfluss auf die Herstellung haben.“