Flexible Fertigung : Wie BMW künftig Antriebe produzieren will
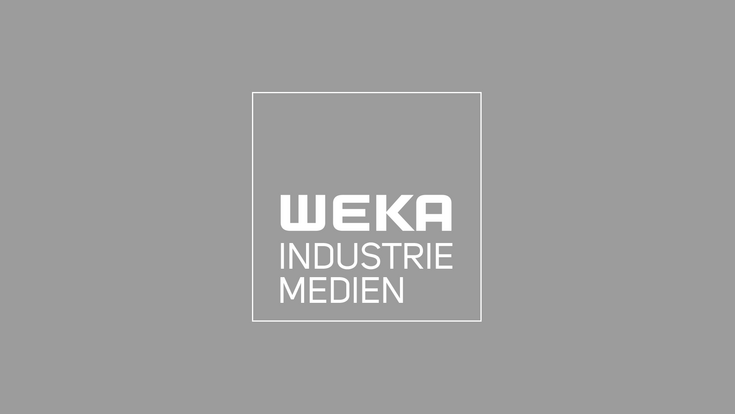
Zwei Fakten sind gleich mal festzuhalten: Der Trend zur Elektromobilität ist irreversibel. Gleichzeitig werden Märkte und Kunden auf der ganzen Welt noch lange sehr verschiedene Antriebsysteme nachfragen. Das heißt, der Trend wird sich über den Globus sehr unterschiedlich und vor allem unterschiedlich schnell durchsetzen. Somit bleiben noch viele Fragen offen: Wann genau und auf welchen Märkten werden wir eine stark steigende Nachfrage nach vollelektrischen Fahrzeugen sehen? Wie stark und mit welcher zeitlichen Verteilung werden Kunden Plug-in-Hybride kaufen? Wie genau wird sich die Nachfrage nach Verbrennungsmotoren weiterentwickeln? All diese Fragen kann heute niemand zuverlässig beantworten. Deshalb hatte sich die BMW Group bereits 2010 entschieden, ab dem nächsten Jahrzehnt in allen Klassen Autos aller Antriebe anzubieten. „Das heißt, moderne, effiziente und saubere Verbrenner, Plug-in-Hybride sowie ein vollelektrischer Batterieantrieb“, konstatiert Markus Grüneisl, Leiter Produktionssystem, Digitalisierung bei BMW. Für 2025 schätzt der Hersteller, dass zwischen 15 und 25 Prozent der verkauften Fahrzeuge von BMW elektrifiziert sein werden. In absoluten Zahlen können das 700.000 oder auch nur 400.000 Elektro- oder Hybrid-Fahrzeuge sein.
Systemintegration für komplexe Produkte
Damit folgt BMW der Strategie einer Systemintegration und richtet sich auf ungewisse Marktprognosen der Elektromobilität aus. Die große Herausforderung für die gesamte Automobilindustrie besteht dabei in der Lieferfähigkeit innerhalb effizienter Kostenstrukturen. „Entscheidend ist für uns die Auslastung unserer Werke. Wie sich die Nachfrage nach Elektrofahrzeugen entwickeln wird, wissen wir aber noch nicht präzise. Deshalb werden wir künftig aus Gründen der Flexibilität Elektro- und Verbrennerfahrzeuge auf dem gleichen Band fertigen“, erläutert Oliver Zipse, Mitglied des Vorstands der BMW AG.
Aus betriebswirtschaftlicher Sicht lassen sich so Kosten bei rückläufigem Auslastungsgrad (Remanenzkosten) oder auch eine mangelnde Lieferfähigkeit, die Stand-alone-Produktionssysteme mit zu geringer Kapazität hervorrufen, vermeiden. Hinzu kommt, dass Automobile heute technisch hochkomplexe Produkte sind, die für ihre Fahrer zuverlässig funktionieren und einfach bedienbar sein müssen. Vor allem autonome Fahrsysteme benötigen viel Sensorik und Rechenleistung. Zur Veranschaulichung: Für ein komplett autonomes Fahren ist das 5.000-fache der Rechenleistung notwendig, die heute in einem BMW 5er verbaut ist. Und der heutige 5er beinhaltet bereits eine Reihe teilautonomer Fahrfunktionen. Selbstredend, dass alle autonomen Fahrsysteme fehlerfrei im Fahrzeug zusammenspielen müssen. Kleine „Hänger“ wie an privaten PCs sind hier nicht hinnehmbar.
Alles läuft in der Produktion zusammen
„Es ist wichtig, flexibel auf die Marktnachfrage reagieren zu können“, sagt Zipse. Nicht zu vergessen, das ansprechende Design, das für viele Kunden ein ausschlaggebender Kaufgrund ist. Darüber hinaus müssen die Hersteller eine Vielzahl gesetzlicher Anforderungen in den verschiedensten Absatzmärkten beachten. All diese Anforderungen laufen schließlich in der Produktion zusammen: Das Produkt muss produzierbar und lieferbar sein. Der beste Prototyp nützt nichts, wenn er nicht wirtschaftlich in Serie gebaut werden kann. Daher kann für BMW die Antwort nur Systemintegration lauten, die durch drei wesentliche Elemente geprägt wird: Die Integration aller Anforderungen an ein Auto, die Integration in einen 60 Sekunden Takt und die Integration neuer Produkte in bestehende Strukturen.
Herstellung im 60 Sekunden Takt
Wer ein komplexes Produktkonzept in Serie bringen will, braucht ein dazu geeignetes Produktionssystem. In der Automobilindustrie hat sich das Grundprinzip der Produktion in Taktabschnitten bewährt. Das bedeutet, vom Presswerk über den Karosseriebau, die Lackiererei und die Montage gibt es eine Vielzahl von Taktabschnitten. In einem Taktabschnitt stehen jeweils 60 Sekunden für Arbeitsinhalte zur Verfügung. So läuft am Ende alle 60 Sekunden ein Fahrzeug vom Band. Hierfür werden über 10.000 Teile zu einem fertigen Auto integriert. Eine bessere Variante als das Taktprinzip ist für BMW nicht in Sicht. Dies gilt auch in Zukunft für Hersteller, die mehr als 1.000 Autos pro Tag produzieren. „Entscheidend ist die Gestaltung des Abtaktungsprinzips am Montageband“, so Zipse. „Die Frage, die wir uns dabei stellen, lautet: Schaffen wir es, unterschiedliche Produktstrukturen in einem 60 Sekunden Takt am Band so darzustellen, dass unterschiedliche Fahrzeuge in einer beliebigen Reihenfolge gefertigt werden können ohne dabei Effizienznachteile zu haben.“
Architekturkonzept und Arbeitstakte
Für einen hohen technischen Verwandtschaftsgrad der Produkte muss vorab ein einheitliches Architekturkonzept mit den beiden Architekturen auf Basis Frontantrieb bzw. Hinterradantrieb etabliert werden. „Hier arbeiten wir als Produktioner eng mit dem Entwicklungsressort zusammen“, sagt Grüneisl. „So gelingt uns der Spagat zwischen Differenzierung, also einem vielfältigen Produktangebot an den Kunden, und einer effizienten Fertigung.“ Im Karosseriebau bedeutet dies teilweise unterschiedliche Fertigungsstrukturen für Vorderbau, Hinterbau und Unterboden. Ab dem Karosseriegerippe lässt sich der Durchlauf dann vereinheitlichen. In der Montage kommt es vor allem auf eine zielführende Integration bei den verschiedenen Antriebssträngen und der Sensorik für das hochautomatisierte und autonome Fahren an. Damit wird mit den verschiedenen Antriebssträngen das Zusammenfügen der Bodengruppe mit der Karosserie („Hochzeit“) vielfältiger und das Vorfügen („Verlobung“) von Antriebskomponenten einschließlich Energiespeicher und Leistungselektronik fordert bei Elektroautos zusätzliche Arbeitsschritte. Dafür werden nur die Arbeitstakte verändert, ohne die Fertigungszeit insgesamt zu verlängern. So bleiben die Prozesse stabil und effizient.
Alle Antriebsformen an einem Band
Zukünftig stehen also zwei flexible Fahrzeugarchitekturen bereit, wobei diese prinzipiell auch auf einen Allradantrieb ausgelegt sein können. Beide Architekturen werden dann mit allen Antriebsformen produziert: egal ob Verbrennungsmotor, Plug-in-Hybrid oder vollelektrischer Antrieb. Diese Architekturen erlauben es auch unterschiedliche Fahrzeugdesigns wie Limousinen oder SAV (Sport Activity Vehicle, z. B. BMW X5) zu realisieren. Die Frage ist nun, was aber muss im Werk passieren, damit alle Motorvarianten von einem Band laufen können? Weder im Presswerk noch in der Lackiererei ändert sich viel. Im Karosseriebau und in der Montage wird der Produktionsablauf angepasst. „Das vollelektrische Fahrzeug (BEV) unterscheidet sich vom Plug-in-Hybrid (PHEV) nur dadurch, dass wir die Bodengruppe in der Fahrzeugmitte variieren und dort den Flachspeicher unterbringen“, so Grüneisl. „Alle Komponenten vorne und hinten - Crash-Struktur, Stirnwand, Klimagerät – sind bei beiden gleich.“ In Unterscheidung zu Fahrzeugen mit Verbrennungsmotor sind BEV und PHEV in erster Linie bei Bodengruppe und Hinterbau spezifisch.
Produktion in der Haupt- und Nebenlinie
Im Grunde genommen werden die Zusammenbauten aus einzelnen Karosserieteilen bis hin zu Unterboden, Vorder- und Hinterbau in Zellen, noch vor dem Beginn einer eigentlichen Linie, gefertigt. Das geschieht unabhängig davon, ob sich diese Komponenten später in einem Fahrzeug mit Verbrennungsmotor, in einem Plug-in-Hybriden oder künftig in einem rein elektrisch angetriebenen Fahrzeug wiederfinden. Erst beim Fügen von Vorderbau, Unterboden und Hinterbau zur Bodengruppe beginnt eine Linie. Elemente wie Seitenrahmen oder Seitenwände sind Zulieferteile. Da ist es unerheblich, ob sie mit oder ohne Ladeklappe montiert werden.
Auf einen Blick: Logik der Automobilproduktion
In der Automobilindustrie umfasst die Systemintegration drei Elemente:
Integration in ein Produkt: Das ist weitgehend der Entwicklungsprozess: Wie muss ein Produkt gestaltet sein, dass es alle genannten Anforderungen gleichzeitig erfüllt?
Integration im 60 Sekunden Takt: In der Serienproduktion müssen bei jedem einzelnen Auto über 10.000 Einzelteile integriert werden. Können pro Werk 1.000 Autos am Tag produziert werden? Welche Potenziale bietet dabei die Digitalisierung?
Integration neuer Produkte in bestehende Strukturen: Es soll nicht nur ein Modell pro Werk produziert werden, sondern verschiedene Modelle. Ist das Produktionssystem in der Lage, ein neues Konzept zu integrieren? Diese Frage betrifft ganz aktuell die Themen Elektromobilität und Autonomes Fahren.