Vernetzung : Warum die moderne Produktion ohne Vernetzung nicht mehr auskommt
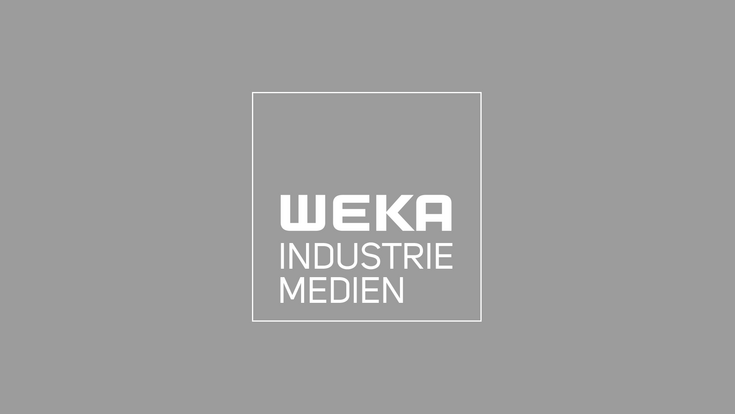
Ein Trend treibt die industrielle Fertigung in nahezu allen Branchen um: die möglichst effiziente und wirtschaftliche Fertigung auch kleinerer Losgrößen. Können Sie uns ein konkretes Beispiel nennen, Herr Bihler, das diesen Trend für die Metallbearbeitung verdeutlicht?
Mathias Bihler: Noch vor 10 Jahren war es üblich, dass Jahresaufträge vergeben wurden. So ein Jahresauftrag – zum Beispiel von einem Automobilhersteller – wurde dann am Stück produziert und mehrere Millionen Teile landeten beim Zulieferer im Lager. Dort war dann jede Menge Kapital gebunden, das keine Rendite bringt. Das ist alles andere als wirtschaftlich. Daher kamen Anforderungen auf, mit flexibleren Anlagen und kürzeren Rüstzeiten bedarfsorientiert zu fertigen.
Mit welchen Mitteln lassen sich die Rüstzeiten in der Metallbearbeitung reduzieren?
Bihler: Mit herkömmlichen Kurvenscheibenmaschinen nur bedingt. Denn das wirklich Aufwändige ist das Feinjustieren. Es dauert Stunden, wenn nicht Tage, um genau zu justieren, welcher Druck ausgeübt werden muss, um ein Stanzbiegeteil richtig auszuformen. Noch dazu ist die Justierung eine kniffelige Angelegenheit, dafür brauchen Sie bestausgebildete Fachkräfte. Ist eine Fachkraft gerade nicht verfügbar, können Sie die Maschine nicht in Betrieb nehmen. So lässt sich eine moderne Just-in-time-Produktion unmöglich umsetzen.
Welche Lösung schlagen Sie dann vor?
Bihler: Wir haben NC-Maschinen auf Basis der hochmodernen Steuerungs- und Servotechnik von B&R entwickelt. Mit diesen Bihler-NC-Maschinen legen Sie einmal die Kraft/Weg-Fahrprofile fest und speichern sie auf der Steuerung ab. Wird die Maschine umgerüstet, muss nur das entsprechende Programm abgerufen werden.
Können Sie uns ein Beispiel nennen, wie das funktioniert?
Bihler: Ein Kunde bekommt z. B. einen Auftrag über 50.000 Stanzbiegeteile für einen Automobilzulieferer. Sobald die Bestellung da ist, wird die Maschine umgerüstet, das dauert mit unserer NC-Technik gerade einmal 15 Minuten bis eine Stunde. Danach kann er sofort mit der Produktion beginnen. Ist der Auftrag fertig, wird wieder umgerüstet – möglicherweise für einen Auftrag aus dem medizinischen Bereich. Diese Flexibilität revolutioniert derzeit den Markt für die Stanzbiege- und Umformende Industrie. Ich gehe davon aus, dass der Markt für klassische Kurvenscheibenmaschinen in den kommenden Jahren rapide schrumpfen wird.
Herr Sandhöfner, welche Lösungen stellt B&R als Automatisierer bereit, damit solche Maschinenkonzepte umgesetzt werden können?
Markus Sandhöfner: Solche Maschinen lassen sich nicht aufgrund einzelner Hard- oder Softwareprodukte entwickeln. Dazu ist ein durchgängiges Gesamtsystem notwendig, wie es wenige Anbieter im Portfolio haben. So ist bei B&R Hard- und Software vollständig unabhängig voneinander. Einmal geschriebene Software ist aufgrund der vollständigen Durchgängigkeit mit jeder Hardware-Generation und Performance-Klasse verwendbar. Sehr wichtig sind auch offene Schnittstellen, damit Maschinen- und Anlagenbauer alle benötigten Komponenten über ein System steuern können.
Bihler: Genau das ist für uns ein entscheidender Punkt: B&R bietet die Möglichkeit, mit einer Mastersteuerung alle Funktionen zu steuern, die wir zur Automatisierung und Prozessentwicklung benötigen. Wenn mehrere Steuerungen für unterschiedliche Verfahrenstechnologien in einem durchgängigen Prozess nötig sind, wird der Aufwand für Wartung und Handhabung zu groß und irgendwann stößt auch die Performance an ihre Grenzen.
Apropos Performance: Können Servo-Applikationen in diesem Punkt mit einer guten Kurvenscheibenmaschine mithalten?
Sandhöfner: Moderne Servotechnik ist Kurvenscheiben weit überlegen. Sehen wir uns die neue Bihler-Maschinengeneration an: An einer Anlage werden zum Beispiel 89 Achsen mit unserem Echtzeitnetzwerk POWERLINK synchronisiert. Die Zykluszeit liegt bei 400 bis 800 Mikrosekunden. Damit lässt sich eine unglaubliche Präzision erreichen.
Bihler: Das kann ich nur bestätigen. Um die Leistung unserer Maschinen zu erhöhen, führen wir die Geschwindigkeit der einzelnen Prozesse bis an die Grenzen des physikalisch Machbaren. Wir können Band- oder Drahtmaterial problemlos so schnell biegen, dass das plastische Umformvermögen gerade nicht überschritten wird.
Wie funktioniert das?
Bihler: Früher haben wir zahlreiche Kurven berechnet, hergestellt, ausprobiert, analysiert und neu berechnet, um die Grenzen des Machbaren auszuloten. Mit Servotechnik kann ich in Minutenschnelle die Fahrprofile exakt an das Umformvermögen des Materials anpassen. Doch das ist nicht alles. Während eines Biegevorgangs wird gemessen, ob es – zum Beispiel aufgrund von Materialschwankungen – zu Abweichungen vom vorhergesehenen Biegewinkel kommt. Die B&R-Servotechnik zusammen mit der Bihler-Messtechnik regelt so schnell, dass der Biegevorgang in Echtzeit angepasst werden kann. So können unsere Kunden perfekte Qualität bei extrem hoher Performance produzieren.
Solch anspruchsvolle Regelungen erfordern sicherlich hochspezialisierte Experten für die Software-Entwicklung.
Bihler: Das ist richtig. In unserem Unternehmen gibt es extrem viel Know-how, was die Umsetzung von Stanz-, Biege- und Montageprozessen in Software angeht. Das macht viel vom Erfolg unserer NC-Maschinen aus. Gleichzeitig muss ich aber betonen: Was die Ansteuerung von Achsen, die Regelungstechnik an sich und vieles mehr betrifft, benötigen wir keine Experten. Für diese Themen haben wir mit B&R einen Partner an unserer Seite, der genau die Plattform bietet, auf der wir unser Prozess-Wissen perfekt umsetzen können.
Wie sieht diese Plattform aus?
Bihler: Dazu gehören viele Komponenten, zum Beispiel die komplette Hardware, aber natürlich auch die Automatisierungs-Software Automation Studio. In Zukunft werden wir sogar noch mehr auf das Know-how von B&R setzen. Zum Beispiel implementieren wir gerade eine OPC-UA-Schnittstelle in unsere Maschinen. Da alle B&R-Steuerungen als OPC-UA-Client und -Server fungieren können, ist der Aufwand für uns erstaunlich gering. Auch wenn wir demnächst Robotik in unsere Maschinen einbinden, bietet uns B&R viele Vorteile: Es ist keine eigenständige Roboter-Steuerung notwendig und mit mapp können wir die Roboter einfach engineeren.
Herr Sandhöfner, was können wir uns unter mapp vorstellen?
Sandhöfner: Bei mapp Technology kapseln wir komplette mechatronische Systeme in Software-Komponenten, die unsere Kunden nur noch parametrieren müssen. So können Kunden wie Bihler komplexe Kinematiken ansteuern, ohne dass sie die Software für die Bewegungssteuerung selbst schreiben müssen.
Herr Bihler, Sie haben vorher OPC UA angesprochen. Werden Sie in Zukunft verstärkt auf die Vernetzung Ihrer Maschinen setzen?
Bihler: Definitiv. Die moderne Produktion kommt ohne Vernetzung nicht aus, darauf basieren ja auch Konzepte wie Industrie 4.0. Um genau zu sein, sind wir auf diesem Gebiet schon sehr weit. Schon heute senden Bihler-Maschinen aus der ganzen Welt Analysedaten zu unserem Stammsitz, wo sie ausgewertet werden. Das geht so weit, dass wir Kunden anrufen, um ihnen zu sagen, dass in Maschine xy das Achslager Nr. 25 Verschleißerscheinungen hat und demnächst ausgetauscht werden muss, um einen ungeplanten Stillstand zu vermeiden.
Wie können Sie die Fehlerquelle so genau bestimmen?
Bihler: Jede Achse hat einen charakteristischen Fingerabdruck. Den messen und speichern wir, bevor wir die Maschine ausliefern. Gibt es dann eine Abweichung von diesem Fingerabdruck wissen wir sofort, dass sich ein Parameter geändert hat. Das ist eine eklatante Weiterentwicklung: War früher eine Bihler-Maschine kaputt, musste unser Service-Techniker hinfahren und sich auf die Suche machen, wo der Fehler in einer Maschine mit 40 Achsen liegt. Wenn er das defekte Teil gefunden hatte, musste er es selbst holen oder von einem Kurierdienst liefern lassen. Ich bin mir sicher: Unternehmen, die sich keine Gedanken darüber machen, wie sie Daten ihrer Maschinen sammeln und auswerten, werden es immer schwerer haben, im Wettbewerb zu bestehen.