Produktion : „Völlig neue Maschinenkonzepte“
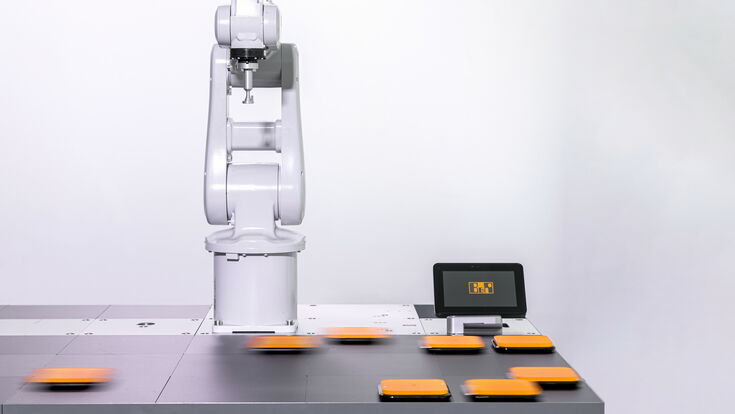
Dario Rovelli will nicht optimieren. Er will etwas Neues schaffen. „Die Optimierung des Produkttransports ist schon lange ein Thema“, sagt der Head of Product Management Motion and Mechatronic Systems bei B&R, „aber eben nur die Optimierung.“ Seit Beginn der industriellen Produktion werden die Produkte von einer Prozessstation bearbeitet, dann zur nächsten Station transportiert und dort wieder bearbeitet. Und das wird so oft wiederholt, bis das Produkt fertig ist. Der Produkttransport ist somit eine Art notwendigen Übels, das selbst keinen Beitrag zum eigentlichen Fertigungsprozess leistet. Außer ein paar Visionären habe niemand dieses Konzept hinterfragt, sagt Rovelli.
Das soll sich nun ändern, und zwar dank Einführung der Magnetschwebetechnik in die Industrie. Was B&R unter dem Namen ACOPOS 6D zum Jahresbeginn vorgestellt hat, soll die Idee des linearen Transports von Station zu Station obsolet machen. „Wir werden in den kommenden Jahren völlig neue Maschinenkonzepte sehen, die weitaus flexibler und produktiver sein werden als aktuelle Generationen“, prophezeit Dario Rovelli, „die Freiheiten, die ACOPOS 6D Maschinenbauern und -betreibern gibt, werden die Produktionsprozesse grundlegend verändern.“
Berührungslos, platzsparend und reibungsfrei
ACOPOS 6D basiert auf dem Prinzip der Magnetschwebetechnik: Shuttles mit integrierten Permanentmagneten bewegen sich berührungslos auf einer Fläche aus Motorsegmenten. Die elektromagnetischen Motorsegmente sind 240 x 240 mm groß und können zu beliebigen Formen zusammengesetzt werden. Die Shuttles tragen je nach Größe 0,6 bis 14 kg Gewicht und bewegen sich mit einer Geschwindigkeit von bis zu 2 m/s. Sie können sowohl zweidimensional verfahren als auch ihre Schwebehöhe ändern und sie lassen sich entlang von drei Achsen drehen oder neigen. Das System verfügt also – namensgebend – über sechs Freiheitsgrade.
Als einen zentralen Vorteil des Systems nennt Rovelli den verminderten Platzbedarf: ACOPOS 6D ermöglicht eine bis zu vier Mal so hohe Shuttle-Dichte wie andere Systeme auf dem Markt, da auf einem Motorsegment gleichzeitig mehrere Shuttles fahren können. Zudem lassen sich die Shuttles als Achsen bei Bearbeitungsstationen einsetzen.
So kann ein Shuttle etwa mit einem Werkstück CNC-Pfade abfahren, während das Bearbeitungswerkzeug starr angebracht ist. Wiegestationen entfallen sogar vollständig, da jedes Shuttle gleichzeitig eine hochpräzise Waage ist. Dadurch kann die Maschine kleiner gebaut werden.
Da die Shuttles frei schweben, verursacht ACOPOS 6D zudem keine Reibung. Somit entsteht auch kein Abrieb, und es gibt keine Verschleißteile, die gewartet werden müssen. Werden die Motorsegmente mit einer Edelstahlabdeckung versehen, entspricht ACOPOS 6D der Schutzart IP69K – das System eignet sich somit für einen Einsatz in Reinräumen und in der Nahrungsmittelproduktion.
Vollständig integriert und mit Intelligenz ausgestattet
ACOPOS 6D ist vollständig in das B&R-System integriert. Daher lassen sich die Shuttles mit beliebigen Achsen, Robotern, Track-Systemen oder Vision-Kameras mikrosekundengenau synchronisieren. Die Bahnplanung der Shuttles selbst erfolgt in einem dedizierten Controller, der mit POWERLINK in das Maschinennetzwerk eingebunden wird. Die Bahnplanung beeinträchtigt daher die Performance des Netzwerkes und der Maschinensteuerung nicht. Für Systeme mit mehr als 200 Segmenten oder 50 Shuttles lassen sich mehrere Controller einsetzen und miteinander synchronisieren.
Im Gegensatz zu vergleichbaren Systemen ist beim ACOPOS 6D jedes Shuttle mit einer weltweit einmaligen ID ausgestattet. Der Controller weiß beim Hochfahren daher sofort, wo genau auf den Motorsegmenten sich welches Shuttle befindet. Aufwändige Homing-Sequenzen oder manuelle Eingaben nach dem Hochfahren sind nicht notwendig.
Die Produktion kann sofort beginnen. Die Positionswiederholgenauigkeit der Shuttles liegt bei ±5 µm, daher ist ACOPOS 6D auch uneingeschränkt für Applikationen geeignet, bei denen es auf höchste Präzision ankommt, zum Beispiel in der Elektronikindustrie und bei der Assemblierung mechanischer und elektronischer Komponenten.
Das Ende der strengen Taktung
Wie die Technologie Produktionsprozesse grundlegend verändern kann, erklärt Rovelli am Beispiel der Parallelisierung langsamer Prozesse: „Die herkömmliche industrielle Produktion ist streng getaktet. Erst wenn alle Bearbeitungsstationen fertig sind, werden alle Produkte eine Station weiter transportiert. Das hat zur Folge, dass die langsamste Bearbeitungsstation den Produktionstakt – und damit die Produktivität – bestimmt.“
Mit einem System wie ACOPOS 6D muss dieser strikte Takt nicht eingehalten werden. Gibt es zum Beispiel eine Bearbeitungsstation, deren Durchlaufzeit doppelt so hoch ist wie die der anderen, wird diese Station zweimal eingesetzt. Die parallelen Stationen werden dann abwechselnd von den Shuttles angefahren. „Um den Output zu verdoppeln muss also nicht die vollständige Maschine oder Linie doppelt angeschafft werden, es reicht aus, diejenige Prozessstation zu verdoppeln, die die gesamte Maschine ausbremst.“
Die Vision des mehrdimensionalen Produktionsraums
Der Traum mancher Vordenker, sagt Rovelli, sei das völlige Auflösen des linearen Produkttransports zugunsten eines mehrdimensionalen Produktionsraums: Jedes Produkt bewegt sich individuell von Bearbeitungsstation zu Bearbeitungsstation, ohne an einen rigiden, sequenziellen Produktionstakt gebunden zu sein. ACOPOS 6D schaffe alle Voraussetzungen, um die Vision des mehrdimensionalen Produktionsraums in die Realität umzusetzen.
Wo das System an seine Grenzen stößt, können andere verfügbare Technologien eingesetzt werden: „Ist es zum Beispiel notwendig, schwere Produkte schnell und mit sehr geringem Produktabstand zu transportieren, kann ACOPOS 6D einfach mit Track-Systemen wie ACOPOStrack oder SuperTrak kombiniert werden. Generell ist ACOPOS 6D eine Technologie, die nicht völlig für sich allein gesehen werden darf“, betont er. „Erst durch die Kombination mit anderen intelligenten Technologien wie Robotik, Machine Vision, Simulation und intelligenter Software spielt ACOPOS 6D sein volles Potenzial aus.“
Geburtsstunde der Schwarmproduktion
Und damit könnte Realität werden, was fast schon zur Platitude verkommen ist: Die Idee, dass sich das Produkt den Weg durch die Produktion selbst suchen soll, gilt schon lange als eine der wesentlichen Visionen von Industrie 4.0 und Industrial IoT. „Das wurde häufig als Hirngespinst abgetan, „aber nun haben wir tatsächlich die Technologie, diese Vision in die Tat umzusetzen“, sagt Dario Rovelli. Mit ACOPOS 6D kann eine Maschine gleichzeitig unterschiedliche Produktvarianten oder sogar unterschiedliche Produkte fertigen. Jedes Produkt fährt die Stationen an, die es tatsächlich benötigt. Und das, sagt Rovelli, sei nicht weniger als die Geburtsstunde der Schwarmproduktion.
Ist ein elaboriertes IoT-Umfeld also Voraussetzung? Nicht unbedingt, meint Rovelli, ACOPOS 6D funktioniere grundsätzlich auch isoliert in einer unvernetzten Umgebung, „aber natürlich schöpft ACOPOS 6D sein volles Potenzial erst im IoT-Kontext aus. Individualisierte Produkte, die der Kunde online konfiguriert und die dann ohne Zwischenstation direkt in die Maschinenhalle übermittelt werden, sind dann nicht mehr Zukunftsmusik, sondern Realität.“
Dabei spiele eine wichtige Rolle, dass IT und OT nahtlos miteinander verknüpft sind. Und zugleich heiße das auch, dass der Anteil der Software am Produktionsprozess immer wichtiger wird. „Wer sich dieser Tatsache nicht bewusst wird und es verschläft, sein Angebot dementsprechend weiterentwickelt, wird es in Zukunft immer schwerer haben, wirtschaftlich zu produzieren.“