Additive Fertigung : Stefanie Brickwede: "Die Serienreife des 3D-Drucks steht außer Frage.“
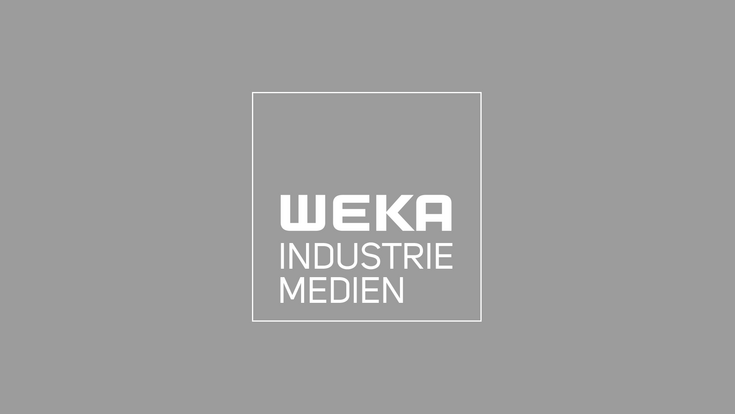
Frau Brickwede, stimmt es, dass sich die Deutsche Bahn die Thematik 3D-Druck aus dem Silicon Valley abgeschaut hat?
Stefanie Brickwede: Ich würde nicht sagen „abgeschaut“, aber die Vorstände der Deutschen Bahn haben sich dort vor ein paar Jahren sicher jene Inspiration geholt, die uns heute tolle neue Möglichkeiten beschert. Ich würde aber behaupten, dass unsere Einsatzgebiete sich doch unterscheiden.
Interessant ist, dass bei Ihnen Prototyping keine Rolle spielt …
Brickwede: …was daran liegt, dass wir keine Hersteller sind. Bei uns war schon immer das Thema Ersatzteile am attraktivsten.
Sie kämpfen mit obsoleten Bauteilen. Man möchte meinen, dass die Deutsche Bahn doch riesige Ersatzteillager beherbergt?
Brickwede: Ja wir haben riesige Lager. Für unseren „Rolling Stock“, also nur die Fahrzeuge, haben wir Teile im Wert von 600 Millionen Euro auf Lager. Dennoch kämpfen wir mit Obsoleszenz. An bestimmte Teile kommen wir gar nicht mehr ran, weil es diese einfach nicht mehr gibt.
Liegt das an den Liefergarantien für die Zugbranche?
Brickwede: Richtig. Im Normalfall haben wir Liefergarantien für die ersten 15 Jahre. Aber allein die erste ICE-Generation fährt schon mehr als 25 Jahre. Sie sehen also, dass wir durchaus mit der Beschaffung von bestimmten Ersatzteilen zu kämpfen haben. Ein anderes Thema sind die langen Lieferzeiten. Für Gussteile warten wir momentan bis zu neun Monate. Ein Zug der neun Monate steht, rechnen Sie sich das mal hoch.
Das angesprochene Gussteil wurde aber kürzlich von Ihnen gedruckt …
Brickwede: … und damit hatten wir das Teil innerhalb von drei Wochen verfügbar.
Drei Wochen statt neun Monate ist gewaltig. Erlauben Sie mir die Bemerkung, aber ich finde drei Wochen für einen Druck etwas lang.
Brickwede: Oh der Druck war viel schneller, aber das Reengineering und die Zertifizierung dieses sicherheitsrelevanten Teiles ist sehr aufwändig.
Das heißt es gibt keine Standards beim Drucken?
Brickwede: Noch nicht. Im Moment ist jedes Teil eine Einzelfertigung. Aber gemeinsam mit dem TÜV Süd haben wir intensiv eine Herstellerqualifizierung für Druckdienstleister erarbeitet. Das soll nicht nur bahnbezogen sein, sondern auch z.B. Automotivkonzernen helfen.
Wie viele Teile drucken Sie im Moment?
Brickwede: Derzeit werden über 110 unterschiedliche Teile gedruckt, darunter auch sicherheitskritische Teile. Zwei Drittel davon werden schon verbaut und erfüllen alle Voraussetzungen.
Die Deutsche Bahn selber besitzt keine Drucker? Richtig?
Brickwede: Richtig. Wir nutzen Dienstleister.
Sie bauen gerade ein internationales Netzwerk „Mobility goes Additive“ auf, um der Technologie im Mobilitätssektor zum Durchbruch zu verhelfen. Innerhalb von zwei Jahren sind sie von neun auf 90 Mitglieder gewachsen. Auch international?
Brickwede: Ja sehr international sowohl auf Mitglieder- als auch auf Interessentenseite. Vor kurzem war z.B. eine Delegation der amerikanischen Armee bei uns. Die haben die gleichen Probleme wie wir: Große Fahrzeuge, obsolete Teile, keine Ersatzteile auf Lager. Es ist sehr spannend, welche branchenübergreifende Parallelitäten da plötzlich entstehen. Auch Kuba interessiert sich sehr für das Thema 3D-Druck. Das Land will unabhängiger gegenüber Einfuhrverboten werden.
Man kann also sagen, dieses Netzwerk ist absolut am Puls der Zeit. Aber was sind denn immer noch die großen Hemmnisse des 3D-Drucks?
Brickwede: Davon gibt es aktuell noch mehrere. Nüchtern betrachtet, hätten wir da einmal die Materialkosten. Gerade im Metallbereich kann 3D-Druck um das zehnfache teurer sein als alternative Technologien. Ein zweites Hemmnis sind die vorhin erwähnten Standards. Diese braucht es dringend, um in größeren Mengen produzieren zu können.
Diese Standards sollten aber dann international sein?
Brickwede: Völlig richtig. Europa hat hier die einmalige Chance eine Vorreiterrolle zu übernehmen und diese Standards weltweit zu etablieren.
Weil alle großen Drucker- und Materialhersteller in Europa sitzen?
Brickwede: Ja, aber die Krux ist, dass diese Verhandlungen unglaublich zäh sind. Die Amerikaner ziehen mittlerweile gewaltig nach. Und die Chinesen liegen auch nur mehr ein Jahr hinter uns. Unsere Vorreiterposition zu verlieren, betrachte ich mit Sorge.
Ist die Mitarbeiterqualifizierung ein Hemmnis?
Brickwede: Oh ja ein großes sogar. Es gibt nicht genug Leute, die 3D-Drucker, also die Maschinen, beherrschen.
Aber werben nicht gerade die Hersteller mit einfachster Bedingung?
Brickwede: Leider ist das ganze Prozedere kein „Plug & Print“. Gerade beim Maschinenhandling braucht es neue Ausbildungsmodelle. Derzeit bedienen Maschinenbauingenieure die Drucker. Es bräuchte aber einen Ausbildungslehrgang „Additiver Maschinentechniker“, denn es geht auch darum mit teils gesundheitsgefährdenden Materialien richtig umzugehen. Auch das Entfernen der Stützstrukturen nach dem Druck ist eine Herausforderung, da immer noch vorwiegend händisch.
Das kürzlich mir zugetragene Argument eines Maschinenbauers gegen diese Technologie dürfte Ihnen bekannt sein: „Das ist nur eine Spielerei und nicht serientauglich.“
Brickwede: Dieses Argument kenne ich nur zu gut. Allerdings sollte sich gerade der Mittelstand Gedanken machen, ob er in der Ecke sitzen bleibt und wartet oder das Thema mitforcieren möchte. Druckmaschinen- und Materialhersteller müssen die Anforderungen ihrer Anwender kennen, um entsprechende Produkte zu entwickeln. Keiner von denen macht F&E vom grünen Tisch weg. Ich gebe Ihnen ein Beispiel: Bei der Bahn brauchen wir für bestimmte Bauteile flammfeste Materialien. Diese gibt es bereits für den Aviation-Bereich. Sie eigenen sich aber nicht für den Zug, weil dieser unter Umständen bei einem Feuer viel länger steht als z.B. ein Flugzeug. Dennoch dürfen diese Materialien nur bedingt Rauch entwickeln oder schmelzen. Den konkreten Branchenbedarf muss man den Hersteller aber zuerst erklären.
Sie erwähnten den Mittelstand? Hinkt der hinterher?
Brickwede: Die großen Konzerne auf der Herstellerseite, wie Siemens, Bombardier haben den Wert dieser Technologie verstanden. Was mir Bauchschmerzen bereitet sind die Zulieferer dieser Konzerne. Aus unterschiedlichsten Gründen will der Mittelstand nicht auf diesen Zug aufspringen.
Einen Grund kann ich Ihnen nennen: So ein Drucker bedeutet im Schnitt eine Investition von über eine Million Euro.
Brickwede: Das ist richtig, hinzu kommen Know-how-Gründe und Personalengpässe.
Und dennoch raten Sie dem Mittelstand, einfach mal drauf los zu drucken?
Brickwede: Ja, denn trotz guter Auftragslage werden sie sonst den Anschluss verlieren. 3D-Druck bedeutet eine Disruption, die für gewisse Sparten nicht gut ausgeht.
Geben Sie uns bitte ein Beispiel.
Brickwede: Ein gutes Beispiel sind orthopädische, medizinische bzw. Dentalprodukte. Das sind alles individualisierte Produkte. Wer hier nicht auf 3D-Druck setzt, wird den Bach runter gehen.
Ein ziemlich düsteres Bild. Auf welche Fakten stützen Sie diese Aussage?
Brickwede: In den USA wurde innerhalb von 500 Tagen die Herstellung von Hörgeräten komplett auf 3D-Druck umgestellt. Adidas druckt mittlerweile individualisierte Sohlen. Orthopädische Einlagen werden künftig direkt eingedruckt, sind aber bislang die Cashcow von Orthopädietechnikern.
Was sagen Sie zu folgendem Geschäftsmodell: Ein Mittelständler kauft sich einen 3D-Drucker und lässt andere Unternehmen daran teilhaben? Teilt also seine Druckkapazitäten?
Brickwede: Interimistisch ist das sicherlich eine gute Idee und entwickelt die Geschäftsmodelle der Druckdienstleister weiter. Immer mehr Softwareanbieter konzentrieren sich auf die Durchsteuerung von verschiedenen Produkten. Die Vernetzung mit fremden Branchen macht definitiv Sinn.
Sie druckten bereits über 6.000 Teile. Wie haben Sie diese Teile identifiziert? Gibt es da eine Grundregel?
Brickwede: Zu anfangs haben wir versucht diese Teile über unser SAP-System zu identifizieren. Dies war allerdings eine Sackgasse, weil wir nicht immer wussten, welches Material verwendet wurde, weil wir keine Fotos vom Verbauort hatten usw. „Top-Down“ ging also nicht, deswegen versuchten wir es „Bottom-Up“. Wir sind in die Werkstätten gegangen und haben uns „Entflammte“ gesucht, die Teile für uns identifiziert haben.
Entflammte?
Brickwede: (lacht) Mitarbeiter, die Feuer und Flamme für das Thema sind. Jeder Betrieb hat sie, man muss sie nur finden. Dafür gilt es mit den Leuten zu reden. So kam z.B. mal ein Kollege aus dem Bereich Bahnhöfe zu uns. Anfangs recht schüchtern, weil er nicht wusste, ob seine Idee überhaupt Sinn machen würde. Es ging dabei um Handlaufschilder in Blindenschrift. Diese sind hochindividuell und wurden bislang teuer gefräst. Deshalb gab es diese nur in großen Bahnhöfen. Ein perfekter Fall für 3D-Druck. Heute drucken wir diese Schilder mit Titan, haben die Kosten um die Hälfte reduziert und konnten damit den Raum Aachen mit 1.500 Schildern ausstatten.
Wer von 3D-Druck spricht, spricht oft von einem gewaltigen Potenzial für bionisch optimierte Bauformen. Sie drucken allerdings nur „fade“ Ersatzteile.
Brickwede: Mit dieser Kritik wurde ich zu anfangs auch konfrontiert. Additive Fertigung macht nur Sinn, wenn man bionisch optimiert. Das ist Blödsinn. Ich kann damit auch völlig banal Ersatzteile klonen. Vielleicht bringt das nicht das volle Potenzial zu Tage, aber wenn ich mir damit die Wartezeit von neun Monaten spare, steht der Nutzen wohl außer Frage.
Sie sind Ökonomin, arbeiten aber mit Ingenieuren. Vor zwei Jahren vs. heute: Welche Differenzen haben Sie beseitigt?
Brickwede: Vor zwei Jahren wurde ich für meine Idee, geschmiedete Teile drucken zu wollen von Ingenieuren „abgewatscht“. Heute robben wir uns gemeinsam an das Thema heran. Die Start-up-Logik, das Bastelimage des 3D-Drucks ist verschwunden. Dass die gedruckte Massenfertigung kommt, wird heute nicht mehr in Frage gestellt. Viele Ingenieure mögen die additive Fertigung für eine Evolution halten, für mich ist es definitiv eine Revolution.
Vielen Dank für das Gespräch! Das Gespräch führte Elisabeth Biedermann