Standort-Ausbau : Sauerstoffreduziertes Hochregallager
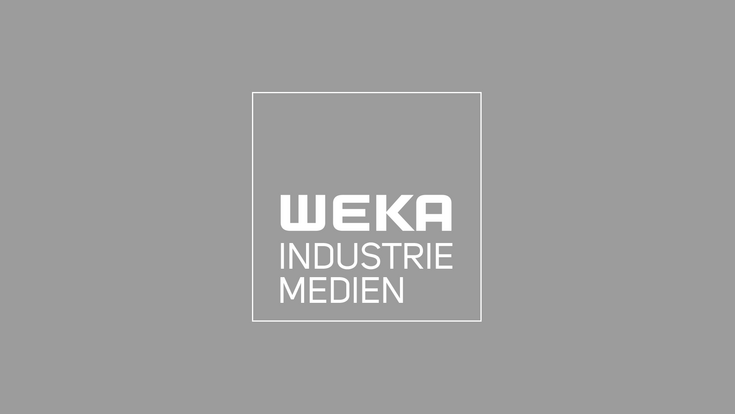
Es wurde eng am Standort Asten für die Lenze Österreich Gruppe. Die Kapazitätsgrenzen waren nahezu ausgereizt, der Betrieb platzte aus allen Nähten. Grund genug, eine wichtige Entscheidung zu treffen – den Standort nicht nur auszubauen, sondern auch für die Zukunft wettbewerbsfähig zu halten. Mit einer Investition von 14 Mio. Euro erweiterte das Unternehmen die Niederlassung daher nicht nur, sondern stellte gleichzeitig einige Weichen für die Zukunft. So wurde etwa die Lackierbox zu einer modernen Lackieranlage mit zwei Spritzständen - an denen bis zu fünf Standardfarben auf Knopfdruck und ohne manuelle Abmisch-Tätigkeit zur Verfügung stehen - ausgebaut.
Lasten bis zu zwei Tonnen. „Früher bildete die Farbgebung ein Ausstoß-schmälerndes Nadelöhr in der Astener Getriebemotorenfertigung, nun wird hier dank einer aktiven Kühlstrecke im Zwei-Minuten-Takt abgefertigt. Die aktuelle Kapazitätsgrenze liegt bei circa 120.000 Ein- heiten“, erklärt Lenze Operations Austria-Geschäftsführer Marco Gattringer-Ebner. Zudem sei auch das maximal handhabbare Produktgewicht in der Lackieranlage erhöht worden. Statt wie früher nur 800 kg packen die einzelnen Traversen der Power&Free-Förderanlage nun Lasten von bis zu 2.000 kg. Dies bedeute, dass zahlreiche Produkte, „die bisher für ihren applikationsspezifischen Feinschliff nach Deutschland oder Frankreich mussten“, nun in Asten endmontiert werden könnten. Etwa 11er und 14er-Getriebe mit einem Abtriebsdrehmoment von bis zu 12.000 Nm sowie Regler der Baureihen 8400 und 9400. Klarer und strukturierter Ablauf. Zudem werde der Standort Asten als Vorratswerk für Drehstrommotore gestärkt, betont Gattringer-Ebner. Für Kunden bedeute der Umbau bessere Verfügbarkeiten, höhere Flexibilität und kürzere Durchlaufzeiten, für Lenze selbst eine Reduktion beziehungsweise Auflösung der angemieteten, externen Lager, eine Kapazitätserhöhung und eine Verbesserung des Materialflusses in der Produktion. „Wir haben jetzt viel mehr Fläche – zur bestehenden 4.800 m2 großen Halle kamen das Hochregallager mit 1.650 m2 und die neue Halle mit 3.000 m2 hinzu – trotzdem wurde der Materialverkehr in der Halle vereinfacht. Wir haben jetzt einen sehr klaren und strukturierten Ablauf vom Eingangsstrom bis zur Auslieferung“, so der Lenze Operations Austria-Boss. Das zugrunde liegende Logistikkonzept wurde – inklusive Ausschreibung und Werkstrukturplanung – in Zusammenarbeit mit Protema Unternehmensberatung erstellt und gemeinsam mit dem Förder- und Lagertechnikspezialisten TGW umgesetzt.
Sehen Sie zum Standort-Ausbau von Lenze eine Fotostrecke.
Zum Einsatz kamen dabei ein automatisches Kleinteilelager (AKL), ein automatisches Palettenlager (APL), mehrere Kommissionierarbeitsplätze mit Pick&Pack, Regalbediengeräte, die Zuführung von vorkommissionierten Behältern aus dem AKL zur Palettenkommissionierung, die fördertechnischen Anbindungen an das Werkstättenlager und an die Lackieranlage, die Lagerverwaltungssoftware CILOG, den Materialflussrechner sowie die Visualisierung, wie . Die gesamte Antriebstechnik für die Regalbediengeräte wurde mit Ein- und Rückspeisemodulen sowie Servoreglern und -antrieben von Lenze realisiert. Ebenso aus dem eigenen Hause stammen die Einspeisemodule für die Behälter- sowie Paletten-Verfahrwagen, sämtliche Antriebe für die Behälter- und Palettenfördertechnik, die Riemen für Querverfahrwägen und Regalbediengeräte, sämtliche Antriebselemente sowie der Schaltschrankbau. Bis zu 260 Ein-/Auslagerungen pro Stunde. Das Hochregallager selbst ist 20 Meter hoch und wurde laut Markus Lehner, Sales Manager bei TGW Systems Integration, in Silobauweise errichtet. Die Gebäude-Außenhülle des Gebäudes wird durch den Stahlbau des Hochregallagers getragen. Im AKL finden bis zu 18.000 Behälter bei 260 Ein-/Auslagerungen pro Stunde Platz. Das dreigassige APL kann bis zu 9.244 Paletten aufnehmen, bei bis zu 95 Ein-/Auslagerungen pro Stunde. In Sachen Brandschutz geht Lenze neue Wege: „Die Brandprävention im gesamten Lager erfolgt durch eine Sauerstoffreduktion auf 15 Prozent“, betont Gattringer-Ebner. Ebenfalls umgestellt wurden Kommissionierung und Verpacken. Beides werde nun an einer Station und von derselben Person durchgeführt. „Der Mitarbeiter steht beim Computer, fordert einen Transportauftrag zu einer bestimmten Lieferung an und die automatische Fördertechnik beziehungsweise die Regalbediengeräte bringen dann die richtigen Paletten und Behälter zur Arbeitsstation. Der Mitarbeiter nimmt die Teile raus, scannt diese und macht den Auftrag versandfertig“, wie Gattringer-Ebner erläutert. Diese Vereinfachung der Arbeitsprozesse finde besonders bei den Mitarbeitern großen Anklang.
Sehen Sie zum Standort-Ausbau von Lenze eine Fotostrecke.