Anger Machining & LCM : Neues Mercedes Getriebe made in Austria
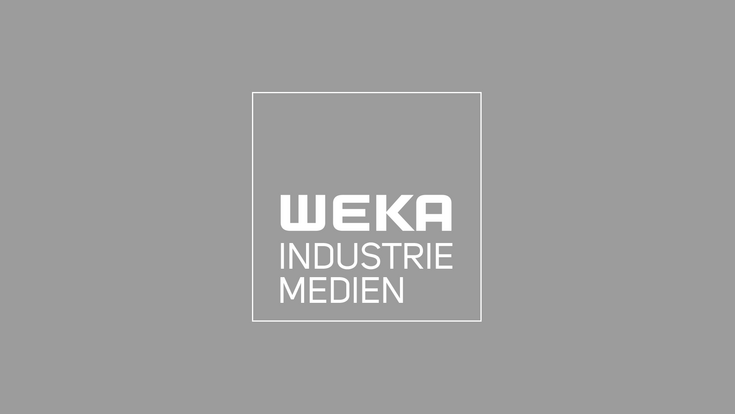
Es war eine der meist bestaunten Überraschungen auf der Automobilmesse in Frankfurt: Das von Mercedes-Benz entwickelte 9G TRONIC-Getriebe – das weltweit erste 9-Gang Automatik-Getriebe für Premiumfahrzeuge. Für die Bearbeitung des dazugehörigen Ventilblocks, der nunmehr neun statt bisher sieben Gänge zu schalten hat, holte sich die Traditionsmarke Unterstützung aus Österreich. Der Unterschied zum Mitbewerb.
Der Wettbewerb war hart. Aber am Ende ging der Prestigeauftrag von Mercedes-Benz nach Traun. Anger Machining konnte sich mit einem überlegenen Konzept gegen renommierte Maschinenbauer durchsetzen. „Präzision und Geschwindigkeit auf engstem Raum in den Gesamtprozess integrieren“, so fasst Roland Haas die Vorgaben der Daimler AG zusammen. Der Bereichsleiter Technik bei Anger Machining hat eine Anlage mit 3-fach-Bearbeitung konstruiert. Der ausschlaggebende Unterschied zum Mitbewerb: Geringerer Platzbedarf und höherer Output als Doppel-Bearbeitungsmaschinen. Um die außerordentlich strengen Toleranzvorgaben erfüllen zu können, holte sich Anger das Linz Center of Mechatronics (LCM) mit an Bord. LCM wurde damit beauftragt, ein hydraulisches Mikro-Positionierungssystem zur Korrektur der Spindelpositionen zu entwickeln. Das bisherige Problem: Durch verschiedene Effekte konnte es bisher sowohl bei den Spindelpositionen als auch bei den Werkstücken zu Lagefehlern kommen. „Bei der Parallelbearbeitung dreier Werkstücke sind die Werkstücke aber nur gemeinsam am Hauptantrieb korrigierbar“, erklärt Haas. Das hydraulische Mikro-Positionierungssystem von LCM sorgt nun dafür, zwei der drei Werkstücke entgegen auftretende Positionsabweichungen elektronisch unabhängig von ihrer Position zu korrigieren. Es kann Positionskorrekturen der Spindeln in den zwei Achsen normal zur Spindelachse bis zu sieben Mal pro Sekunde mit einer Präzision von weniger als 5 µm ausgleichen. „Das System von LCM ist nicht nur robust, schnell und präzise, es braucht auch kaum Platz“, so Haas über die Entwicklungsarbeit des Mechatronik-Spezialisten. Die größte Herausforderung dabei: Die Hydraulik mit der Mess- und Regelungstechnik zu einer funktionierenden Einheit zusammenzuführen und das auf engstem Raum. Verkabelung und die Sensorik inklusive. Elastische Stahlmembranen halten 3 Tonnen Druck.
Herzstück dieser neuartigen Mikro-Positionierung der Spindelköpfe sind jeweils vier hydraulisch verstellbare, in Paaren gegeneinander wirkende Stahlmembranen. Sie erlauben als Druckkissen Positionskorrekturen in beiden Spindelnormalachsen. Durch Veränderung des Öldrucks in den Membranen und eine spezielle Rahmenkonstruktion ist so eine zweiachsige Einstellung der Spindelköpfe machbar. „Um die hohen Stellkräfte, die wiederum eine sehr hohe Steifigkeit des Systems erlauben, möglichst exakt und verlustfrei auf den Spindelkopf zu übertragen, haben wir um diesen einen sehr steifen, allerdings beweglichen Rahmen gelegt“, präzisiert LCM-Projektleiter Bernd Winkler. „Während zwei Druckkissenpaare innerhalb des Rahmens direkt auf den Spindelkopf wirken, wird die zweite Achse durch Druckkissen verändert, die von außen auf den direkt am Spindelkopf anliegenden Rahmen wirkt.“ Überraschungsfreie Entwicklungsarbeit.
Gebaut wird das Hydraulische Mikro-Positionierungssystem von LCM mit marktüblichen Regelventilen und Wegsensoren. Auch die Steuerung erfolgt über gängige Produkte. Nur sechs Monate dauerte die gesamte Planung und Konzeption des Systems. Und zwei Monate später stand ein voll funktionstüchtiger Prototyp zur Verfügung. Das erstaunte nicht nur Haas. „Auch die Entwicklung des serientauglichen Produktes konnte in nur zwei Wochen realisiert werden“, zollt der Technikleiter bei Anger dem LCM-Team Respekt. „Die größte Überraschung für uns war aber, dass es bis zum heutigen Tag weder in der Entwicklungsphase, noch während Inbetriebnahme oder im Echtbetrieb bei Daimler zu Überraschungen oder Verzögerungen gekommen ist“, betont er. „Das Mikro-Positionierungssystem war überraschend schnell voll einsatzfähig.“ Vielversprechende Perspektiven.
Der Ventilblock des neuen 9G-TRONIC-Getriebes wird seit Sommer 2013 mit den zwei Anger-Anlagen im Daimlerwerk Neckartal gebohrt und gefräst. Und das in 3-fach Bearbeitung. Produktionsunterbrechungen zur Nachjustierung der Spindelköpfe gibt es nicht, denn das von LCM entwickelte und programmierte hydraulische Mikro-Positionierungssystem arbeitet fehlerfrei. In Traun werden unterdessen bereits die nächsten beiden Anlagen für Daimler gefertigt. Die Lieferung erfolgt im Herbst. LCM-Geschäftsführer Gerald Schatz verrät überraschende Perspektiven, die bei der Weiterentwicklung des Mikro-Positionierungssystems hin zur nächsten Generation entstanden: „Durch einen digitalhydraulischen Ansatz ist es uns gelungen, die Komplexität des Systems nochmals zu verringern. Dadurch können wir mit einfacheren Komponenten arbeiten.“ Die Kosten des Gesamtsystems sowohl auf der Ventilebene als auch bei den notwendigen Sensoren kann somit nochmal deutlich reduziert werden. Elisabeth Biedermann