Verbindungstechnologien : Leichtbau: KVT-Fastening bietet neues Verbindungselement für Carbon
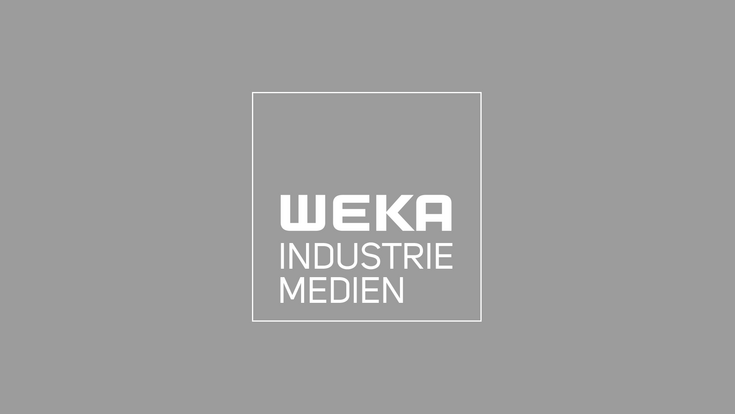
Traditionelle Verbindungssysteme, die für Metall und Holz entwickelt wurden, sind mit Verbundwerkstoffen oft nicht kompatibel oder erfordern große Zugeständnisse bei der Verarbeitung. Der bekannteste unter den Verbundstoffen sind die Kohlenstofffasern, auch Carbon genannt. Sie stehen stellvertretend für den Trend, altbewährte Materialen durch leichtgewichtigere und stabilere abzulösen. Bei Carbonplatten ist das herkömmliche Stanzen und Bohren oft nicht möglich, weil dadurch die Stabilität der eingebrachten Fasern zerstört und die Bauteilfestigkeit beeinträchtigt werden würde. Zum Einsatz kommen hier bigHeads, deren Prinzip so einfach wie genial ist: bigHeads zu deutsch „große Köpfe“ sind Grundplatten (Head), an denen mittels Schweißung beliebige Befestigungselemente – wie Stifte, Muttern, Gewindebolzen, Haken und dergleichen – angebracht werden können. Wobei die besondere Schweißung den USP (Alleinstellungsmerkmal) der bigHeads darstellt. In ihr steckt das ganze Know-How, das den bigHeads eine besonders hohe Stabilität verleiht.
Kleben statt bohren
Kohlenstofffaserverstärkte Kunststoffe in Autokarosserieteilen sind oft nur wenige Millimeter stark, was ein Problem bei der richtigen Befestigung darstellen kann. In diesem Fall können bigHeads bei der Produktion direkt in Carbon und andere Verbund- oder Kunststoffe integriert werden, wodurch sich beispielsweise optische und funktionelle Besonderheiten besser abbilden lassen, ohne dass hinsichtlich der Belastbarkeit Abstriche in Kauf genommen werden müssen. Die großen Grundplatten der intelligenten Befestiger können hier einfach einlaminiert oder auf Oberflächen sowie in Sandwichmaterialien eingeklebt werden. Das ist eine diskrete und effiziente Möglichkeit, selbst dünnste Strukturen, form- und funktionsbewahrend sowie prozesssicher zu verarbeiten. Ebenso ist die Einbettung in Kunststoffe durch Umspritzung möglich. Weder soll es zu Stauchungsfehlern noch Wölbungen kommen, die die Struktur optisch beeinträchtigen. Zudem müssen die Festigkeitsprüfungen belegen, dass das Produkt die gestellten Anforderungen dauerhaft erfüllen kann.
Vom Hybrid-Porsche bis zur Luxusyacht
Ein großes Einsatzgebiet für die bigHeads, die es in Stahl verzinkt oder Edelstahl gibt, ist die Automobil-Branche. Wobei bei Sportwägen aufgrund der Gewichtsoptimierung zunehmend Carbonteile zur Anwendung kommen. So wird im Hybrid-Porsche Spider 918 die Zuführung zum Lüftungskasten von diesen kleinen „großen“ Köpfen gehalten. Bei Aston Martin sind vor allem die aerodynamischen Front- und Heckspoiler mit bigHeads befestigt. Auch beim polnischen Rennauto Arrinera sind sehr viele (knapp 40) der intelligenten Befestiger in der Karosserie verbaut. Nachdem Edelstahl-bigHeads mit einer Qualität von AISI 316 eine See- und Chlorwasserbeständigkeit attestiert wird, erfreuen sie sich auch bei Yachten und Speedbooten großer Beliebtheit. Exklusivstes Beispiel ist der in Salzburg gefertigte Kormaran. Hier werden die bigHeads eingesetzt, um die Kabelstränge zu halten. Bei Sunreef-Yachten von HTEP hingegen dienen sie der Befestigung der Schallisolierung zum Lärmschutz in der Kabine.
Sicher und gut versteckt
Gemeinsam ist allen genannten Beispielen, dass die bigHeads stets sicher aber meist „unsichtbar“ sind, da weder Nieten noch Bohrlöcher und auch keine unschönen Schatten entstehen. Angebracht werden die Befestiger meist durch Laminieren oder mit Klebstoff, der Dank des Designs der Grundplatte gezielt durch die Löcher fließt und damit das Verbindungselement in Position hält, wodurch die gewünscht hohe Stabilität und eine besonders hohe Festigkeit erzielt wird.
Die Form folgt der Funktion
Aufgrund ihrer zahlreichen Vorteile kommen die Verbindungstechnologien von bigHead nicht nur im Fahrzeug- und Schiffsbau, sondern auch im Maschinenbau sowie in der Möbelindustrie zum Einsatz. Darüber hinaus finden sie in vielen weiteren Bereichen Verwendung, in denen anspruchsvolle Befestigungslösungen für Leichtbauweisen und speziell bei Verbundwerkstoffen erforderlich sind. Der Designleitsatz „Die Form folgt der Funktion“ lässt sich mit Verbundwerkstoffen für immer mehr Anwendungen in den unterschiedlichsten Branchen umsetzen. Die Produktpalette umfasst aktuell rund 1.000 verschiedene Ausführungen und 400 Standardprodukte und in ihrer Bauweise auch kundenspezifisch angepasst werden können.