Ersatzteile : Lagerleichen
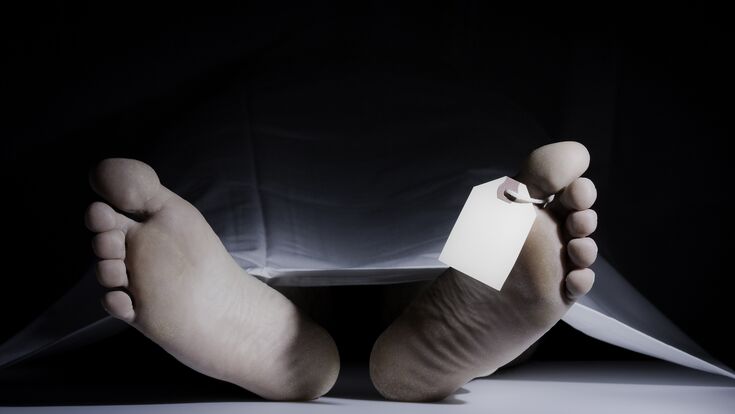
Buchhalterisch tot, aber original verpackt. Betritt Thomas Heller das Lager eines neuen Kunden, stechen sie ihm sofort ins Auge – die original verpackten Ersatzteile überzogen mit einer dicken Staubschicht. Lagerleichen säumen den Weg des Abteilungsleiters Anlagen- und Servicemanagement am Fraunhofer-Institut für Materialfluss und Logistik. Heller hat es sich zur Aufgabe gemacht, Unternehmen zu einem „World-Class-Ersatzteilmanagement“ zu führen. Der Weg bis dorthin: Mühsam, schwer und dennoch äußerst lohnenswert.
Ersatzteile werden häufig weder zentral noch systematisch beschafft. „Oft wissen Unternehmen gar nicht mehr, für welche Anlage das Teil eigentlich ist“, kennt Heller die Situation in den Ersatzteillagern vieler kleiner und mittelständischer Unternehmen. „Verlässt ein Mitarbeiter das Unternehmen, geht oft auch das Wissen um spezifische Teile mit verloren“, erklärt er weiter. Der Grund: Systematische Erfassung ist in vielen Unternehmen eine große Unbekannte. „Und selbst wenn die Notwendigkeit erkannt ist, fehlt es an Mitarbeitern, die diese Aufgabe übernehmen können.“ Damit steigen die Ersatzteilbestände ständig und damit auch die Lagererhaltungskosten für Unternehmen.
Der Aufwand schreckt ab.
“Nach wie vor fällt es vielen Betrieben schwer, ihre Ersatzteilbestände zu ordnen“, erklärt Heller. KMUs fehlen dafür einfach die nötigen Ressourcen. Die Erfassung von nicht identifizierten Ersatzteilen, den sogenannten Leichen, ist immer abhängig von der Ausgangssituation. „Hier trifft man von Karteikarten, Excel Listen bis zur selbstgestrickten Datenbank auf fast alles“, erklärt Heller. „Da kann es bis zu 30 Minuten dauern, bis alle erforderlichen Daten für ein einziges Ersatzteil gesammelt sind.“ Bei einem Durchschnittslager von rund 20.000 Teilen bedeutet das einen Aufwand von Mannjahren, umso mehr, wenn es an professioneller Unterstützung und Einbindung der Lieferanten fehlt. „Das sind Dinge über die Unternehmen einfach nicht gerne sprechen“, kennt Oliver Hofbauer die schwierige Situation so mancher Unternehmen. Der Geschäftsführer von H&H Systems entwickelt mit seinem Unternehmen das Instandhaltungsmanagementsystem ISPRO-NG, welches Betriebe bei der Errichtung eines strukturierten Ersatzteillagers unterstützt.
Eine große teure Wunde.
Dass Factory hier den Finger auf eine große Wunde legt, weiß auch Hubert Biedermann. „Wir reden hier nicht von Schütt- und Schaufelgut“, so Biedermann. Unternehmen lagern oft Ersatzteile im Wert von mehreren Zigtausend Euro. „Und wer schon einmal eine 4.000 Euro Pumpe original verpackt, verschrotten musste, weil sie in die neue Anlage nicht mehr passt, tut das weh.“ Der Leiter des Department Wirtschafts- und Betriebswissenschaften an der Montanuniversität ist fassungslos: „Es ist unglaublich was sich Unternehmen da durch die Lappen gehen lassen“, sagt Biedermann. „Wir gehen teilweise durch Lager und könnten ad hoc die Bestände um bis zu 30 Prozent senken.“ Mit einer einfachen Hochrechnung verdeutlicht der Professor was für Einsparungspotenzial auf Unternehmen da wartet. „Angenommen ein Unternehmen hat ein Ersatzteillager im Wert von einer Million Euro, davon entfallen circa 20 Prozent auf die jährlichen Lagerhaltungskosten. Senkt man diesen Bestand, könnten sich Unternehmen erhebliche Summen sparen.“ Biedermann ist felsenfest davon überzeugt, dass hier ein riesiges Potenzial auf Unternehmen wartet. „Damit könnten Arbeitsplätze gerettet werden.“
Lesen Sie weiter auf Seite 2: Betriebe sträuben sich.
Dennoch bauen vor allem KMUs ihre Barrikaden hoch. Der Aufwand für die Erfassung eines ordentlichen Materialstammsatzes in der ERP Software ist einfach zu groß. Das Ersatzteillager zu straffen, geht dennoch. Hofbauer und sein Team helfen Ihren Kunden bei der Errechnung des Mindestlagerbestands, dafür verwenden sie eine eigens entwickelte Instandhaltungssoftware ISPRO-NG. „Einkäufe, Verbräuche werden dokumentiert und der optimale Wiederbeschaffungszeitpunkt ermittelt. Damit lässt sich das Lager ziemlich straffen“, erklärt er. Auch am Fraunhofer-Institut wird mit Hilfe einer Risikoanalyse an dem Problem unnötiger Lagerbestände gefeilt. Mit Hellers ERBORAS-Methode lässt sich ausrechnen, wie wahrscheinlich es ist, dass innerhalb der Wiederbeschaffungszeit das Ersatzteil wieder benötigt wird. Damit lässt sich ermitteln, wie viele Teile am Besten bestellt und gelagert werden sollten“, sagt Heller.
Lösung: Konsignationslager.
Eine weitere Lösung die riesige Konzerne wie die voestalpine und Magna bereits anwenden, kennt Biedermann. „Ein Konsignationslager ist ein Lager, dass zwar dem Lieferanten gehört, aber vor Ort ist“, so der Professor. „Nur wer etwas rausnimmt, zahlt“, erklärt Biedermann. Diese Poolinglösung wäre besonders für KMUs attraktiv, trotzdem regt sich da Wiederstand. „Der Mitbewerb soll nichts wissen“, nennt Biedermann einen Grund. Den nächsten liefert Heller: „Es ist einfach menschlich, sich Sachen auf die Seite zu legen und nicht außer Haus zu geben.“ All diese Lösungen könnten zumindest in Zukunft Schluss mit unnötigen Ersatzteillagern machen. Aber die verstaubten Leichen in den Lagern der KMUs bleiben dennoch und werden wohl auch in zehn Jahren noch nicht vollständig verschwunden sein.