Hannover Messe : Kaeser präsentiert erstmals frequenzgeregelte ASD-Kompressoren-Reihe
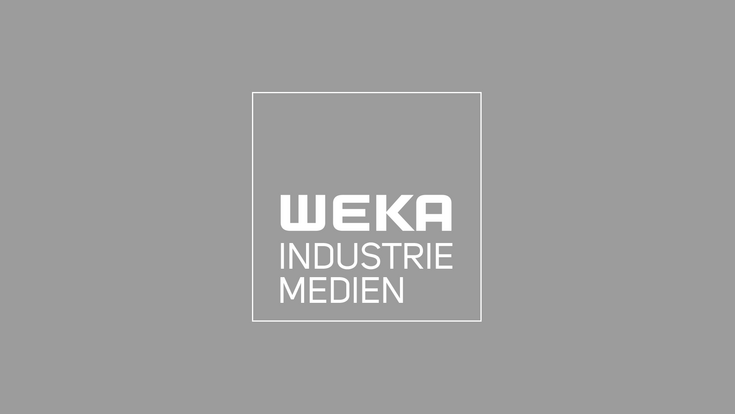
Der verantwortungsvolle Umgang mit Ressourcen gehört zu den wichtigen Erfolgsfaktoren von Kaeser Kompressoren in Coburg. Als einer der bedeutendsten Druckluft-Systemanbieter und Trendsetter der Branche präsentiert das Familienunternehmen zur Hannover Messe 2017 erneut einen Meilenstein: Die frequenzgeregelte ASD-Kompressoren-Reihe wird erstmals mit einem Synchronreluktanz-Motor ausgerüstet, der gerade im Teillastbereich deutlich geringere Verluste gegenüber Asynchronmotoren aufweist.
„Unser Ansporn ist der hohe technologische Anspruch, für den Kaeser Kompressoren weltweit bekannt ist“, betont Wolfgang Hartmann, Leiter Internationales Marketing und Technik-Experte bei dem Familienunternehmen aus Coburg. Hintergrund seiner Aussage ist die stetige Optimierung der Drucklufterzeugungssysteme und deren hoher Effizienzgrad. Beispielsweise hat das Unternehmen schon vor vielen Jahren – lange bevor die heute geltenden gesetzliche Regelungen in Kraft getreten sind – seine Kompressoren-Baureihen auf energiesparende IE3-Elektromotoren umgestellt und damit seine Vorreiterrolle als einer der bedeutendsten Druckluft-Systemanbieter gestärkt.
Seit gut zwei Jahren folgt sukzessive der nächste Schritt zur Erhöhung der Energieeffizienz, nämlich die konsequente Umstellung aller Hightech-Kompressoren im Leistungsbereich von 30 kW bis 315 kW auf High Efficiency Elektromotoren der Energieeffizienzklasse IE4. Wolfgang Hartmann bestätigt: „High-End-Verdichterqualität ist direkt gekoppelt mit höchster Energieeffizienz, so dass wir auch bei den Antrieben die bestmögliche Lösung für unsere Kunden zur Verfügung stellen.“
Nun folgt der nächste Schritt, den der Trendsetter zur Hannover Messe 2017 erstmals einer breiten Öffentlichkeit vorstellt und damit seine Rolle als Premium-Anbieter untermauert. Das Unternehmen bringt die drehzahlgeregelten Schraubenkompressoren der ASD-Baureihe mit einer völlig neuen Antriebstechnik auf den Markt. Der größte Vorteil dieser, mit dem Systempartner Siemens entwickelten Gesamtlösung ist: Bis zu zehn Prozent Wirkungsgradverbesserung im Teillastbereich. Für Wolfgang Hartmann ein weiterer Meilenstein in der technologischen Erfolgschronik von Kaeser: „Dieses seit Jahrzehnten bekannte Antriebsprinzip ist nun technisch so perfekt in Serienmotoren realisiert, dass Anwender weltweit davon profitieren.“
Geregelte Antriebslösung mit hohem Systemwirkungsgrad
„Aus unserer Sicht ist eine solche systematische Effizienzerhöhung im Teillastbereich die logische Konsequenz aus den Klimaschutzbestrebungen wie sie sämtliche Regierungen weltweit in ihren Klimaprotokollen beschließen“, betont Wolfgang Hartmann und spannt damit den Bogen zur technologischen Umsetzung: „Mit unserer drehzahlgeregelten Variante der ASD-Baureihe bieten wir Kunden weltweit den Einstieg in ein Minimum an Energieverbrauch – und Betriebskosten.“ Denn häufig sind Druckluftstationen modular aufgebaut: Stetig laufende Kompressorsysteme mit IE3 und IE4-Motoren übernehmen dabei die Grundlastversorgung und zusätzliche Spitzenlastkompressoren decken flexibel den erhöhten Druckluftbedarf ab effizient im Verbund geregelt durch den Sigma Air Manager 4.0. Dies geschieht künftig mit Synchronreluktanz-Antriebssystemen von Siemens mit besonders hohen Wirkungsgraden im Teillastbereich.
Als Praktiker weiß er um die hohe Bedeutung der neuen Synchronreluktanz-Motoren von Siemens. Entwickelt wurden sie vor dem Hintergrund, dass die neue Norm EN 50598 nicht nur die Einzelwirkungsgrade von Antrieben mit einbezieht, sondern die Systemwirkungsgrade in den Mittelpunkt der ökologischen Betrachtung rückt und somit frequenzgeregelte Antriebslösungen nach ihrer ganzheitlichen Wirksamkeit beurteilt.
Vom Synchron- und Asynchronmotor das Beste
Sofort stellt sich die Frage: Was ist grundlegend anders bei der Synchronreluktanz-Technologie, die auf der Plattform der Simotics GP/SD von Siemens basiert. Antwort: Diese neue, innovative Standardmotorenreihe vereint die Vorteile von Asynchronmotoren und Synchronmotoren in einem Antrieb. Im Läufer wird weder Aluminium, Kupfer noch teure seltene Erden Magnete verwendet, sondern Elektrobleche mit spezieller Profilierung aneinander gereiht. Das macht den Antrieb robust und servicefreundlich wie man es von Asynchronmaschinen her kennt.
Dagegen sind die Regeleigenschaften mit denen von Synchronmotoren vergleichbar: Reluktanzmotoren weisen aufgrund der spezifischen Läuferkonstruktion eine hohe Dynamik auf und im Läufer findet keine zusätzliche Erwärmung aufgrund von Stromfluss statt. Entscheidend ist die optimale Anpassung des gesamten Antriebssystems, also von Frequenzumrichter und Motor. Hier setzt Kaeser auf den Sinamics G120, der mit einem speziell angepassten Regelalgorithmus auf den Motor angepasst wurde und zusammen das Synchronreluktanz-Antriebssystem bildet. Diese Kombination ist optimal aufeinander abgestimmt und schafft so die Möglichkeit der maximalen Energieeinsparung.
Wolfgang Hartmann berichtet: „Zusammen mit unserem Entwicklungspartner Siemens haben wir diese innovative Antriebsvariante so weit optimiert, dass nun Drehzahlen bis in die Größenordnung von 4.000 Umdrehungen pro Minute möglich sind.“ Das bedeutet neben der Energieeffizienz: Leistungssteigerung bei gleicher Baugröße. Interessant ist in diesem Zusammenhang, dass sich die Gehäuse- und Fußabmessungen des Synchronreluktanz-Motors nicht vom Asynchron-Motor unterscheiden. Kurzum: Die direkte Substitution ist ohne großen Engineering-Aufwand möglich; Anwender können sich also je nach Anwendung flexibel für die eine oder die andere Antriebslösung entscheiden. „Ein solches Systemdenken unterstreicht unsere Standardisierungsstrategie“, ergänzt der Experte bei Kaeser.
Bei gleicher Baugröße spürbar mehr Performance
Der Premium-Kompressorenhersteller setzt mit der drehzahlgeregelten Serie und dem Synchronreluktanz-Antriebssystem erneut einen technologischen Meilenstein. Während diese Kompressoren bisher mit Frequenzumrichter und IE3-Energiesparmotoren nach dem Asynchronprinzip ausgerüstet wurden und somit ökologisch die Speerspitze der Drucklufterzeugung bilden, „wollen wir in den nächsten Jahren weitere Leistungsklassen mit Reluktanzmotoren ausrüsten“, betont Wolfgang Hartmann. Oder anders formuliert: Bei gleicher Baugröße spürbar mehr Leistung. Dabei liefert Siemens an Kaeser eine vollständig getestete, abgestimmte und optimierte Systemlösung. Ebenso zeigt der Wirkungsgradvergleich (im Diagramm am Beispiel eines 30 kW Motors), was heute bereits möglich ist.
Beispielsweise treten im Läufer prinzipbedingt kaum Wärmeverluste auf, so dass die Lagertemperatur spürbar geringer ist. Das wirkt sich positiv auf die Lebensdauer und somit auf die Servicefreundlichkeit sowie die Verfügbarkeit der Antriebe aus. Wolfgang Hartmann bestätigt: „Durch die optimale thermische Auslastung der Motoren ergeben sich damit noch längere Serviceintervalle als wir sie bisher schon anbieten.“ Auch die Entwärmung der Schaltschränke profitiert davon, so dass auch hier weniger Abwärme nach draußen geführt werden muss. Aufgrund des Einsatzes drehzahlgeregelter Lüfter in Drucklufterzeugungssystemen bei Kaeser ergeben sich somit zusätzliche Einspareffekte.
Innovatives Antriebssystem für eine nachhaltige Zukunft
Wer sich von den Vorteilen der neuen Antriebstechnik überzeugen will, wird auf der Hannover Messe 2017 fündig. Dort werden die Kaeser-Schraubenkompressoren der ASD-Baureihe mit einer Liefermenge von 3,15 bis 5,5 m3/min bei 8,5 bar gezeigt. Erstmals sind sie dann mit den innovativen Synchronreluktanz-Motoren von Siemens ausgerüstet, die im Teillastbereich eine Wirkungsgradverbesserung von bis zu zehn Prozent, eine Top-Eingruppierung mit IES2 in der neuen Energieeffizienznorm EN 50598 sowie erneut deutlich geringere Energiekosten bieten. Durchschnittlich könnten so nach Angaben des Kompressorenherstellers rund 450 Euro pro Jahr an Energiekosten eingespart werden – gerechnet bei rund 6.000 Betriebsstunden und zehn Cent pro Kilowattstunde.
Verantwortlich dafür ist das innovative Funktionsprinzip, das Siemens bei der Entwicklung der Synchronreluktanz-Motoren umgesetzt hat. Der Verzicht auf teure Werkstoffe wie Aluminium, Kupfer und seltene Erden Magnete im Läufer macht die Motoren nicht nur kostengünstig, sondern sorgt auch in regelungstechnischer, energetischer und thermischer Hinsicht für erhebliche Vorteile – vor allem im Teillastbereich. Es gibt diese Motoren nun standardmäßig mit Aluminium- und Grauguss-Gehäuse auf der Plattform der energieeffizienten 1LE1-Asynchronmotoren als Simotics GP/SD.
Damit erhalten Anwender ein Maximum an Flexibilität hinsichtlich Einsatzfall bzw. Umgebungsbedingung, aber auch in Bezug auf das Lastverhalten. Damit betritt Siemens neben den hocheffizienten IE4-Asynchronmotoren eine weitere Stufe der Energieeffizienzsteigerung in der Antriebstechnik und sorgt für ökologischen Wettbewerbsdruck. Wolfgang Hartmann freut sich: „Ökologische Argumente sind bei qualitativ hochwertigen Verdichterlösungen die wichtigsten, um die Industrie in eine nachhaltige Zukunft zu begleiten.“