Digitalisierung : Kärntner erschaffen digitalen Zwilling der Produktion
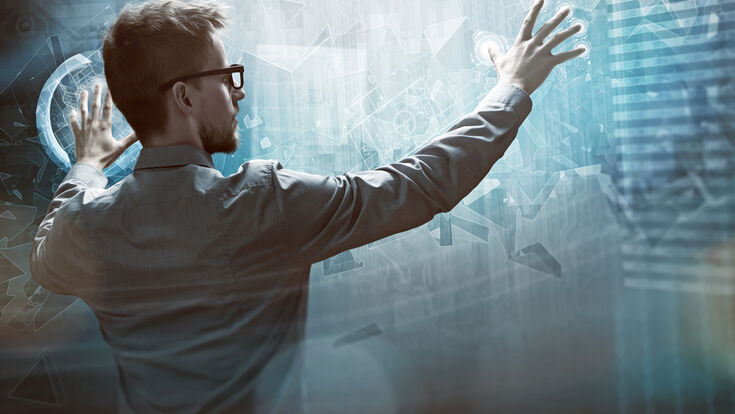
Nachträgliche Anmerkung: Die Gesellschaft proscicon wurde mit Ende Juni 2016 aus privaten Gründen aufgelöst und das betreffende Projekt auch nicht mehr begonnen.
Gottfried Seebacher ist eigentlich ein offener Mensch. Geht es aber um seine Endkunden – genauer gesagt seine neuesten Projekte - stößt so ziemlich jeder bei dem Geschäftsführer der proscicon auf Granit. Zu Recht – denn derzeit wird der Traum einer digitalen Fabrik in der Kärntner Ideenschmiede äußerst fein gesponnen. Fast still und heimlich haben Seebacher und sein Team erstmals Kennzahlen für das Messen der Gesamteffizienz einer Produktion entwickelt. „Damit sind wir die ersten die Flexibilität und Effizienz in einer Fertigung und Logistik messbar machen“, erklärt er.
Bewaffnet mit diesen einzigartigen Indikatoren haben sich die Kärntner Simulationsspezialisten Anfang Februar einen besonders dicken Fisch an Land gezogen. Aktuell führen sie Gespräche mit einem großen deutschen Antriebshersteller. Für diesen wollen sie einen digitalen Zwilling der Fertigung schaffen. In sehr kurzen Taktzeiten soll dieser damit verschiedenste Produktionsszenarien parallel zur Fertigung durchspielen können.
Die Macht der Excel-Listen brechen
Der Traum vom digitalen Zwilling geistert durch viele Fertigungshallen. Produktionsverantwortliche kennen nur zu gut das Potenzial dahinter. Verschiedenste Fertigungsszenarien parallel zum eigentlichen Prozess simulieren zu können, um damit die effizienteste Fertigungsvariante für die nächste Charge zu wählen, sind Visionen, die sich so mancher sehnlichst wünscht. Eine Vision, die aber immer noch auf dieselben Probleme stößt. Die Macht von Excel-Listen in KMUs bleibt ungebrochen. Die damit verbundenen Inseln, zerstören den Nährboden eines digitalen Zwillings. Auch Unternehmen die Daten bereits mithilfe eines MES (Manufacturing Execution System) erfassen, „können zwar bereits gehen, aber noch lange keinen Marathon laufen“, verbildlicht Seebacher es. Zu oft bleibt eine statistische Auswertung und Analyse der Daten auf der Strecke.
Erstmals messbare Gesamteffizienz
Die Daten liegen brach. „Reine Geldverschwendung“, meint auch Seebacher. Und jene Unternehmen, die immer noch meinen „meine Prozesse sind aber anders“, nimmt Seebacher nur zu gern den Wind aus den Segeln. Seiner Meinung nach ist die Prozesslandschaft bis zu einem geringen Prozentsatz in jeden Unternehmen ähnlich. Im Rahmen seiner Forschungsarbeiten besuchte er drei Produktionsbetriebe. In einem Holzverarbeitungsbetrieb untersuchte er dessen Supply Chain, bei einem Zulieferbetrieb die Produktion und bei einem Dämmstoffhersteller die Logistik. Aus diesen drei Pilotfabriken entwickelte er seine einzigartigen Kennzahlen für die Flexibilität und die Effizienz der Produktion sowie der Produktionslogistik. „Aus diesen können wir dann wiederum die Gesamteffizienz eines Unternehmens berechnen“, so Seebacher. Zugrunde liegt den Kennzahlen dabei ein generisches Modell entwickelt aus einer prototypischen Simulationsstudie direkt in den Unternehmen. „Dabei wurden zB bei der EPP (Kennzahl für Effizienz der Produktionslogistik) Zeitverluste bei der Abwicklung der produktionslogistischen Aufgaben erfasst“, so Seebacher. Indem die produktive Transportabwicklungszeit ins Verhältnis mit der tatsächlich verfügbaren Abwicklungszeit gebracht wird, ergibt sich dann der entsprechende Indikator.
Gesamteffizienz bleibt mau
Seebacher ist ehrlich. „Das Ergebnis der Gesamteffizienz erschreckte die Betriebe“, so der Kärntner. Denn eine Gesamteffizienz von 20 Prozent war keine Seltenheit. Seebacher betont aber, dass seine Kennzahl nicht zwangsläufig immer 100 Prozent ergeben muss. „Branchenprimus kann hier auch ein Betrieb mit 25 Prozent sein“, so der Kärntner. Geht es aber um Investorenakquise wird das natürlich schlagend. Denn ein Euro Investition ist somit plötzlich nur mehr 20 Cent wert. Seit den 80er Jahren gibt es das „leane“ Gedankengut, aber immer noch herrscht Verschwendung in den Systemen. Seebacher weiß das aus eigener Erfahrung. Etwas mit dem die Kärntner nun aufräumen wollen.
Kennzahlen alleine helfen aber auch nicht, das weiß auch Seebacher. „Nur weil man seine Gesamteffizienz kennt, weiß man noch lange nicht, wo die Baustellen liegen“, betont er. Genau dafür haben sich die Kärntner aber schon längst eine eigene Lösung einfallen lassen. In Echtzeit können sie jedes mobile Endgerät mittlerweile mit ihren Kennzahlen bespielen. Mit einer Drill-Down Funktion kann der Kunde direkt in seine Prozesse blicken. „Das heißt mit einem Klick sieht er genau, in welchem Bereich gerade ein Effizienzverlust vorliegt und kann reagieren“, so Seebacher.
Einen Schritt weiter wollen die Kärntner eben bei jenem Antriebshersteller gehen. Dieser soll gleich einen simulationsfähigen digitalen Zwilling seiner Fertigung bekommen. „Damit kann der Produktionsleiter verschiedenste Fertigungssimulationen durchspielen“, so Seebacher. „Die Effizienz der einzelnen Szenarien wird über unsere Kennzahlen ermittelt. “Somit kann das Unternehmen entscheiden, welches Szenario am Effizientesten ist und dieses dann in der echten Fertigung ablaufen lassen.
Die proscicon-Kennzahlen im Überblick
Die OPE bildet die Anlageneffizienz von Anlagengruppen, gesamten Produktionslinien und/oder gesamter Produktionsstandorte unter zusätzlicher Berücksichtigung der Bestandssituation ab.
Die EPP beschreibt zusätzlich die Effizienz bei der Durchführung produktionslogistischer Aufgaben und erfasst dazu sämtliche in der Produktionslogistik auftretenden Verluste.
Die Gesamtsystemeffizienz errechnet sich schließlich aus der Anlageneffizienz und der produktionslogistischen Effizienz.
Nachträgliche Anmerkung: Die Gesellschaft proscicon wurde mit Ende Juni 2016 aus privaten Gründen aufgelöst und das betreffende Projekt auch nicht mehr begonnen.