Additive Fertigung : Gerfertec macht additives Aufschweißverfahren serientauglich
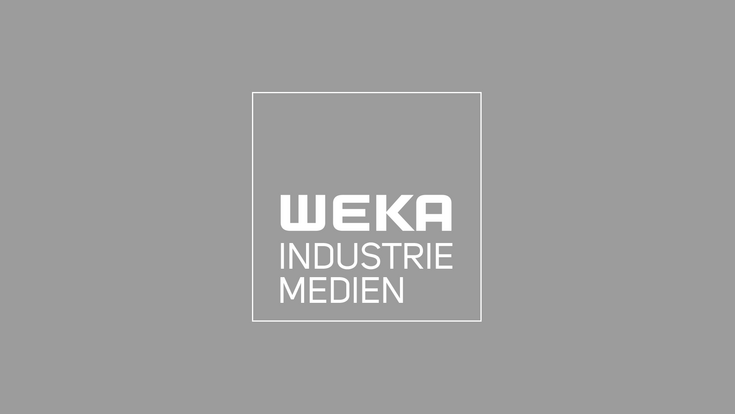
Es ist ein Wettlauf mit der Zeit und ein Wettlauf mit der Konkurrenz. Viele forschen am Thema 3D-Druck mit Draht, doch niemand ist ein marktreifes Produkt gelungen. Bis jetzt. Tobias Röhrich, Geschäftsführer des Berliner Start-Ups Gefertec macht als Erster das additive Aufschweißverfahren 3DMP kommerziell verfügbar. Das Verfahren basiert auf Lichtbogenschweißen und verwendet als Ausgangsmaterial Draht, mit dem Schweißraupe für Schweißraupe ein Werkstück gedruckt wird. „Es handelt sich dabei um das wirtschaftlichste additive Verfahren, wenn es darum geht, große Bauteile aus metallischen Werkstoffen bei hohen Auftragsraten zu fertigen“, erklärt Röhrich.
Wachstum in Amerika
Als Schnittstelle zwischen den Plandaten und der Lichtbogenschweißanlage dient eine eigens entwickelte Software, die die CAD-Daten in einzelne digitale Druckschichten, die CAM-Modelle, zerlegt. Mit diesen Daten nimmt die CNC-Steuerung die exakte Positionierung des Schweißkopfs vor. Die Fertigung des endkonturnahen Werkstücks erledigt die Maschine dann vollautomatisch; die Endbearbeitung erfolgt mit herkömmlicher CNC-Frästechnik. Obwohl das Verfahren völlig neu ist und die Marktbearbeitung für das Berliner Start-up, das vor zwei Jahren gegründet wurde, erst mit der EMO so richtig gestartet ist, hat man große Pläne: „Wir wollen schnell wachsen, auch der Schritt nach Amerika ist bereits für nächstes Jahr in Planung. Unsere Technologie ist ausgereift, der Markt ist groß – und wir rechnen mit einer relativ großen Wachstumskurve für unser Unternehmen“, so Röhrich. Basis dafür soll das breite Anwendungsfeld des so genannten 3DMP-Verfahrens (kurz für „3D-Metal-Print“) sein: „Unsere Technologie kann alle klassischen Fertigungs- und Bearbeitungsverfahren für Metallteile wie Umformen, Trennen, Fügen, Beschichten, Fräsen oder Drehen ablösen. Das bedeutet, jedes Unternehmen, dass heute fräst, kann schon morgen mit 3DMP arbeiten.“
Wirtschaftlich und schnell
Die Vorteile seien vor allem die hohe Kostenersparnis im Vergleich zur konventionellen Fertigung und auch im Vergleich zu anderen 3D-Druckverfahren. Das liegt einerseits daran, dass Draht wesentlich günstiger als Pulver ist – und das aufwändige Pulverhandling, das ebenfalls Geld und Ressourcen benötige, wegfalle. „Größter Vorteil ist aber mit Sicherheit die sehr hohe Aufbaurate. Sie beträgt, je nach verwendetem Werkstoff, aktuell bis zu 600 Kubikzentimeter pro Stunde. Dadurch eignet sich die GTarc-Maschine für die schnelle und wirtschaftliche Fertigung auch größerer Werkstücke aus Stahl, Nickelbasis, Titan oder Aluminium.“
Arbeiten, wie mit einer CNC-Maschine
Der 3D-Drucker GTarc, den das Berliner Unternehmen entwickelt hat, ist als 3-achsige Variante für Werkstückgrößen bis drei Kubikmeter oder 5-achsig für Werkstückgrößen bis 0,8 Kubikmeter erhältlich. Ganz neu ist die „GTarc 60-5“, die im November auf der Fachmesse „formnext“ erstmals vorgestellt wurde: Sie eignet sich für Werkstückgrößen bis 60 Liter und 200 Kilogramm; der maximale Durchmesser der Bauteile beträgt 450 Millimeter. „Das Besondere ist die einfache Bedienung: Die Maschine arbeitet wie eine klassische Werkzeugmaschine mit einer CNC-Steuerung. Das bedeutet, ein Facharbeiter, der bisher auf CNC-Maschinen gearbeitet hat, wird auch mit unserer Anlage problemlos arbeiten können“, sagt Röhrich.