Technik Reportage : Gamification: Wie Knapp die Getriebefertigung bei Pankl Racing optimiert
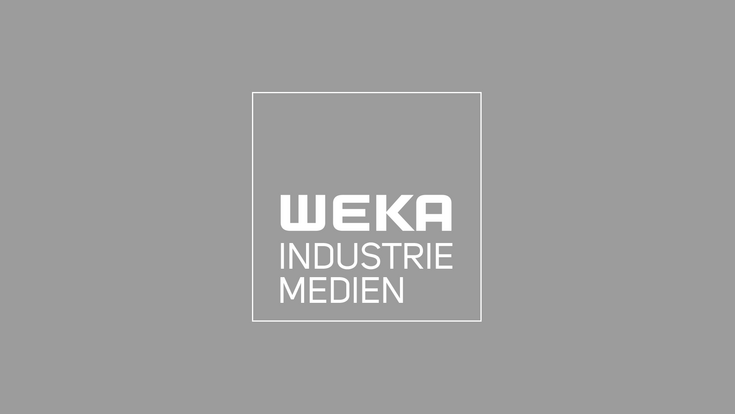
Superbike, Enduro, Motocross oder X-Bow, dafür steht KTM als Motorrad- und Sportwagenhersteller. Die Pankl Racing AG mit Hauptsitz in Österreich ist Teil der internationalen KTM Industries-Gruppe und auf die Bereiche Aerospace, Racing sowie High Performance spezialisiert. Pankl High Performance Systems produziert als neue Sparte der Pankl Racing AG hochwertige Getriebe. 2016 wurde dafür eine moderne Produktionsstätte in Kapfenberg errichtet. Hier werden Forschung und Entwicklung über Produktion und Testeinrichtungen gebündelt, um eine innovative Getriebefertigung zu realisieren. Für die Automatisierung des Montagebereichs am neuen Standort entschied sich Pankl für eine spannende, innovative Lösung der Knapp-Gruppe.
Getriebe im 3-Minuten-Takt
Am Anfang standen hohe Ziele. Die automatisierte Produktionsleistung in Kapfenberg sollte nämlich volles Tempo bei null Fehlern bringen. Bis zu 160.000 Getriebe pro Jahr und damit eine Taktzeit von 3 Minuten pro Getriebe war der Zielwert für das neue Werk. Neben einer Integration der gesamten Wertschöpfungskette unter einem Dach war eine effektive Automatisierung für die hohen Produktionsziele unumgänglich. Neben höchster Qualität, durchgängiger Prozesskontrolle und Erweiterbarkeit war starke Flexibilität für die Automatisierung gefordert, denn neun Offroad-Getriebe und drei für Straßenserien werden am Standort gefertigt. Für die Umsetzung dieser hohen Anforderungen entschied sich Pankl für eine integrierte Lösung aus der Knapp-Gruppe, die automatische und manuelle Tätigkeiten in einem intelligenten Montageprozess vereint. „Das Knapp-Team hat sehr schnell verstanden, was wir brauchen, und in der Konzeptphase ein hohes Maß an Kreativität eingebracht, um die richtige Lösung zu finden“, so Michael Mayer, Plant Manager bei Pankl High Performance Systems, im Rückblick auf die Entscheidung zur Kooperation, „mit dem automatischen Lagersystem haben wir eine bewährte Technologie im Einsatz, da es durch seinen modularen Aufbau mit unseren steigenden Produktionszahlen mitwachsen kann.“
Montage voll im Griff
Die Montagelösung bei Pankl spielt dank Knapp viele intelligente Stücke: Ein automatisches Kleinteilelager mit 3D-fähigen Shuttles versorgt die Montagearbeitsplätze nach dem Ware-zur-Person-Prinzip, moderne Bilderkennungs- und Bildverarbeitungstechnologie überprüft jeden Arbeitsschritt und stellt einen fehlerfreien Zusammenbau der Getriebe sowie eine lückenlose Verfolgbarkeit sicher. Und der Softwareeinsatz hilft dabei: „Dazu hat Knapp maßgeschneiderte Montagearbeitsplätze entwickelt“, erläutert Michael Mayer die Vorteile der Automatisierungslösung, „das System integriert sich damit nahtlos in unser Konzept, den gesamten Fertigungsprozess personifiziert rückverfolgbar zu gestalten.“ Warum kann die Lösung von Knapp das erreichen: All das liegt an der gesamtheitlichen Software KiSoft One, die Auftragsverteilung und Verwaltung übernimmt und gleichzeitig Schnittstelle zwischen der Knapp-Anlage und dem ERP-System von Pankl ist. Alle Benutzeroberflächen sind im easyUse-Prinzip ausgeführt, das einfache Bedienung und benutzerorientierte Darstellung an allen Arbeitsplätzen und auf allen Endgeräten ermöglicht. Die intelligente Software ivii.core unterstützt alle qualitätssichernden Maßnahmen am Arbeitsplatz ivii.smartdesk. KiSoft SCADA rundet die Softwarelösung ab und visualisiert die Anlage in 3D bis zur Sensorenebene und zeigt den Anlagenzustand in Echtzeit.
Lagern im Shuttle-System
Automatisierte Montage fängt schon mit exakt geregeltem Teilemanagement an. Nach der Anlieferung werden die Teile und Rohmaterialien zunächst in einem Verschieberegal gelagert. Schüttgut, das später für den Zusammenbau der Getriebe benötigt wird, wird direkt im YLOG-Shuttle-System eingelagert. Das Rohmaterial wird zu den Fertigungsmaschinen befördert, dort bearbeitet und danach in der Waschanlage gereinigt. Von der Waschanlage gelangen die Halbfertigteile in Gitterkörben auf einer Fördertechnik zum Wareneingangs-Arbeitsplatz an der Rückseite des YLOG-Shuttle-Systems, gesteuert von KiSoft SRC aus dem Hause Knapp. Das automatische Kleinteilelager erstreckt sich über 7 Längs- und 2 Quergassen, automatisiert wird das Regal mit 6 Shuttles, die über 2 Lifte die Ebenen wechseln. Über ein Schienensystem verlassen die Shuttles das Regal und versorgen die Montagearbeitsplätze. Das Echtzeit-Feedbacksystem, mit dem der ivii.smartdesk ausgestattet ist, überwacht den Zusammenbau der Getriebe und setzt damit eine Null-Fehler-Strategie und durchgängige Rückverfolgbarkeit im Montageprozess um.
Montage am ivii.smartdesk
Der Einsatz von ivii.smartdesk verbindet maximale Qualität im Montageprozess mit maximaler Leistung, um die hohen Produktionsziele von Pankl zu unterstützen. Gleichzeitig ist der spielerische Ansatz der Arbeitsschritte – die Gamification – motivierend für die Mitarbeiter und trägt zu einer lernenden Organisation bei. „Mit dieser Produktion erreicht Pankl eine neue Ebene, was die integrale Vernetzung vom Rohteil bis zum Fertigteil über alle Fertigungsprozesse, Qualitätsdaten, Betriebsdaten und Montagedaten anbelangt“, betont Christoph Prattes, COO Pankl Racing AG, „wir erreichen eine hohe Transparenz und Nachvollziehbarkeit – und damit eine hohe Effizienz in der Abarbeitung.“ Und er ist mit dem Ergebnis voll zufrieden: „Hier haben wir sicher eine Best-Practice-Anwendung für die vernetzte Produktion geschaffen.“ Dass diese Strategie auch für die Belegschaft motivierend ist, freut Christoph Prattes besonders: „Unsere Mitarbeiter sehen das Feedbacksystem nicht als Überwachung, sondern als willkommene Unterstützung, um ihre Arbeit in bester Qualität und schnellster Zeit umzusetzen – und so unsere Ziele zu erfüllen.“
Die Anwendung auf einen Blick
Knapp Smart Production
Was: Beinhaltet ein automatisches Kleinteilelager mit 3D-fähigen Shuttles zur Lagerung der Getriebeteile und ivii.smartdesks - innovative Montagearbeitsplätze - mit Echtzeit-Feedbacksystem. Dieses überwacht den Zusammenbau von Getrieben und gewährleistet die durchgängige Rückverfolgbarkeit und die Umsetzung einer Null-Fehler-Strategie auch im Montageprozess.
Besonders weil: Ein spielerischer Ansatz – Gamification –, der motivierend für die Mitarbeiter ist und damit zu einer lernenden Organisation beiträgt.
Anwendung bei Pankl: Montage von Motorradgetrieben, 9 Offroad, 3 Straßenserien
Lagersystem: Ylog-Shuttle, 6 Shuttles, 2 Cross-Lifte
Lagerstellplätze: 4.368
Leistung: 26 Getriebe/Stunde/Arbeitsplatz in zwei Schichten
Ziel im Endausbau: 160.000 Getriebe in drei Schichten
Arbeitsplätze: 4 ivii.smartdesk
Software: KiSoft One, KiSoft SCADA, KiSoft SRC, ivii.core, easyUse-Benutzeroberfläche
Zum Auftraggeber: Pankl Racing Systems AG entwickelt, erzeugt und vertreibt Motor- und Antriebssysteme sowie Fahrwerksteile für den Rennsport, für High-Performance-Autos und die Luftfahrtindustrie. Pankl punktet in diesen Nischenmärkten mit Leichtbaukomponenten aus hochwertigen und innovativen Werkstoffen, die für extreme mechanische Belastungenausgelegt sind. Der High-Performance-Bereich spezialisiert sich auf die Produktion von Motor- und Antriebskomponenten für Luxusautomobile und wurde in den letzten Jahren sukzessive expandiert. Pankl zählt zur KTM Industries-Gruppe, einer führenden europäischen Fahrzeug-Gruppe, die den strategischen Fokus auf das globale Sportmotorradsegment und den automotiven High-Tech-Komponentenbereich legt.
Zum Auftragnehmer: Die Knapp-Gruppe mit Hauptsitz in Hart bei Graz ist ein Anbieter intralogistischer Komplettlösungen und automatisierter Lagersysteme und hat sich auf die Kernbranchen Healthcare, Fashion, Retail, Food Retail und Industry spezialisiert. Mit mehr als 30 Standorten, über 3000 Mitarbeitern und einer Exportquote von 97 Prozent betreut Knapp Kunden weltweit. Knapp Industry Solutions ist der Spezialist für maßgeschneiderte Lösungen für die Industrie-, Produktions- und Distributionslogistik innerhalb der Knapp-Gruppe. Mit skalierbaren Shuttle-Lösungen und freifahrenden Transportsystemen verfügt das Unternehmen über Technologien, die im industriellen Umfeld neue Möglichkeiten hinsichtlich Flexibilität und Verfügbarkeit bieten.