3D-Druck : Flying (very) high
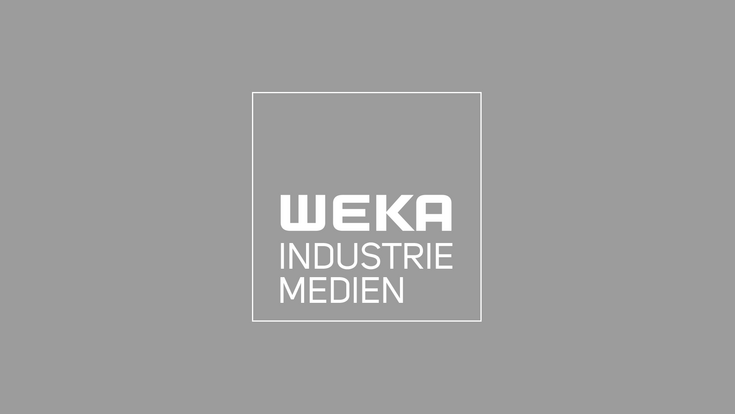
Man stelle sich vor, Satellitenstrukturen könnten direkt im All per 3D-Druckprozess hergestellt werden. Heute werden ja alle Raumschiffe auf der Erde entwickelt, getestet und montiert und per Trägerrakete zu ihren jeweiligen Einsatzorten transportiert. Jede Komponente muss so ausgelegt sein, dass sie den hohen Belastungen der Startphase standhält – was in den meisten Fällen zu einer übergroßen Struktur führt. Hinzu kommen natürlich enorme Kosten infolge der hohen Massen und Volumina und der komplexen Testverfahren, die für den Transport mit der Trägerrakete erforderlich sind.
Ein möglicher Ansatz zur Vermeidung dieser Kosten und Anstrengungen ist die Herstellung von Raumfahrzeugkomponenten direkt in der Umlaufbahn unter Verwendung generativer Herstellungsverfahren. Diese Technologie, die als In-Situ-Fertigung bekannt ist, ermöglicht die Erstellung von Komponenten, die eher auf die Missionsanforderungen als auf die Startanforderungen zugeschnitten sind. Neben der Senkung der Startkosten spart die reduzierte Masse des Raumfahrzeugs Ressourcen und kann die Lebensdauer der Mission verlängern.
Forschung im Parabelflug
Um das Potenzial zu untersuchen, hat die europäische Weltraumbehörde ESA die Kampagne „AIMIS-FYT“ (Additive Manufacturing In Space – Fly Your Thesis 2020!) ins Leben gerufen. Um die Kampagne beworben haben sich acht Studenten der Hochschule für angewandte Wissenschaften München. Ihr Auftrag: Experimente zur additiven Fertigung im Weltall bei Mikrogravitation durchzuführen. Im November und Dezember 2020 ging es für die acht zwar nicht ins All, jedoch an Bord einer Verkehrsmaschine – und in Richtung der gefürchteten Parabelflüge.
Dabei geht ein Flugzeug wiederholt in einen steilen Steigflug und kippt dann relativ abrupt in einen Sinkflug ab. Das Ergebnis ist eine Flugbahn, die von außen betrachtet wie eine Linie steiler Wellen aussieht. Auf den Wellenbergen, also immer im Moment des Überganges vom Steigflug in den Sinkflug, kommt es dann zu einer Neutralisierung der Erdanziehungskräfte, also Mikrogravitation, ganz ähnlich jener im Weltraum. Dies sind die idealen Bedingungen, um das Druckverfahren zu testen.
Die Basis für das Team war der Flughafen Paderborn. Von hier aus ging es dann immer wieder Richtung Frankreich, um über dem Atlantik die Parabelflüge durchzuführen.
Druckvorgänge im Vorfeld abgeleitet
Das Team hat einen 3D-Drucker mit einem Extruder konstruiert, durch den ein flüssiges Photopolymer abgegeben werden kann. Anstatt wie bei herkömmlichen 3D-Druckern Komponenten Schicht für Schicht zu erstellen, werden die Komponenten direkt über die dreidimensionale Bewegung des Druckkopfs erstellt und durch Anwendung von UV-Licht innerhalb kurzer Zeit ausgehärtet. So kommen die Einflüsse praktisch nicht vorhandener Erdanziehungskräfte nicht zum Tragen.
Mit der erfolgreichen Auswahl für das „Fly Your Thesis!“-Programm hatte das Team die Möglichkeit, Experimente durchzuführen und diesen Druckprozess unter Schwerelosigkeitsbedingungen zu validieren. Zu diesem Zweck wurden vier grundlegende 3D-Druckvorgänge aus dem allgemeinen Prozess abgeleitet. Diese Operationen bildeten die Grundlage der Experimente, die während der Kampagne untersucht wurden. Um einen stabilen Druckprozess zu gewährleisten, muss der Extrusionsprozess detailliert analysiert werden. Um dieses Ziel zu erreichen, sind sowohl der Einfluss der Druckparameter auf den Prozess als auch der Einfluss der Mikrogravitation von Bedeutung.
Mission accomplished
Die Ergebnisse können sich sehen lassen. Das Hauptziel der Technologiedemonstration des 3D-Druckverfahrens ist eindeutig erreicht worden. In der Schwerelosigkeit hat das Team erfolgreich verschiedene Arten von Stäben bzw. Druckverfahren getestet. Am Ende jeder Parabelsequenz lag ein ausgehärteter Stab vor, der Druck in der Schwerelosigkeit ist also gelungen.
„Dass sich auch kleinere Fachwerkstrukturen unter Schwerelosigkeit drucken ließen und dass diese anschließend sicher verstaut wurden, untermauert den Erfolg – genau wie eine ausführlichere mechanische Analyse im Nachgang“, sagt Torben Schäfer, Team AIMIS-FYT.
Im Rahmen des Versuchsaufbaus stießen die Studierenden auf RS Components und fragten (erfolgreich), ob der Distributor sie im Rahmen eines Sponsorings mit Bauteilen für das Projekt unterstützen könne. Es handelte sich um eine bunte Zusammenstellung von Signalsäulen über Umschalter, Nutensteine bis zu Steckverbindern.