Leonhard Muigg : Fertigungssteuerung: Warum sich hier mit Excel nicht optimieren lässt
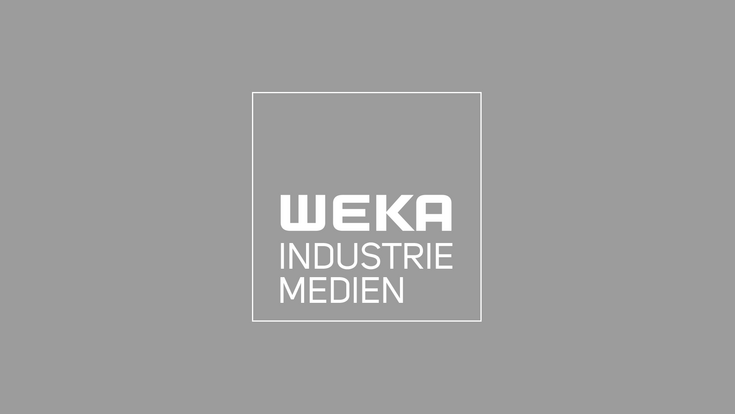
Lassen Sie mich mit einem Szenario beginnen. Als Zulieferbetrieb bekommen Sie am Ende des Geschäftsjahres von der Einkaufsabteilung ihres Hauptkunden einen Brief mit folgendem Inhalt: Im Zuge eines Kosteneinsparungsprogrammes bitten wir Sie, uns bei Ihren Produkten mit einer Preisminimierung von 3 bis 5 Prozent für das nächste Geschäftsjahr entgegenzukommen. Bekannt oder? Will man seinen Hauptkunden nicht verärgern, versucht man diesem Wunsch natürlich nachzukommen. Daraus resultiert die Überlegung, ob sich vielleicht die eigenen Kosten für Material oder Personal „drehen“ lassen, ohne das eigene Margenziel zu vernachlässigen. Zweifelsfrei kommt irgendwann der Punkt, an dem es schwierig oder gar unmöglich wird, diesen Forderungen nach Preisnachlässen nachzukommen. Hinzu kommt, dass man auch globalen Trends wie der Individualisierung, der Veränderung hin zu Losgröße Eins und erhöhter Produktkomplexität gerecht werden muss. Ein Teufelskreis? Sicherlich. An dieser Stelle finde ich das Zitat eines Kunden von Siemens sehr passend. Auf die Frage was heute die größte Herausforderung eines Auftragsfertigers ist, kam die Antwort: „Sehen sie, als Zulieferer müssen wir unsere Leistungen immer 20 Prozent günstiger anbieten können als der OEM selbst, dabei müssen wir für unser Unternehmen ein Margenziel von mindestens 10 % sicherstellen.“
Zweifel am Begriff Prozesskosten
Dass das mit Kosteneinsparungsprogrammen auf Material und Personal nicht mehr erreicht werden kann, ist klar. Dafür müssten sich die Verantwortlichen schon sehr genau mit den Prozessen und Abläufen auseinandersetzen. Wobei nicht nur Technologie und Ablaufplanung zu betrachten sind, auch die Transparenz für Prozesskosten steht hier am Prüfstand. Wer fragt, wie Produktkosten ermittelt werden, bekommt sehr oft zur Antwort, dass alles auf Material- und Prozesskosten errechnet wird. Ich stelle hier den Begriff „Prozesskosten“ ganz groß in Frage. Denn ich bin nicht überzeugt, dass eine Prozesskostenabbildung mit Zuschlägen, Umlagen usw. die echten Prozesskosten abbildet. Hinzukommt, dass diese Kalkulationstabellen fast nie aktuell sind.
Statische Planungswerkzeuge reichen nicht mehr aus
Diese Pufferpositionen werden sich künftig nicht mehr in die Produktkosten einrechnen lassen, ohne dass man genau weiß, wo sich die Wirtschaftlichkeitsgrenze beim Produkt und der Herstellung befindet. Diese Grenze ist dynamisch, da sich etwa Rüst- und Zwischenlagerungszeiten auch auf die Produktionskosten auswirken können. Zu stark abstrahiert? Vielleicht. Trotzdem eine zunehmende Dynamisierung der Fertigung verursacht dynamische Kosten. Um weiterhin Herr über diese Kosten zu sein, reichen Planungswerkzeuge mit statischem Charakter (wie z. B. Excel) nicht mehr aus. Für die Kosten- und Prozesskontrolle sowie Fertigungssteuerung braucht es künftig Rückmeldungen in Echtzeit. Nur so wird man sich künftig wirtschaftlich kompetitiv am Markt behaupten können.
Logistik macht es uns vor
Eine neue planerische Herausforderung für den Mittelstand. Deshalb beschreibt der Digital Enterprise Ansatz von Siemens einen dritten Zwilling, der als der „Digitale Performance Zwilling“ bezeichnet wird. Dieser Zwilling beschreibt die Lösungsansätze für die Datensammlung und -interpretation. Wie kann man also die Dynamik bereits in der Planung beherrschen? Die Logistik macht es uns schon seit Jahren vor. Dort ist die Simulation dynamischer Systeme ein Schlüssel zum Erfolg. Geht es etwa darum die Simulation von Materialflüssen oder Wertströmen in die Planung miteinzubeziehen, werden auch bestehende Prozesse in Frage gestellt und verändert. Die Simulation liefert schon zu einem sehr frühen Zeitpunkt Antworten auf das Einsparungs- und Optimierungspotenzial.