Predictive Maintenance : „Es reicht nicht, ein paar Sensoren einzubauen“
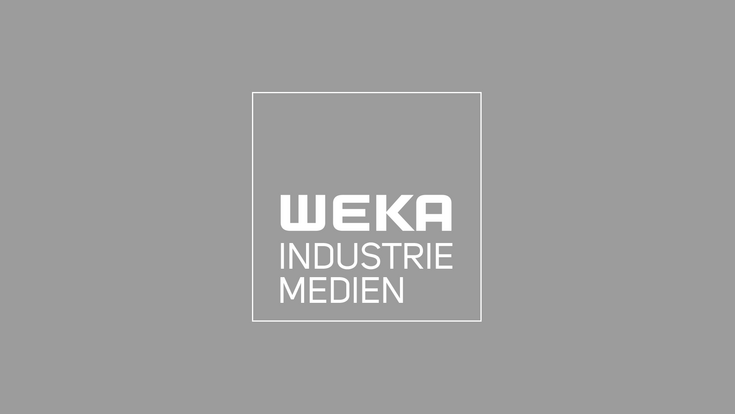
FACTORY: Herr Biedermann, Predictive Maintenance scheint derzeit einen Hype zu erleben, obwohl der Begriff sehr unterschiedlich verwendet wird. Muss man das Thema wieder ein wenig einhegen?
Hubert Biedermann: Es gibt eine Art Heilserwartung, die Hoffnung, dass sich dank Predictive Maintenance demnächst alle Anlagen rechtzeitig melden werden, bevor irgendeine Störung auftaucht. Tatsächlich umfasst der Begriff die unterschiedlichsten Methoden, und das Thema ist weder einfach zu fassen noch zu managen, auch wenn oft anderes vermittelt wird.
Am erfolgreichsten sind in meinen Augen immer jene Unternehmen, die hier Schritt für Schritt vorgehen. Die klein beginnen – und die vor allem bei Anlagen mit Verschleißteilen beginnen. Denken Sie etwa an einen Kran, ein Paradebeispiel für Predictive Maintenance: Wechselnd belastete, instationäre Anlagen mit vielen Verschleißteilen haben die höchsten Instandhaltungs-Kosten. Zudem kann man dort, wo es immer wieder gleichförmige Belastungen gibt, auf der Basis historischen Daten lernen.
Wird das Thema zu hoch gehängt? Sie sprechen von Kranen – viele sprechen gleich von Industrie 4.0.
Biedermann: Die extrem hohe Erwartungshaltung in manchen Unternehmen ist tatsächlich ein Problem – hinsichtlich der Prognosegüte, der Wirtschaftlichkeit und der Schnelligkeit der Zielerreichung. Wenn dann die Menschen vor Ort, die die Idee umsetzen sollen, etwa die mangelnde Datenbasis ins Treffen führen, ist die Ernüchterung manchmal recht groß. Die Unternehmen verfügen oft über Unmengen an Daten, aber unstrukturiert, nicht harmonisiert, ohne einheitlichen Zeitstempel. Es bedarf sehr viel Vorbereitungszeit, um gut in ein Projekt zu gehen.
Wie nähert man sich dem Thema also?
Biedermann: Wir fragen bei unseren Projekten zu Beginn immer: Was erwartet der Kunde eigentlich von Predictive Maintenance? Wo liegt das Problem des Kunden? Und woran würde er den Erfolg festmachen? Wir beginnen also mit den klassischen KPI.
Der zweite Schritt ist ein eingehendes Datenqualitäts-Assessment. Und hier folgt oft die große Ernüchterung. Viele Unternehmen haben jahrelang Instandhaltungsdaten im SAP abgelegt, aber noch nie ausgewertet. Nicht einmal retrospektiv.
Was viele in diesem Zusammenhang übersehen: Je komplexer die Betriebssituation ist, desto mehr unterschiedliche Daten benötigt man. Neben belastungsbezogenen Parametern wie Dichte oder Vibration sind dann auch die Prozessparameter entscheidend. Natürlich machen Machine Learning und KI deren Verarbeitung immer einfacher, aber bis dorthin bedarf es vieler Schritte. Es reicht nicht, ein paar Sensoren einzubauen. Und es reicht erst recht nicht, ein paar Statistiker hinzuzuziehen.
Wie meinen Sie das?
Biedermann: Vor ein paar Jahren haben Konzerne begonnen, Statistiker einzustellen. Die sollten die Maschinen- und Anlagendaten auswerten und dann Antworten liefern. Aber so funktioniert das nicht. Ohne Domain-Wissen kommen Sie hier nicht weit.
Wird die Bedeutung von Domain-Wissen unterschätzt?
Biedermann: In erschreckendem Ausmaß. Weil sich viele Unternehmen zu wenig Gedanken darüber machen, ob der Betrieb und die Weiterentwicklung einer Anlage einen Wettbewerbsvorteil darstellen oder nicht.
Nehmen Sie zum Beispiel einen Flughafenbetreiber, der ein Förderband für Gepäck will. Oder ein Pharmaunternehmen, das ein Hochregallager benötigt. In beiden Fällen will der Auftraggeber Wartungen und Inspektionen nicht selbst übernehmen. Er will nur wissen, was ihn Investition und Betrieb kosten werden. Wenn der Lieferant klug ist, liefert er nicht nur eine Zuverlässigkeits-gerechte Konstruktion, sondern überlegt sich gleich auch ein Predictive-Maintenance-Paket. Denn er ist ja in der Betreiber-Phase für Zuverlässigkeit und Verfügbarkeit verantwortlich. So wird der Anlagenbau dazu gezwungen, an After Sales Services zu denken.
Ein Stahlproduzent, der seine Wettbewerbsvorteile unmittelbar aus dem Betrieb der Anlagen zieht, muss das Domain-Wissen natürlich selbst aufbauen. Dieses Wissen braucht man immer – die Frage ist nur, wo es verortet ist.
In welchen Branchen sehen Sie Predictive Maintenance denn am weitesten fortgeschritten?
Biedermann: Überall dort, wo es nicht um Pilotanlagen geht, sondern um hundert- oder tausendfach duplizierbare Anlagen. Also etwa bei Automotive, der Eisenbahn- und Luftfahrtindustrie oder im Bereich der Energieerzeugung. Die überhöhte Erwartungshaltung kommt eher aus der Prozessindustrie, wo wir es aber mit Pilotanlagen zu tun haben und nicht mit duplizierbaren Anlagen.
Ich will hier aber nicht missverstanden werden: Predictive Maintenance ist in meinen Augen sehr zukunftsträchtig, aber je mehr Technologie in einer Anlage steckt und je stärker wir mit Steuerungstechnologien arbeiten – wo sich Fehler ja überhaupt nicht vorhersagen lassen –, und je weniger mechanische Komponenten in der Anlage stecken, desto differenzierter müssen die Vorgangsweise und die Strategiewahl der Instandhaltung aussehen. Eine Kritikalitätsbewertung der Anlage mit strukturierter Schwachstellenanalyse ist hier zielführend.
Sie haben die Datenqualität angesprochen. Ist die vor allem bei KMU ein Problem?
Biedermann: Aber nein, selbst bei Projekten, die wir mit Konzernen durchführen, gehen bis zu 60 oder 70 Prozent der Zeit dafür drauf, überhaupt einmal die Datenbasis zu schaffen. Und dann sind wir noch lange nicht im Modell, im Algorithmus. Daher plädiere ich immer dafür, mit Pilotprojekten zu beginnen, mit Little Data. Und mit vorsichtiger Erwartungshaltung.
Wie gehen denn Ihrer Erfahrung nach die Instandhalter selbst mit dem Thema Predictive Maintenance um? Stößt man damit auf Begeisterung?
Biedermann: Ich denke, die Antwort kennen Sie. Die Begeisterung ist oft enden wollend. Tatsächlich haben viele Angst davor, wegrationalisiert zu werden. Und manche Unternehmen machen ja auch den Fehler zu behaupten, Predictive Maintenance werde die Instandhalter letztlich einsparen.
Dabei geht es doch um etwas ganz anderes: Wenn man es schafft, in der Anlage eingebaute Schwachstellen zu identifizieren und zu beheben, wird die Anlage unter dem Strich besser. Und bessere, zuverlässigere Anlagen mit weniger Prozessparameter-Streuung erzeugen höhenwertige Produkte. Man kann das Produkt billiger herstellen, weil man weniger Ausschuss produziert. Ich höre immer wieder: Predictive Maintenance soll uns helfen, Kosten einzusparen. Natürlich denkt da jeder sofort an Personalkosten.
Und wie reagieren Sie dann?
Biedermann: Dann sage ich, sorry, macht es mit jemand anderem.
Zur Person
Professor Hubert Biedermann ist Vorstand des Instituts für Wirtschafts- und Betriebswissenschaften an der Montanuniversität Leoben und Präsident der Österreichischen Vereinigung für Instandhaltung und Anlagenwirtschaft (ÖVIA).