Thema des Monats : Die KVP-Millionen-Show
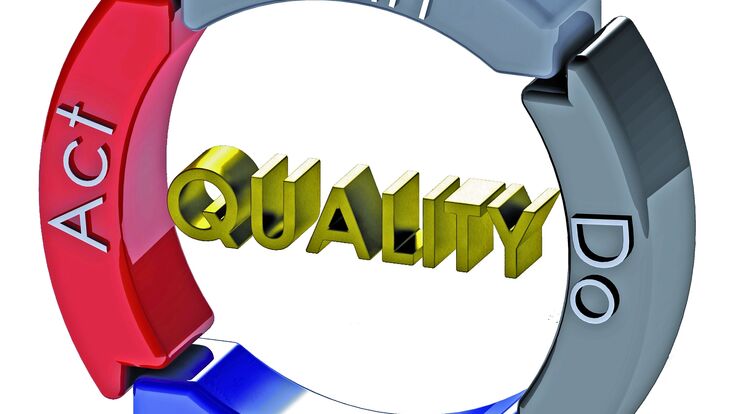
Im Rahmen unserer Recherchen zum Thema des Monats herrschte beim Stichwort KVP das ein oder andere Mal durchaus etwas so wie die babylonische Sprachverwirrung. Nicht nur, dass Unternehmen ihre eigenen Bezeichnungen kreieren. Auch die Herangehensweise ist äußerst unterschiedlich. Während bei GM Powertrain das betriebliche Vorschlagswesen quasi institutionalisiert ist, gehen kleinere Betriebe oft sehr informell – aber keineswegs schlechter – mit dem Thema um.Seit über 27 Jahren gehört das „betriebliche Vorschlagswesen“ bei GM Powertrain Austria zum guten Ton. Wie stark sich das im allgemeinen Gebrauch als kontinuierlicher Verbesserungsprozess – kurz KVP – genannte Managementwerkzeug im Werk in Wien Aspern etabliert hat, zeigt eine Statistik, die anlässlich des 25-jährigen Jubiläums des Vorschlagswesens im Jahr 2008 dazu veröffentlicht wurde. Seit der Einführung 1983 wurden bis dahin rund 276.000 Verbesserungsinitiativen eingereicht, die gesamt zu Einsparungen von rund 63,4 Millionen Euro und Mitarbeiterprämien von rund 11,9 Millionen Euro führten. Die höchste Einsparung wurde im Jahre 1991 erzielt: Johann Doll, Werner Schalk und Herbert Sporr sparten dem Unternehmen 2 Millionen Euro für Verbesserungen bei der Motorenprüfung ein. YIP-iiieeeey.
Bei Infineon in Villach hat man für Ideen die sich sowohl für das Unternehmen als auch für die Mitarbeiter lohnen, den Slogan „Your ideas pay“ (YIP) kreiert. Dementsprechend wird die Einreichung einer Idee bei Infineon Technologies als „Yip“ bezeichnet. Nach der hausinternen Definition lässt ein sinnvoller YIP erkennen, a) was verbessert werden soll, b) wie es verbessert werden soll und c) dass seine Verwirklichung für die Kunden sowie für das Unternehmen und/oder die Mitarbeiter eine Verbesserung bedeuten kann. Im Durchschnitt wurde aus Österreich heraus in den letzten Jahren ein Nutzen von rund 20 Millionen Euro pro Jahr für das Unternehmen errechnet. Im schwersten Jahr der Wirtschaftskrise, 2009, wurden immerhin noch „Yips“ im Wert von rund 10 Millionen Euro aus Österreich lukriert. „Die Fähigkeit, Anlagen und Prozesse zu verbessern, ist ein entscheidender Wettbewerbsvorteil unseres Standortes. Das Ideenmanagement unterstützt diese Aktivitäten auf besondere Weise und stellt sicher, dass unsere Mitarbeiter auch am Erfolg ihrer herausragenden Leistungen beteiligt werden“, erläutert dazu Monika Kircher-Kohl, CEO Infineon Technologies Austria AG. Mit Rübig nach RIO.
Der Härtetechnik-Spezialist Rübig aus Wels setzt in seinem Haus auf RIO („Rübig – Ideen für Optimierung“). Im Zentrum stehen zum einen die Kosteneinsparung und zum anderen die Sicherheit der Mitarbeiter im Unternehmen. Besonders wichtig sind, so Qualitätsmanager Roland Glück, „die dauerhafte Erhaltung des Einsparungspotenzials und, dass neue Mitarbeiter nicht dieselben Fehler machen, die schon einmal aufgetreten sind“. Rübig profitiert nachhaltig von den Ideen – und die Abteilung des Mitarbeiters, der den Vorschlag zu Verbesserung entwickelt hat, von einer Prämie. Glück: „Die in einem konkreten Fall erreichte Einsparung von 40.000 Euro pro Jahr ist ein nachhaltiger Erfolg einer Idee eines Mitarbeiters. Uns sind aber jederzeit auch Vorschläge willkommen, die ,nur‘ ein paar 100 Euro ausmachen.“ Das ABC des KVP.
Der mit Standorten in Klagenfurt, Villach und Wolfsberg ansässige Auftragsfertiger für den Sondermaschinenbau, ABC Service & Produktion GmbH, fertigt mit 220 Mitarbeitern Präzisionsdreh- und Präzisionsfrästeile aus Metall, Kunststoff und Hochleistungskeramiken sowie mechatronische Baugruppen und Sondermaschinen. KVP wurde 1994 eingeführt und wird von der Unternehmensleitung massiv gefördert. „Es ist für den wirtschaftlichen Erfolg eines Unternehmens ganz entscheidend, die guten Ideen seiner Mitarbeiter abzuholen“, erläutert GF Thomas Höbart die Vorgangsweise. „Wir nutzen in diesem Bereich verschiedene Werkzeuge, eines davon ist unsere „Ideenbörse“. Die rund 15 bis 20 Vorschläge pro Monat werden durch eine interdisziplinär besetzte Jury bewertet und gegebenenfalls prämiert. Höbart: „Die Bewertung erfolgt möglichst analytisch und transparent durch die Errechnung eines Jahres-Nettonutzens – das ist jener monetäre Nutzen, den der Vorschlag innerhalb von 12 Monaten unter Abzug der Realisierungskosten einbringt. Der Ideeneigentümer wird in die Realisierung des Vorschlages mit eingebunden.“ Der Jahressieger wird aus einer Rankingliste ermittelt und zusätzlich zur Prämie mit einer Flugreise belohnt. Technischer Korrekturvorschlag.
Beim Schaltschrankbauer Schinko hat das Vorschlagswesen den etwas sperrigen Titel „Technischer Korrekturvorschlag“. „Wir haben einen klar definierten Ablauf, wie zum Beispiel Vorschläge von der Produktion in die Konstruktion einfließen“, sagt GF Gerhard Lengauer. „Dieser ist seit vielen Jahren bei uns implementiert und deckt einen Großteil unseres Verbesserungswesens ab.“ Die Umsetzung erfolgt oft auch in Absprache mit den Kunden. „Das geht dann sehr rasch und beinhaltet durchaus auch konstruktive Änderungen eines Produktes, die sich auch als wirtschaftlicher Vorteil für unsere Kunden erweisen.“Gesorgt wird bei Schinko auch für die Rückmeldung an die Mitarbeiter, die Vorschläge eingereicht haben. Im Gegensatz zu vielen anderen gibt es bei Schinko für Vorschläge aber keine Prämien. Lengauer: „Ich kenne beide Systeme. Meine Erfahrung hat gezeigt, dass das System in Unternehmen, die keine Prämien ausschütten, länger und besser lebt.“ Schlank sein macht stark.
battenfeld-cincinnati erkannte bereits vor einigen Jahren, dass sich sowohl die internen Anforderungen als auch die der Kunden rapide verändern. „Qualität alleine genügte nicht mehr, es galt, Topqualität in möglichst kurzer Zeit zu liefern. Um sich für diese neuen Herausforderungen zu wappnen, wurde Ende 2007 beschlossen, das Lean-Six- Sigma-Konzept im gesamten Unternehmensverbund in die Unternehmensphilosophie aufzunehmen“, erläutert Christoph Steger, Director Market & Technologies. „Innerhalb der letzten drei Jahre konnten viele Prozesse durch Lean-Six-Sigma-Projekte nachhaltig verbessert werden: Durchlaufzeiten wurden verkürzt, Fehlerquellen beseitigt und Abläufe vereinfacht.“
›› ABC Service & Produktion GmbH
2007 wurde ein Mitarbeiter-Vorschlag zum Thema „Mitarbeiter-Gesundheit“ eingebracht. Aus diesem Vorschlag entstand ein Gesundheitsprojekt mit den Schwerpunkten Ernährung, Bewegung, Erholung. Zu allen drei Schwerpunktthemen gab es Informationsveranstaltungen mit externen Spezialisten, an denen alle Mitarbeiter teilgenommen haben. Aufgrund der gesellschaftlichen Entwicklung (Überalterung) ist es auch für Unternehmen von immer größerer Bedeutung die Leistungsfähigkeit seiner Mitarbeiter positiv zu beeinflussen. Aus diesem Projekt heraus entstand auch ein jährlicher Gesundheitscheck, der unter Mithilfe der Betriebsärztin allen Mitarbeitern angeboten wird.
›› battenfeld-cincinnati
die Lean Six Sigma Philosophie wird vom gesamten Unternehmen gelebt. Ein Beispiel: In der Vergangenheit mussten einzelne steuerungstechnische Regelparameter bei jeder auszuliefernden Maschine langwierig durch individuelle Einstellprozesse definiert werden. Dies kostete Zeit und war fehleranfällig. Auf Initiative eines Mitarbeiters aus der Endkontrolle wurde eine webbasierte Applikation entwickelt, die es ermöglichte, die Regelparameter systematisch zu erfassen, zu archivieren und zu aktualisieren. Dadurch wurden die individuellen Einstellungsprozesse obsolet, was zu einer drastischen Reduzierung der Durchlaufzeit gepaart mit einer Erhöhung der Qualität führte.
›› Bosch
BVW – das „Betriebliche Vorschlagswesen“ wurde 1924 vom Firmengründer Robert Bosch im Unternehmen etabliert. Beim BVW geht die Initiative vom Mitarbeiter selbst aus. Er erkennt einen verbesserungswürdigen Zustand und entwickelt Lösungen zur Verbesserung. Für den Fall, dass die Idee umgesetzt wird, erhält der Mitarbeiter eine Vergütung, die sich am Nutzen seines Vorschlages orientiert. Die jährlich mehrere Millionen Euro betragende Ausschüttung an Prämien zeigt, dass sich Mitdenken durchaus lohnt. Anfang der 90iger Jahre wurde bei Bosch der Continuous Improvement Process (CIP) eingeführt. Da die Führungskräfte aller Ebenen für den CIP-Prozess verantwortlich sind, spricht man von geführter „Ideengenerierung“. CIP ist stark ausgeprägt im direkten Bereich (Fertigung), wird aber auch in allen anderen Funktionen im indirekten Bereich (Verwaltung, Vertrieb, Entwicklung) angewendet. Häufig wird hierfür eine moderierte Gruppenarbeit verwendet, bei der zu einem vorgegebenen Thema („geführt“), Ideen und Vorschläge zur Verbesserung von den Mitarbeitern identifiziert und diskutiert werden.
›› Fronius
Bei Fronius wurden bisher die Gasschläuche für die Schweißgeräte erst nach der Geräteprüfung der Verpackung beigelegt – was einige Male im Jahr vergessen wurde. Dies passiert künftig nicht mehr: Fronius hat quasi den Gasschlauch in den Produktionsprozess der Geräte integriert. Er wird jetzt in der Fertigungslinie montiert; bei der Endprüfung des Gerätes wird mit diesem Gasschlauch geprüft und nicht mehr mit einem Prüfgasschlauch. Ein fehlender Schlauch fällt so sofort auf (Poka-Yoke-Lösung, siehe Kasten). Seit dieser Umstellung – die keinen Euro gekostet hat – gab es keine Reklamation mehr.
›› GM Powertrain
Zwei pneumatische Roboter hatten bei GM die Aufgabe, die Gangräder für den 4. und 5. Gang nach dem Entgraten vom Band zu nehmen und in die richtige Position zu bringen, damit sie weiter zu einer Waschmaschine transportiert werden konnten. Die Roboter erwiesen sich aber als störungsanfällig und wartungsintensiv. Dann hatten Gerd Puchecker, Robert Kronsteiner, Hubert Tiefengrabner, Markus Rechberger und Thomas Klien von der Fünfgang-Getriebefertigung eine Idee: Eine einfache mechanische Umlenkung dreht seither die Gangräder in die richtige Lage und befördert sie so in die Waschmaschine. Die Roboter wurden arbeitslos, die Einsparungen für Strom, Ersatzteile, Wartungen und Reparaturen ergaben eine Summe von 24.164 Euro pro Jahr.
›› Infineon
Die Bandbreite der Wertigkeit der Ideen zur Verbesserung von Prozessen, Produkten etcetera ist sehr groß. Erfahrungsgemäß sind vor allem Verbesserungsideen im Fertigungsbereich diejenigen, die den höchsten wirtschaftlichen Nutzen für das Unternehmen erzielen. Natürlich nicht alltäglich, aber zur Veranschaulichung, wie hoch der Nutzen einer Idee sein kann: In Villach wurde ein spezieller „Yip“ mit einem Einsparungspotenzial von mehr als 800.000 Euro bewertet.
›› Miba Frictec
Reiblamellen für Kupplungen und Bremsen produziert Miba Frictec. Die Fiber Composite Lamellen bestehen aus einem Stahlträger, Klebstoff und dem organischen Fiber Composite Reibbelag. Um die Lamellen auszuhärten, kommen sie in eine Heizpresse. Diese verfügt über vier Presszellen, in der je eine Lamelle einem bestimmten Druck ausgesetzt ist. Pro Presszelle wurde bisher eine Lamelle eingelegt. Die Adapter der Presse wurden nun so modifiziert, dass pro Presszelle vier Lamellen gleichzeitig eingelegt werden können. Dies spart rund 42.000 Euro im Jahr – und beträchtlich Zeit.
›› Rübig
Wärmebehandlungs-Dienstleister Rübig hat mit seiner Strategie RIO („Rübig – Ideen für Optimierung“) kürzlich ein besonders profitables Projekt umsetzen können. Für Rübig ist in der Regel der Freitag ein intensiver Wochentag. Die Warenannahme ist voll ausgelastet, da viele Kunden noch vor dem Wochenende anliefern wollen. Eine organisatorische Maßnahme brachte hier Entspannung: kleine Veränderungen von Tätigkeitsbereich sowie Stundeneinteilung führten zu einer deutlichen Verbesserung der Durchlaufzeiten und zu einer Einsparung von 40.000 Euro pro Jahr, da nun viel weniger Überstunden anfallen.
›› Schinko
Ein Beispiel wie man bei Schinko Verbesserungen betreibt bezieht sich auf ein Gehäuse für ein medizinisch-technisches Laborgerät, das vielfältigste Umformen brauchte. Diese waren zu Beginn nur mit größten Problemen durchzuführen und verursachten eine hohe Ausschussquote. „Ein Mitarbeiter kam mit einem Verbesserungsvorschlag bezüglich der Verwendung eines anderen Materials für das Gehäuse“, erzählt Schinko GF Gerhard Lengauer. „Damit haben wir den Ausschuss faktisch eliminiert, aber auch gleichzeitig die Fertigungszeiten deutlich reduziert und somit unser Produktionsziel erreicht.“
›› Siemens SIMEA
Andrew Callahan hat als Leiter der Produktion von Large Drives-Einheiten im SIMEA Werk in Wien die Einführung des Siemens Production Systems (SPS) mitgestaltet. Die Philosophie dahinter orientiert sich am Lean Manufacturing. „Wichtig ist die Einbindung der Mitarbeiter “, sagt Callahan. „80 Prozent eines Projektes werden von den Teams sehr rasch umgesetzt, die restlichen 20 Prozent kommen in die KVP-Schleife und werden in einem zweiten Durchgang erledigt.“ Wie gut das funktioniert präzisiert der gebürtige Amerikaner an einem Beispiel: „Im Bereich Traktion - Antriebstechnik für Bahn und U-Bahn - konnte durch die SPS-Methodik die Durchlaufzeit um 50 Prozent verbessert werden. Außerdem haben wir die Fertigungsflächen um ein Drittel reduziert und die Arbeitsplätze standardisiert. Diese Änderungen geschahen auf Anregung der Mitarbeiter.“
›› technosert
Beim Elektronik-Spezialisten technosert ist KVP Standard. „Gute Ideen bringen Erfolg“, so Geschäftsführer Johannes Gschwandtner. Die Vorschläge der Mitarbeiter werden in die Qualitätssicherungssoftware aufgenommen; jene, die umgesetzt wurden, auf Wirksamkeit geprüft. Zu einer beachtenswerten Verbesserung führte die Idee, flexible Rahmen für die Selektivlötwelle zu bauen, anstatt sie für jeden Auftrag individuell zu fertigen. Mit diesen Rahmen können Greifer die Leiterplatten besser aufnehmen. Die Kosten- und Zeitersparnis ist hoch: Jetzt können mit zehn Adaptern alle Bauteile optimal gehandhabt werden.
›› Trumpf
KVP ist eine Führungsaufgabe – wenn sich niemand darum kümmert, dann ver-kümmert es“, meint Thomas Saiko, Werksleiter von Trumpf in Pasching. Es muss zuerst ein Produktionssystem oder Produkt geschaffen werden, das grundsätzlich funktioniert. Dieses kann dann laufend verbessert werden. Das Beispiel von Trumpf zeigt, dass auch Kunden den Anstoß zu guten Ideen der Mitarbeiter geben können. Ein Anwender stellte nämlich fest, dass bei der Abkantpresse TruBend 7036 nicht alle Anschlagpositionen für ein zu biegendes Blech gut erkennbar waren. Ein Trumpf-Mitarbeiter griff dies auf; die Lösung fand sich in Form einer CNC-schwenkbaren iLED-Leuchte. Der Vorschlag bewährte sich – jetzt werden alle TruBend 7036 mit der automatisch schwenkbaren iLED ausgerüstet.
›› vatron gmbh
Die Entwicklung, Produktion und Inbetriebnahme von mechatronischen Mess- und Regeleinrichtungen für Industrie-Anlagen ist das Geschäft von vatron (eine Tochter der voestalpine und Siemens VAI). Vor der Eröffnung des neuen Betriebsgebäudes 2008 waren technische Arbeitsplätze und Büroarbeitsplätze quasi „verschmolzen“. Die bestehende Platz- und Ressourcenproblematik wurde durch ein vollkommen neues Raumkonzept gelöst: Heute gibt es wenige Wände, freie Arbeitsplatzwahl (kabellos mit Laptop und Handy) und eine klare Trennung zwischen Büroarbeitsplatz und Technik. Obwohl Mitarbeiter in die Entscheidungen eingebunden waren gab es vor dem Umzug große Bedenken. Heute, ein Jahr danach, entpuppt sich das Konzept als „Renner“. Kommunikation und Arbeitsprozesse wurden deutlich verbessert und werden von allen Mitarbeitern als sehr gut eingestuft.
Poka Yoke
Das Poka-Yoke-Prinzip (aus dem japanischen, bedeutet etwa „unglückliche Fehler vermeiden“) deckt durch bestimmte technische Maßnahmen Fehler auf und verhindert diese. Das KVP-Beispiel von Fronius funktioniert nach diesem Prinzip. Der Gasschlauch eines Schweißgerätes wird zur Geräteprüfung benötigt. Folglich kann kein geprüftes Schweißgerät ohne Schlauch ausgeliefert werden. Ein bekanntes Beispiel sind SIM-Karten, die sich auf Grund ihrer Form nur korrekt in den Slot einlegen lassen. Kaizen
Die aus Japan stammende Lebens- und Arbeitsphilosophie Kaizen („Veränderung zum Besseren“) ist dem vom US-Amerikaner William Edwards Deming entwickelten KVP praktisch gleichzusetzen. Kaizen zielt auf eine Verbesserung des Gesamtprozesses und nicht ausschließlich des Endprodukts. Explizit fordert diese Philosophie Verbesserungsvorschläge von den Mitarbeitern ein. Dabei stehen drei Faktoren im Vordergrund: Kostensenkung, Qualitätssicherung und Zeiteffizienz. Weit verbreitet ist Kaizen in der Automobilindustrie.