Messtechnologie : Computertomografie: Dreidimensional in die Zukunft
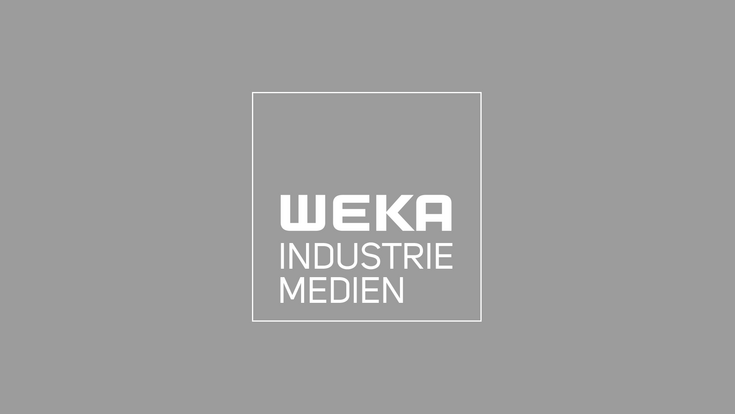
Soll-Ist-Vergleiche zwischen CAD- und tomografisch ermittelten Daten lassen Problemzonen am Bauteil erkennen, ohne spezielle Messpunkte anlegen zu müssen. Sämtliche Abweichungen werden farbkodiert angezeigt und sind schnell zu erkennen. Für die Qualitätssicherung seiner Produkte, geometrische Mess-Aufgaben und Material-Analysen nutzt der Hersteller von hochwertigen Steckverbindern zur Energie-, Signal- und Datenübertragung sowie für Geräte-Anschlusstechnik, Netzwerkkomponenten und Systemkabel.
3D Datenstruktur für die gesamte Prozesskette.
Das Koordinaten-Messgerät mit Computertomografie kommt hauptsächlich zur zerstörungsfreien Konformitäts-Analyse für die Produktionsoptimierung zum Einsatz. Mit der Computertomografie entlasten wir unsere bestehende Messtechnik. Außerdem ist dieses Verfahren mitunter schneller als die herkömmliche Koordinaten-Messtechnik und liefert zusätzliche Informationen. Langfristig werden wir die gesamte Prozesskette auf 3D-Datenstrukturen umstellen. Davon ist auch die Qualitätssicherung betroffen. Mit der Röntgentomografie lassen sich die notwendigen dreidimensionalen Untersuchungen durchführen. In erster Linie jedoch war die Mess-Genauigkeit des Geräts ausschlaggebend für seine Anschaffung. Es muss eine Genauigkeit in der Größenordnung weniger Mikrometer liefern. Damit kann das Unternehmen filigrane Steckverbinder (<1 cm) ebenso messen wie große Gehäuse für Wagen-Übergangskabel, die fast einen halben Meter lang sind.
Geeignet für Mess- und Analyseaufgaben.
Zurzeit wird das Messgerät zu zwei Drittel für Mess- und zu einem Drittel für Analyse-Aufgaben genutzt. „Messen“ bedeutet, dass die Oberflächen von Gehäusen und Steckverbindern erfasst und die zugehörigen Maße (Länge, Radius) bestimmt werden. Mussten zuvor noch Schliffe erstellt werden, an denen dann die Maße der Innenkammern erfasst wurden, lassen sich jetzt Schnittaufnahmen anfertigen, die einem solchen Schliff entsprechen. Das bedeutet einen deutlich geringeren Aufwand. Zudem kann die Schnittebene digital verschoben werden. Wo früher wegen des Aufwands nur eine Schliffebene zur Qualitätssicherung herangezogen wurde, können wir jetzt ohne zusätzlichen Mess-Aufwand in beliebig vielen Ebenen messen. Der einzige Mehraufwand besteht in der anschließenden Verarbeitung der Informationen.
Unter „Analyse“ versteht man im Unternehmen in erster Linie entwicklungsbegleitende Prüfungen, bei denen das Volumen des jeweiligen Teils zerstörungsfrei betrachtet wird. Das Untersuchen von Dichtigkeit und Prüfen des Verlaufs von Vergussmasse sind Beispiele. Mit Hilfe eines CT-Scans und der Analyse kann man feststellen, ob sich das Füllmaterial richtig verteilt hat oder ob sich Lunker im Kunststoff oder Aluguss befinden. Je nach Ergebnis kann man die Werkzeugform oder die Spritzparameter optimieren.
Einfaches Bedienen und Auswerten.
Der Umgang mit dem Messgerät ist einfach. Der Bediener muss keinerlei Justagearbeiten verrichten, sondern kann das Werkstück unmittelbar auf den Drehtisch setzen, der sich zwischen Röntgenquelle und Detektor befindet. Dann wählt er in der Bedienoberfläche der Software Winwerth die gewünschte Vergrößerung und eventuelles Rastern, bei dem Teilbilder des Werkstücks aufgenommen und anschließend zu größeren Volumen zusammengesetzt werden. Das Rastern wird bei länglichen Steckerleisten, die nur wenige Reihen mit einer großen Anzahl Pole haben eingesetzt.
Diese werden senkrecht aufgespannt, Abschnitt für Abschnitt eingescannt und exakt zusammengefügt. Dadurch wirdeine sehr hohe Auflösung und Genauigkeit erreicht. Startet der Bediener den Röntgenvorgang, wird eine zu wählende Anzahl Durchstrahlungsbilder in verschiedenen Drehstellungen aufgenommen. Anschließend erfolgt in der Software eine 3D-Rekonstruktion der Einzelbilder zu einem kompletten 3DVolumen, das die gesamte Werkstückgeometrie innen und außen beschreibt. Das Ergebnis sind Messdaten mit einer Genauigkeit im Mikrometerbereich, die jedes Detail des Werkstücks abbilden und sich in verschiedener Weise auswerten lassen.
Idealer Erstmuster-Prüfbericht.
Ein typisches Einsatzgebiet ist der Erstmuster-Prüfbericht zur Freigabe des Produktes. Dazu liefern die Produktentwickler ein Vorserienmuster mit Zeichnung und CAD-Daten sowie den Prüfbogen. Nach dem Scannen des Bauteils, erfolgt mit den Daten ein Soll-Ist-Vergleich in farbkodierter Darstellung sowie eine Lunker-Analyse. Anschließend werden die Prüfmaße gemessen und das Ergebnis im Erstmuster-Prüfbericht dokumentiert. Die Beurteilung der Maße liegt dann beim Entwickler, der das Teil bei positivem Befund zur Serienfertigung freigibt. Ergänzend zu den Messungen, bei denen exakte Werte ermittelt werden, bietet die Software die Möglichkeit zum erwähnten Soll-Ist-Vergleich, auch farbkodierte Abweichungsdarstellung genannt. Namensgebend für diese Bezeichnung ist die farbige Darstellung der Abweichungen zwischen Soll- und Ist-Geometrie. Zum Hintergrund: Das CAD-Modell wird in die Mess-Software eingelesen und über die tomografisch ermittelten Daten gelegt. Sämtliche Abweichungen werden farbkodiert angezeigt, sodass der Anwender auf einen Blick Einfallstellen oder sonstige Problemzonen erkennen kann, ohne speziell einzumessen. Diese Darstellung kann als Grundlage für die Korrektur des Spritzguss-Werkzeugs dienen. Hilfreich ist diese Methode auch bei der schnellen Prüfung von Gehäusen, die gröber tolerierte Maße wie etwa Radien aufweisen, deren genaues Maß nicht für die Funktion entscheidend ist.
Mess-Technologie macht sich bezahlt.
Der größte Gewinn darin, dass man mit dem neuen Gerät durch das schnelle Messen in verschiedenen Ebenen deutlich mehr Informationen über das gesamte Bauteil erhält. Diese werden zugunsten einer besseren Qualität genutzt.
Weitere Nutzen: Zum Beispiel beim Messen der großen Druckguss-Gehäuse, bei denen die Werkzeuge aus Verschleißgründen relativ oft ersetzt werden müssen. Alle ein bis zwei Jahre kommt dasselbe Gehäuse wieder zur Erstmuster-Prüfung, weil ein neues Werkzeug gebraucht wurde. Wenn dafür einmal das Mess-Programm geschrieben ist, kann es bei Bedarf wieder verwendet werden. was natürlich Zeit spart. Bei den Isolierkörpern aus Kunststoff gibt es noch andere positive Effekte. Für die innenliegenden zahlreichen Kammern müssen Maße und Position erfasst werden. Beim Röntgen lässt sich der Mess-Vorgang komfortabel duplizieren. Außerdem sind die Spritzguss-Werkzeuge häufig mit Vier- oder Achtfach-Nestern ausgeführt, wofür ein Mess-Programm mehrfach verwendet werden kann.