Industrie 4.0 : Banner Batterien hat die schlankste Produktion
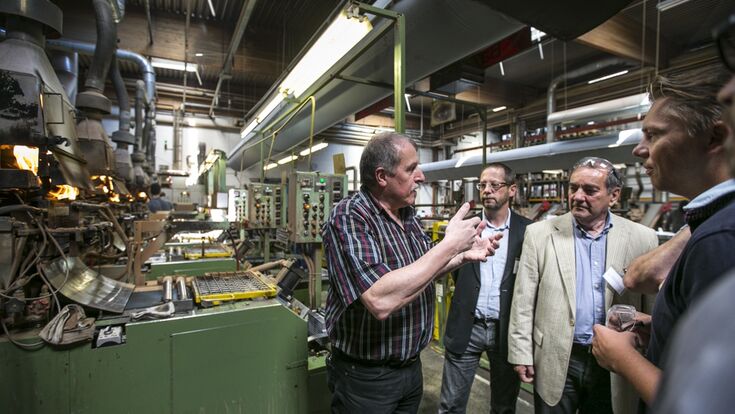
Sein Know-how preiszugeben, davor hatte Franz Dorninger nie Angst. „Unsere Produktionsprozesse sind sehr spezifisch, das verstehen nur wenige“, versichert der technische Direktor bei Banner Batterien. Nur dem direkten Mitbewerb hätte der Linzer seine heiligen Hallen nicht gezeigt. Dennoch Grund genug für dreißig auswärtige Produktionsleiter, der exklusiven Einladung zu folgen, um einmal die Prozesse der Linzer genauer betrachten zu können. Warum dieses Treffen? „Damit über den Tellerrand geschaut wird“, so Dorninger. Denn Banner hat etwas, was viele wollen: Eine funktionierende Lean Production.
Banner ist Österreichs Aushängeschild in der Batterieproduktion und beliefert viele bedeutende Kraftfahrzeughersteller wie Audi, BMW, VW, Porsche oder Mercedes mit Erstausrüstungsbatterien. Der Druck der Automobilisten ist groß. Laufende Produktinnovation gefragt. „Dazu braucht es einen Produktionsprozess, der sich ständig weiter verbessert“, so Dorninger. Die Linzer setzen deshalb seit längerem auf die Methoden der „schlanken Produktion“. „Um dieses Konzept anwenden zu können, braucht es einerseits eine Qualifizierung aller betroffenen Mitarbeiter, vom Anlagenbediener bis hin zum Produktionsmanager“, erklärt Dorninger. „Andererseits braucht es geeignete IT-Tools, die hier strategisch die Mitarbeiter unterstützen.“ Gefunden hat Banner dieses IT-Tool in Graz. Gamed bietet Softwareprodukte zur Optimierung der Prozesse in der Produktion, Instandhaltung, Qualitätssicherung und Disposition. Die Lösungen der Grazer unterstützen seit 1998 die Produktionsprozesse des Batterieherstellers. Und das mit sichtlichem Erfolg: So konnte die Produktivität bereits um mehrere Prozent gesteigert werden. Ein Erfolg, den sich diese dreißig Produktionsleiter genauer anschauen wollten.
Übeltäter entlarvt
Johannes Stimpfl erinnert sich noch gut: „Erster Schritt bei Banner war die Instandhaltungssoftware IPC“, erklärt der Geschäftsführer von Gamed. „IPC unterstützt die Koordinierung und Abwicklung aller Wartungsaufträge, Störungsbehebungen und Verbesserungsmaß- nahmen.“ Auch die Bevorratung und Beschaffung von Ersatzteilen wird mit IPC übersichtlich und effizient organisiert. Dabei sollen Kennzahlentrends mit Leistungsdaten aus der Produktion den Betriebsverantwortlichen bei operativen Optimierungen oder strategischen Änderungen helfen.
2009 kam dann der nächste Schritt bei Banner: Zur gezielten Produktivitätssteigerung der Anlagen wurde der OEE Analyser eingeführt. „Der OEE Analyser misst ohne zusätzlichen Personalaufwand die Leistung der Maschinen und bietet mit seinen zahlreichen Analysen gezielte Optimierungsmaßnahmen“, so Stimpfl. „Verdichtete Managementberichte mit Abweichungsanalysen sind wichtige Entscheidungsgrundlagen für Neuinvestitionen, um teure Überkapazitäten zu vermeiden.“
Dorninger kann das bestätigen, hat er dank dem OEE Analyser einen Übeltäter auf seinen Anlagen entlarvt, der so nie aufgefallen wäre. „Es war ein kleines Gerät, dass die Maschine nur im Minutentakt zum Aus- fall brachte“, erklärt der technische Direktor. „Doch die Summe der Störungen auf das Jahr gerechnet ließ dann sofort den Übeltäter auffliegen.“ Mittlerweile läuft das Gamed-System auf 18 Maschinen und Linien. Soll aber auch die nächsten Jahre die restlichen fünf Linien erobern, denn Dorninger hat einen ganz netten psychologischen Nebeneffekt des OEE Analysers entdeckt. „Seit meine Mitarbeiter sehen, was sie selbst leisten und was ihr Kollege an der anderen Maschine leistet, sind sie motivierter denn je“, erklärt er. Der OEE Analyser unterstützt Maschinenbediener und Schichtführer mit aktuellen Informationen im operativen Be- trieb und bei der Schichtübergabe. Als nächster Schritt ist der Einsatz von Machine Eye geplant. „Machine Eye ist ein Visualisierungssystem, um Zielvorgaben, Auftragsfortschritt oder Maschinenzustände übersichtlich und aktuell den Mitarbeitern und Betriebsver- antwortlichen auf Großanzeigen oder mobilen Geräten anzuzeigen“, so Stimpfl. Für Dorningers Motivationsprogramm eine perfekte Ergänzung und wichtiger Beitrag zur Lean-Kultur von Banner.
Alle Kosten im Blick haben.
Das Lean-Production-Konzept von Banner ist fast komplett. Die auswärtigen Produktions- leiter bereits enorm beeindruckt. Um noch eins draufzusetzen, lässt Dorninger seinen Mitarbeiter Thomas Eggendorfer zu Wort kommen. Bei Banner ist er für den „Kontinu- ierlichen Verbesserungsprozess“ (KVP) zuständig. „Bis vor kurzem musste ich alle KVP- Projekte, Auswertungen und Grafiken mühevoll in Excel führen und verwalten“, erklärt Eggendorfer. Ein großer Aufwand: So musste der KVP-Verantwortliche alleine für circa 15 Abteilungen regelmäßige Ergebnis- berichte erstellen und aushängen. 2013 hat Banner dann entschieden, den KVP Guide von Gamed flächendeckend einzusetzen. „Angefangen von Verbesserungsvorschlägen über das Projektmanagement bis hin zu Wirtschaftlichkeitsauswertungen und Kennzahlen unterstützt der Guide alle am KVP beteiligten Mitarbeiter“, erklärt Stimpfl. „Genehmigungsverfahren und Projektfortschritte werden durch eine grafische Ablaufsteuerung mit E-Mail-Benachrichtigung unterstützt.“ Seitdem hat Thomas Eggendorfer jederzeit den Überblick über Status, Termin- und Kostensituation aller Projekte.
Am Ende der Führung möchte Dorninger dann doch noch eines klarstellen. „Es war ein harter Weg zur Lean Production, so wie sie heute ist. Dabei sind wir erst 60 Prozent des Weges gegangen“, gibt sich der technische Direktor bescheiden. Einen unternehmensexternen Austausch in Sachen Lean Production hält er für sinnvoll. Zumindest der Blick der dreißig Produktionsleiter dürfte in Zukunft sicher viel weiter als nur zum Tellerrand reichen.