Raketenbau : Abgespaced: Automatisierung in der Produktion von Raketen
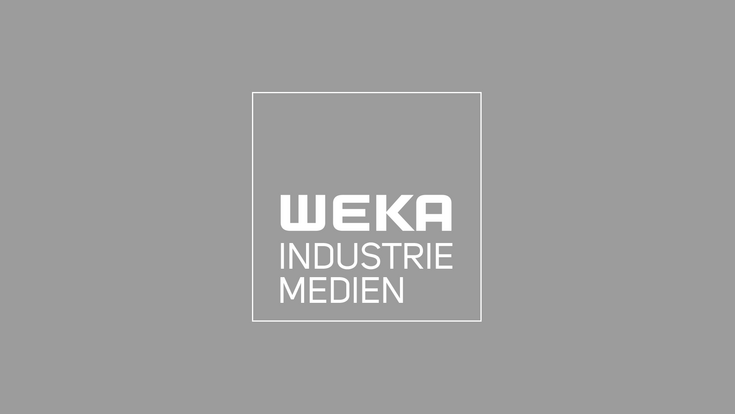
Die Automatisierung hat in jeglichen Bereichen der Produktion Einzug gehalten – auch in der Raumfahrtindustrie. FACTORY hat mit Dieter Grebner, Gründer und Geschäftsführer von Peak Technology und Piergiorgio Assandri, CIO bei Ingersoll Machine Tools, einem Schwesterunternehmen der Camozzi Group, unter anderem darüber gesprochen, worauf bei der Automatisierung in der Raumfahrtindustrie besonderer Wert gelegt wird, welche Verbundstoffe zum Einsatz kommen und wohin sich die automatisierte Raketenproduktion entwickeln wird.
Faserwickeln mit Mehrachsrobotern in Oberösterreich
Der oberösterreichische Leichtbauspezialist Peak Technology legt seinen Fokus auf den Aufbau von Fertigungs- und Prozess-Know-How beim Faserwickeln von Compositebauteilen. „Endlosfasern werden dabei in exakten Ablagemustern auf einem Wickelkern oder einer vorgefertigten Trägerstruktur mittels Mehrachsrobotern vollautomatisiert abgelegt. Die Ablagemuster entsprechen zuvor numerisch optimierten Lagenwinkeln“, erklärt Dieter Grebner, Gründer und Geschäftsführer von Peak Technology. Das verarbeitete Rohmaterial weist dabei eine sehr ausgeprägte mechanische Anisotropie, das heißt Richtungsabhängigkeit der Eigenschaften, auf. Wenn mehrere hunderte Kilogramm Faserverbundmaterial verarbeitet werden sollen, welches einer Dichte von ~1,6 g/cm³ mehreren Kilometern Fasern entspricht, ist das mittels Handarbeit nicht mehr realisierbar und moderne CNC gesteuerte Roboterarme übernehmen diese Aufgabe. Einmal programmiert, können so, mit sehr hoher Wiederholgenauigkeit gesamte Raketenstufen hergestellt werden.
Darauf wird bei der Automatisierung in der Raumfahrtindustrie Wert gelegt
Genau diese Technologie, das Wickeln von Faserverbundbauteilen wird weltweit zur Herstellung von Raketentanks, Zwischenstrukturen und ganzen Raketenstufen verwendet. „Diese Fertigungsmethode ist sehr gut mittels mehrachsigen Roboterarmen automatisierbar und erzeugt zudem extrem wenig Abfall, da das Rohmaterial direkt abgelegt wird und keine Rohmaterial Zuschnitte verwendet werden. Es kann dabei beinahe beliebig viel Material reproduzierbar verarbeitet werden“, berichtet Grebner. Diese Reproduzierbarkeit ist gerade in der Raumfahrt sehr wichtig, da gewisse berechnete und getestete Funktionen der Bauteile stark vom Herstellungsprozess abhängen und somit mittels „qualifizierter Prozesse“ einen sicheren Betrieb von Raketen Satelliten ermöglichen. „Das kosteneffiziente Zusammenspiel aus Mensch- und Maschine macht diesen Herstellungsprozess zudem besonders attraktiv und ermöglicht in relativ kurzer Entwicklungszeit die Substituierung klassischer und oftmals veralteter Herstellungsmethoden und Materialien“, führt Grebner weiter aus.
Das braucht es für den Raketenbau
„Abgesehen davon, dass der Anteil der Verbundwerkstoffe beim Bau von Raketen weiter zunehmen wird und Investitionen in Geräte für die Faserplatzierung und das Verlegen von Bändern nach sich ziehen wird, müssen wir bedenken, dass Verbundwerkstoff-Flugzeugstrukturen durch Aluminium- und Titanverbindungen zusammengehalten werden, die mit Fräsmaschinen hergestellt werden, wo dies möglich ist, und, wo dies nicht möglich ist, mit 3D-Druck für kleinere und komplizierte Teile“, erläutert Piergiorgio Assandri, CIO bei Ingersoll Machine Tools. Das Unternehmen ist ein Partner der US-amerikanischen Verteidigungs- und Luftfahrtindustrie und hat Prozesse zum Bau von Flugzeugstrukturen entwickelt, zunächst mit Fräsen, dann mit Verbundwerkstoffen und additiver Fertigung.
Nach Grebner stehen bei Leichtbaukennzahlen beinahe ausschließlich Aluminium und Kohlefaser, also Carbon, in direkter Konkurrenz. „Während Aluminium eine durchschnittliche Dichte von ~2,7g/cm³ besitzt, weist Carbon-Composite ~1,6g/cm³ auf. Dabei ergibt sich bereits ein Faktor von beinahe 2, welcher Kohlefaserstrukturen leichter machen würde“, sagt Grebner von Peak Technology. Allerdings müssen auch mechanische Eigenschaften berücksichtigt werden. Während Kohlefaser eine sehr starke Anisotropie vorweist und somit nur in Faserrichtung hohe mechanische Kennwerte erreicht, besitzt Aluminium im Rohzustand beinahe gleiche Kennwerte in alle Richtungen. „Ein besonderer Aspekt in der Raumfahrt sind Festigkeitswerte bei kryogenen Temperaturen wie sie zum Beispiel bei Treibstofftanks zum Einsatz kommen. Zusammenfassend kann man sagen, dass, je nach Optimierungsgrad des Aluminiumbauteils, eine Massenreduktion mit Compositebauweise im Bereich von 25 bis 40 Prozent möglich ist“, so Grebner.
Darum setzt man auf Verbundwerkstoffe
Verbundwerkstoffe sind stabiler und leichter als Stahl. Ein Kubikfuß Gussstahl wiegt ungefähr 222 Kilogramm. Abhängig von der Materialrezeptur können Verbundwerkstoffe bis zu 70 Prozent leichter sein, wobei ihre überlegene Belastbarkeit erhalten bleibt. „In der Luft- und Raumfahrt macht dann jedes eingesparte Pfund an Gewicht sofort eine entsprechende zusätzliche Portion Nutzlast wett. Das ursprüngliche Alpha 1.0 Fahrzeug von Firefly war eine Rakete mit einem Durchmesser von 6 Fuß und einer Nutzlastkapazität von 300 bis 500 Kilogramm. Firefly überarbeitete daraufhin seinen Business Case und kam zu dem Schluss, dass eine Alpha 2.0 nur dann marktfähig sein könnte, wenn sie eine Nutzlast von 1.000 Kilogramm tragen könnte, um den Bedarf für den Start mittelgroßer Satelliten in den niedrigen Erdorbit (LEO) zu decken“, so Assandri. Eine Rakete aus Verbundwerkstoffen schien die offensichtliche Wahl zu sein, angesichts der Erfahrung im Design und in der Herstellung von Verbundwerkstoffen, zusammen mit den Zielen, die Nutzlastkapazität zu erhöhen, ohne den Durchmesser zu vergrößern, das Gesamtgewicht so gering wie möglich zu halten und die Kosten pro Start bei etwa 15 Millionen US-Dollar zu halten. Firefly Aerospace ist ein US-amerikanisch-ukrainisches Raumfahrtunternehmen, das die Produktion von Raketen aus Verbund Werkstoff mit Ingersoll Machine Tools automatisiert.
Die Zukunft der Automatisierung in der Raketenproduktion
„Die Automatisierung in der Luft- und Raumfahrt wird demselben Weg folgen, den wir vor 50 Jahren in der Automobilindustrie gesehen haben. Nachdem die Prozesse in jeder einzelnen Fertigungszelle von Menschen auf Maschinen übertragen wurden (Intra-Zellen-Automatisierung), werden auch alle Vorgänge zwischen den Zellen, die mit Transfers und Logistik zu tun haben, an Roboter und FTS übertragen (Inter-Zellen-Automatisierung)“, meint Assandri. Er prophezeit, dass diese Entwicklung weiter von den Industrie 4.0-Fähigkeiten profitieren werde, die wir heute haben: die Möglichkeit, Sensoren hinzuzufügen und Daten von der Ausrüstung zu sammeln, die es erlauben, digitale und Fabrik-Zwillinge zu bauen, um alle Fertigungsvorgänge zu simulieren, vorauszusehen, zu unterstützen und zu optimieren.
„Im Falle von Flugzeugstrukturen, die zu groß sind, um sie auf einem Fließband abzufertigen, werden nomadische Roboter, die auf AGVs montiert sind und sich gemeinsam um ein Teil herum bewegen, die Prozesse ausführen“, so Assandri.
Das Ziel bei Peak Technology ist, eine Serienfertigung von hochkomplexen Raketenbauteilen, bis hin zu ganzen Raketenstufen, in einem stabilen und reproduzierbaren automatisierten Prozess am Standort Holzhausen zu etablieren. Dazu wurden mehrere Schlüsseltechnologien, Werkstoffe und Prozesse identifiziert. Diese Schlüsseltechnologien befinden sich in unterschiedlichen Entwicklungsstadien und werden in separaten Entwicklungsprojekten behandelt und gelöst.