Plasma Metal Deposition : 3DPMD: Vielfalt im Großformat
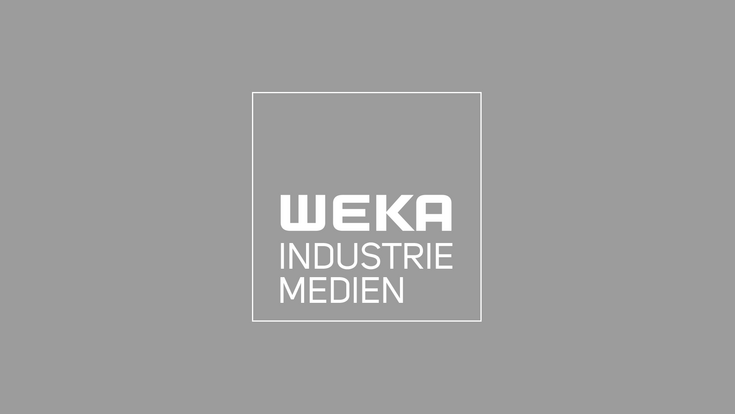
Beim 3DPMD-Verfahren (kurz: PMD) handelt es sich um ein „direct energy“ Verfahren, dass sich mit gängigen Verfahren der additiven Fertigung, wie etwa dem Pulverbettverfahren, nicht vergleichen lässt. Das Pulverbett hat seine Vorzüge, wenn ein sehr komplexes, filigranes und dennoch präzises Bauteil gefragt ist. Im Gegensatz dazu ist das PMD-Verfahren grobmotorisch, mit Wandstärken von 5 mm und dicker und somit für große Bauteile geeignet.
Österreichischer Forscherdrang
Vor fünf Jahren hat RHP-Technology begonnen alternative Technologien zur Pulverbett Sinter Technologie zu erforschen. Ziel des Unternehmens aus Seibersdorf war es, Bauteile mit einer Abmessung über einem halben Meter herzustellen. „RHP ist für Pulvertechnologie und Materialentwicklung bekannt und wir konnten bisher in zahlreichen Kunden- und Forschungsprojekten Wissen zur additiven Fertigung aufbauen unter anderem in dem wir begonnen haben mit verschiedenen Schweißtechnologien zu experimentieren“ erinnert sich Erich Neubauer, Geschäftsführer der RHP-Technology GmbH. Schließlich begann man mit dem PMD-Verfahren. Wie ein geübter Schweißer, der frei mit der Hand einen dreidimensionalen Gegenstand aufschweißt, baut eine Anlage koordiniert Lage für Lage Bauteile auf. „Wenn man diesen Schweißbrenner mit einem Roboter oder in einem Portalsystem bewegt, hat man durchaus auch die Möglichkeit Bauteile mit einem Durchmesser von einem Meter oder darüber hinaus herzustellen“ erklärt Neubauer.
Vielfältige Materialkombination
Mit dem PMD-Verfahren lassen sich auch Werkstoffe kombinieren und Multimaterialen herstellen. Werkstoffseitig gibt es kaum Einschränkungen erklärt Neubauer: „Wir können beispielsweise eine Werkzeugform aus einem Werkstoff aufbauen und eine finale Schicht mit anderen Eigenschaften aufbringen. Wir können mit Verbundwerkstoffen, aus partikelverstärkten Metallen, die Härte oder Verschleißfestigkeit verbessern oder Draht kombiniert mit keramischen Pulver verarbeiten.“
Von der Turbine bis zum Flugzeug
Es ist eine Kostenfrage, ob sich der Einsatz des PMD-Verfahrens lohnt. Je teurer der Grundwerkstoff, umso vorteilhafter ist das Verfahren. „Bei Aluminium ist der Rohstoff günstig und das Zerspanen kaum ein Thema. Hingegen bei Titanwerkstoffen oder Superlegierungen, die deutlich aufwendiger zu bearbeiten und teurer sind, ist das PMD-Verfahren wirtschaftlich sinnvoll“, argumentiert Neubauer.
Die Möglichkeiten zur Anwendung finden sich in vielen Bereichen: Turbinenschaufeln in Wasserkraftwerken oder Werkzeugformen, die andernfalls aus dem Vollen herausgearbeitet werden müssen. „Mit unserem Prozess wird der Bauteil endformnahe aufgebaut und abschließend noch minimal bearbeitet“, erklärt Neubauer. Insbesondere in der Luftfahrt hat das Verfahren aufgrund einer hohen Kosteneinsparung seine Berechtigung: „Speziell bei Titanwerkstoffen wird massiv Rohstoff verschwendet. Mit unserer Technologie bauen wir das Bauteil rohstoffsparend auf“, so Neubauer und führt weiter aus: „Wenn man Bauteile für die Luftfahrt herstellt zählt nicht nur der Kostenvorteil, die Sicherheit geht vor“. Nach seiner Einschätzung wird es noch einige Zeit dauern, bis PMD-Bauteile in kritischen Bereichen verbaut werden. „Qualifizierungsprozesse, die sicherstellen, dass das erste und das zehnte Bauteil genau dieselbe Qualität haben, sind in der Ausarbeitung. In Anwendungsfeldern wie der Luftfahrt sind Fehlstellen nicht tolerierbar. Es kann aber auch nicht jedes Bauteil in einem Computer-Tomographen überprüft werden“, so Neubauer. Er ist jedoch zuversichtlich, denn Firmen in den USA sind bei „direct energy“-Verfahren schon sehr weit und es gibt bereits erste Bauteile im Testbetrieb.
Schwachstellen und Potenziale
Abseits vom Einsatz in der Luftfahrt eignet sich das PMD-Verfahren für das Drucken von Ersatzteilen. „Wenn größere Bauteile im Lager permanent vorrätig sein müssen, weil die Herstellung große Vorlaufzeit hat, kostet es Unternehmen unnötig Geld“, so Neubauer. Auch im Prototypenbau hat das großformatige Fertigungsverfahren seine Legitimation.
Trotz aller Potenziale, die der Experte in dem Verfahren sieht, spricht er ganz offen an wo das Verfahren verbesserungswürdig ist. Beim Pulverbettverfahren, geht die Entwicklungshistorie deutlich weiter zurück, daher hat man es teilweise schon geschafft die Prozesssicherheit und Rohstoffüberwachung sicherzustellen. Insbesondere softwareseitig sieht Neubauer noch Entwicklungspotenzial: „Das man ein beliebiges 3D-Modell in den PMD „Drucker“ lädt, direkt die optimalen Parameter für den Aufbauprozess erhält und gleich loslegt, davon träumen wir derzeit noch.“ Wie viele Unternehmen am Markt arbeitet auch RHP gemeinsam mit Partnern an Lösungen, um diese Schwachstellen zu beseitigen. In der Zwischenzeit werden die Kinderkrankheiten bei RHP durch Manpower und Know-how kompensiert. „Wenn ein Bauteil mit dieser Technologie gebaut wird, sieht sich ein Mitarbeiter den Aufbaupfad an und korrigiert ihn gegebenenfalls“, sagt Erich Neubauer und zeigt sich zuversichtlich: „Es ist nur eine Frage der Zeit, bis die Durchgängigkeit der Prozesskette erlaubt, dass man eine Datei in die PMD Anlage lädt und am nächsten Tag das Bauteil ohne viel Zutun eines Mitarbeiters fertig ist.“
Fazit
Gerade bei der Fertigung großformatiger Metallbauteiler bietet das PMD-Verfahren gegenüber der Zerspanung aus dem Vollen oder dem Guß von Bauteilen neue Möglichkeiten. Beim Kauf einer PMD-Anlage sollte der künftige Betreiber jedoch wissen worauf er sich einlässt: Eine Serienproduktion mit stabilem Prozess ist einfacher zu realisieren als jeden Tag ein anderes Bauteil mit neuen Werkstoffen zu fertigen. Der Geschäftsführer von RHP resümiert: „Dass sich jemand eine Maschine kauft und sagt, heute mache ich ein Kupferteil, morgen Stahl und jedes Mal eine unterschiedliche Geometrie, soweit glaube ich ist man bei diesem Verfahren noch nicht. Da bedarf es schon eines geschulten Mitarbeiters.“