Innovation : 3D-Druck & Sensorik: So werden Knieorthesen intelligent
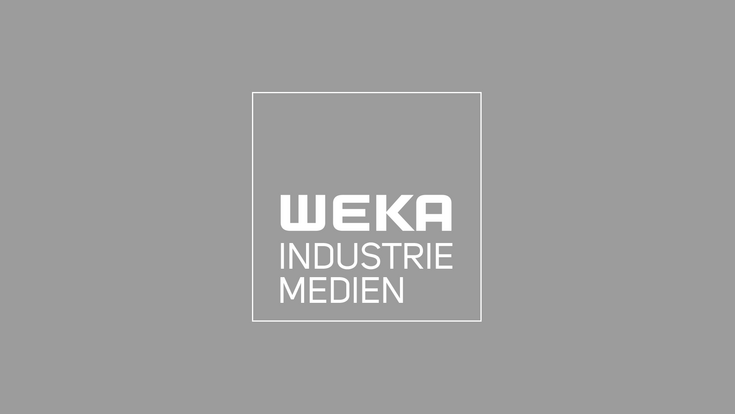
Anm. der Redaktion: Das ist ein Gastbeitrag von Rainer Salzberger, Digital Manufacturing Consultant, EOS
Es wurde schon viel über das Internet der Dinge (IoT) und die Vernetzung von Unterhaltungselektronik, Gebäudeinfrastruktur und auch Maschinenelementen berichtet. EOS ist überzeugt, dass man das volle IoT-Potenzial durch den klugen Einsatz von additiver Fertigung ausschöpfen kann. Denn so lassen sich intelligente und vernetzte Komponenten wesentlich einfacher und zudem ökonomischer integrieren. Tatsächlich könnte die Kombination von Sensorik, Konnektivität und 3D-Druck die Digitalisierung zu Anwendungen und Geschäftsszenarien führen, von denen heute – noch – niemand spricht.
Die Vorteile von Sensorik und 3D-Druck
Kombiniert man mechanische Designelemente mit eingebetteter Elektronik wie Mikrocontrollern, Sensoren und Konnektivität via Radiofrequenz (RF), wird dies heute als intelligente Bauteile – „Smart Parts“ – bezeichnet. Diese Bauteile ermöglichen ein maßgeschneidertes Produktdesign, das mittels hochpräziser, sicherer Datenübertragung in Echtzeit die Anforderungen spezifischer Nutzergruppen adressiert. Die additive Fertigung wiederum liefert unter anderem eine sehr hohe Gestaltungsfreiheit bei präziser Konstruktion sowie die Möglichkeit zur Funktionsintegration von Sensoren zur schnellen und gleichzeitig wirtschaftlichen Fertigung maßgeschneiderter Bauteile. Das erlaubt eine verkürzte Anlaufzeit für die Kleinserienproduktion und eine schnelle Markteinführung.
Eine neuartige Lösung für ein altbekanntes Problem
Dieser Ansatz lässt sich am Beispiel einer der häufigsten Knieverletzungen unter Beweis stellen: dem Kreuzbandriss. Verletzungen wie diese ziehen für gewöhnlich eine lange Genesungszeit nach sich, verbunden mit dem Risiko einer nur sehr zögerlichen Heilung oder sogar dauerhaften Beeinträchtigung. Die Gründe dafür sind in der Regel falsche Bewegungen oder eine zu starke Belastung des Knies während des Heilungsprozesses. Die Lösung wäre, Patienten direkt Rückmeldung bei falscher Belastung zu geben, ohne jedoch die Bewegungsmöglichkeiten massiv einzuschränken. Vor diesem Hintergrund hat EOS gemeinsam mit Blackbox Solutions eine in hohem Maße anpassbare, additiv gefertigte Knieorthese entwickelt, die mit integrierten Sensoren, der Fähigkeit zur Datenverarbeitung und RF-Konnektivität ausgestattet ist. Der Prototyp ist ein Beleg dafür, wie die verschiedenen Akteure rund um ein intelligentes Produkt wertvolle Echtzeiteinblicke durch Sensordaten erhalten und wie diese für alle Beteiligten vorteilhaft genutzt werden können. Die primären Anforderungen an die Knieorthese wurden durch Interviews mit allen direkt oder indirekt beteiligten Nutzern ermittelt: Man befragte Patienten, Ärzte und Medizingerätehersteller, welche Daten beziehungsweise Informationen dazu beitragen würden, die Patientenerfahrung und die ärztliche Versorgung zu verbessern.
Umfassende Analyse für komplette Genesung
Der entwickelte Prototyp besteht aus einer eingebetteten technischen Lösung, die sowohl das Nachrüsten bei einer vorhandenen Knieorthese mittels einem additiv gefertigten, maßgeschneiderten Ersatzgehäuse erlaubt als auch die direkte Integration in eine komplett additiv gefertigte Orthese. In allen Anwendungsfällen ist das kompakte Format der Sensoren besonders platzsparend und unterstützt damit die Leichtigkeit und Ergonomie der Knieorthese insgesamt. Die gewählte Sensortechnologie für Winkel- und Kraftmessungen vereint hohe Präzision mit einem berührungslosen Konzept, was die Integration erheblich vereinfacht. WiFi und Bluetooth-Low-Energy-Kommunikation erlauben ein Echtzeit-Monitoring. Dieses kann entweder über eine direkte WLAN-Verbindung mit der Knieorthese, oder über ein mobiles Gerät (z.B. ein Smartphone) als Benutzerschnittstelle und Controller, gesteuert werden. Die Datenanalyse erfolgt dann entweder auf Remote-Servern, über eine Anwendung auf einem lokalen mobilen Gerät und/oder direkt über den in der Knieorthese eingebetteten Prozessor. Wichtig ist, dass die sensiblen Daten der Nutzer auf sichere Weise vor Ort verarbeitet werden können und somit die Bestimmungen hinsichtlich Datenschutz und Privatsphäre erfüllt sind. Der Datenzugriff sowie die Analyse und Sicherung der gesammelten Informationen erfolgt über Schnittstellen, die auf die Bedürfnisse und Anforderungen der verschiedenen Nutzergruppen zugeschnitten sind. Batteriebetriebene Sensoren und vernetzte Software-Anwendungen können Patienten und Ärzte dabei unterstützen, die richtige Kniebelastung und den damit unterstützten Heilungsprozess in Echtzeit zu verfolgen und Reha-Maßnahmen nach den individuellen Patientenbedürfnissen auszurichten. Die vom intelligenten Bauteil eingehenden Echtzeitdaten ermöglichen den Herstellern einen unmittelbaren Einblick in die Nutzung und Leistung ihrer Produkte, so dass zukünftige Versionen verfeinert und verbessert werden könnten. Krankenkassen und Gesundheitsbehörden wiederum könnten die Daten nutzen, um bessere statistische Berichte über Krankheitsfälle zu erstellen.
Fazit
Der Orthesenprototyp mit seiner intelligenten Beobachtung des Kniegelenks zeigt an einem konkreten Beispiel das immense Potenzial, das in der Kombination von additiver Fertigung, Sensorik und Konnektivität liegt. Der industrielle 3D-Druck liefert dabei entscheidenden Beitrag: Dazu gehören die hohe Gestaltungsfreiheit auch bei einem kompakten und präzisem Design sowie die funktionale Integration von Sensoren. Letzteres ermöglicht, individualisierte Produkte in relativ kleinen Mengen schneller und ökonomischer herzustellen und gleichzeitig die Funktionalität des physischen Produkts kundenspezifisch zu optimieren. Dieser Ansatz kann verschiedensten Branchen als Inspiration dienen und auf zahlreiche weitere Anwendungen übertragen werden: Durch die Verwendung von intelligenten Bauteilen lassen sich be- oder entstehende Produkte weiter verbessern, die Kundenzufriedenheit steigern und neue Business Cases erschließen.