Lineartechnik : Warum Schunk die Pneumatik eliminiert
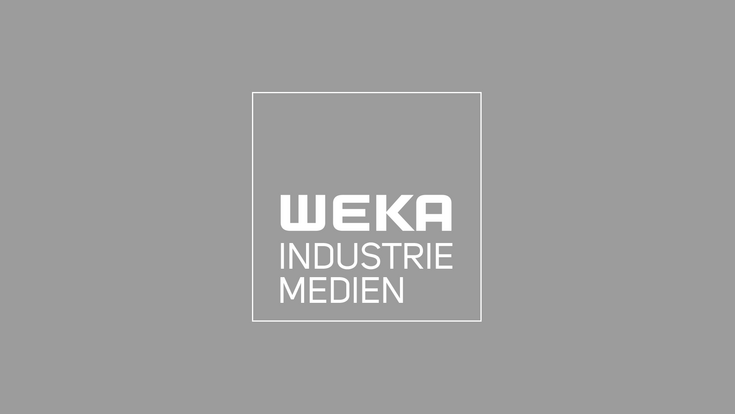
Es ist ein mechatronisches Pilotprojekt. Eigentlich gelten in der Großserienfertigung der Automotive-, Elektronik- und Konsumgüterindustrie pneumatisch gesteuerte Handhabungsmodule als Standard, doch damit könnte bald Schluss sein: Mit allerlei Finessen laufen nämlich mechatronische Handhabungsmodule den konventionell pneumatisch angetriebenen Komponenten den Rang ab. Vor allem wegen ihrer Verschleißvorteile und besseren Energieeffizienz gelten sie als interessante Newcomer. Einzig die Komplexität der Ansteuerung und der hohe Preis haben bislang verhindert, dass die Alleskönner sich rasant ausbreiten. Genau hier will Schunk mit einem mechatronischen 24-V-Standardprogramm für die Hochleistungsmontage alles ändern. Zentrales Element neben mechatronischen Greifern und Drehmodulen ist eine Linearachse mit verschleißfreiem Direktantrieb und Auto-Learn-Technologie. Diese Achse lässt sich nicht nur intuitiv bedienen, sie lernt sich selbst einzustellen. Pilotanwender ist Neumayer Tekfor in Hausach. Als einer der Ersten hat der Automotive-Spezialist die Gelegenheit beim Schopf gepackt und die smarte Schunk-Linearachse ELP in einer Prüfanlage für Schmiedeteile auf die Probe gestellt.
Mit smarter Achse zur längeren Lebensdauer
Neumayer Tekfor hat sich auf Komponenten und Baugruppen im Bereich Power Train spezialisiert. Pro Tag verarbeitet der ambitionierte Automobilzulieferer rund 100 Tonnen Stahl. Um eine maximale Qualität zu gewährleisten, durchlaufen alle funktionskritischen Teile eine penible 100-Prozent-Kontrolle. Rund 1,3 Millionen Schmiedeteile für Motorkomponenten und den Antriebsstrang werden produziert. Entsprechend hoch sind die Anforderungen an die eingesetzten Prüfmaschinen, die Neumayer Tekfor allesamt selbst baut. „Es ist unglaublich, wie rasant der Verschleiß der Anlagen steigt, wenn man die letzten sieben bis zehn Prozent Taktzeit herauskitzelt“, berichtet Jürgen Müller, Leiter Sondermaschinenbau bei Neumayer Tekfor, über die Zeit vor der smarten Linearachse von Schunk. Lag die Taktzeit für die Rissprüfung mithilfe der Wirbelstromtechnik vor 15 Jahren noch bei sieben bis acht Sekunden, wurde sie durch neue Technologien auf heute unter zwei Sekunden verkürzt. Großaufträge führten dazu, dass die Leistungsfähigkeit von pneumatischen Achsen durch das Öffnen der Drosseln bis an die Grenzen des Machbaren ausgereizt wurde. In der Folge stieg der Verschleiß der Stoßdämpfer rasant an. Auch andere Komponenten wurden durch die harte Fahrt in die Endlage und die damit verbundenen Erschütterungen in Mitleidenschaft gezogen. So sank die Lebensdauer eines Kamerasystems zur Detektion der Schmiedeteile von zehn Jahren auf gerade einmal neun bis zwölf Monate – ein auf Dauer unhaltbarer Zustand, den Schunk ändern sollte.
Schunks Versprechen auf die Probe gestellt
Schnell stellte sich für Müller heraus, dass die extrem schnellen Bewegungen in Verbindung mit der harmonischen Fahrt in die Endlage genau das war, was seine Maschinen brauchten. Der Leiter des Sondermaschinenbaus macht keinen Hehl daraus, dass Neumayer Tekfor seine Rolle als Pilotanwender auf die Spitze trieb. „Schunk hatte behauptet, die Achse sei kinderleicht einzubauen. Ohne Elektroniker oder Ingenieur. Genau das haben wir gemacht und die Inbetriebnahme einem Azubi im dritten Lehrjahr überlassen.“ Mit einer einzigen Rückfrage beim Elektriker sei es dem Berufseinsteiger möglich gewesen, die Achse anzuschließen und zu parametrieren. „Man gibt lediglich den Verfahrweg von A nach B an, schon ermittelt das Modul anhand der bewegten Masse vollautomatisch das optimale Verfahrprofil. Das ist kein Vergleich zur Programmierung konventioneller Achsen mit Regler.“ Nach acht Wochen Testbetrieb stand fest: Die Erschütterungen in der Maschine sind deutlich zurückgegangen und die Taktzeit konnte noch weiter erhöht werden.
Eliminierung der Pneumatik
Die selbstlernenden Schunk-Achsen enthalten jede Menge intelligenter Features, die den Aufbau mechatronischer Montagesysteme zum Kinderspiel machen. Verschleißfreie Lineardirektantriebe sowie verschleißarme Führungen senken den Wartungsaufwand auf nahezu null. Ausfälle durch überbeanspruchte Stoßdämpfer oder falsch eingestellte Drosseln gehören damit der Vergangenheit an. Zugleich sorgt die Eliminierung der Pneumatik für deutliche Einsparungen beim Kostenfaktor Energie und reduziert den Geräuschpegel. Im Vergleich zu pneumatischen Modulen ist die Schunk ELP im laufenden Betrieb rund 20 dB leiser. Für die Inbetriebnahme genügt es, die Normstecker (M8/M12) anzuschließen, die Endlage mechanisch mit einem Sechskantschlüssel einzustellen und die Ein- beziehungsweise Ausfahrgeschwindigkeit an zwei Drehcodierschaltern unmittelbar am Modul zu definieren. Bereits nach zwei bis fünf Hüben ist die Programmierung mithilfe der integrierten Auto-Learn-Technologie vollautomatisch abgeschlossen, ohne dass der Bediener den gekapselten Lernprozess beeinflussen müsste oder könnte.
Mit allen Steuerungen kompatibel
Während des Einlernvorgangs wird die maximal mögliche Geschwindigkeit bei jeweils aktueller Zuladung berechnet. Das Verfahrprofil selbst ist als Rampe angelegt, sprich abhängig vom Gesamthub beschleunigt und bremst die Einheit automatisch. Schläge und Schwingungen sowie eine unkontrollierte Fahrt mit Maximalgeschwindigkeit des Moduls sind somit ausgeschlossen. Ändert sich das Teilegewicht im laufenden Prozess, passt die Achse ihr Bewegungsprofi l innerhalb weniger Hübe automatisch an, ohne dass wie bei pneumatischen Modulen Drosseln eingestellt oder wie bei elektrisch gesteuerten Modulen neue Verfahrsätze aufgespielt werden müssen. Da die Ansteuerung über digitale I/O erfolgt, sind die Achsen mit allen gängigen Steuerungen kompatibel. Pneumatische Komponenten können 1:1 durch mechatronische ersetzt werden. Für den Betrieb sind weder Ventilinseln in der Anlage noch Antriebsregler im Schaltschrank erforderlich. Das spart Platz und jede Menge Zeit bei der Planung, Beschaffung und Inbetriebnahme. Auch die Kleinspannung kommt Müller entgegen: „24 Volt haben wir in der Regel sowieso bereits in jeder Maschine.“
Zum Auftraggeber: Neumayer Tekfor
Die Neumayer Tekfor GmbH in Hausach ist ein erfolgreicher Anbieter von Komponenten und Baugruppen im Bereich Power Train. Das Unternehmen beschäftigt rund 700 Mitarbeiter und erwirtschaftet einen jährlichen Umsatz von rund 140 Millionen Euro.
Zum Auftragnehmer: Schunk
Schunk bietet eines der weltweit größten Greifsystemeund Spanntechnik-Sortimente sowie das breiteste Standard- Greifkomponentenprogramm an. Erst kürzlich gewannen sie dafür auf der Hannover Messe den renommierten Industriepreis Hermes Award 2017.