Leitbetrieb Salzburg : Salzburg: Wie Atomic Austria seine Anlagen vernetzt
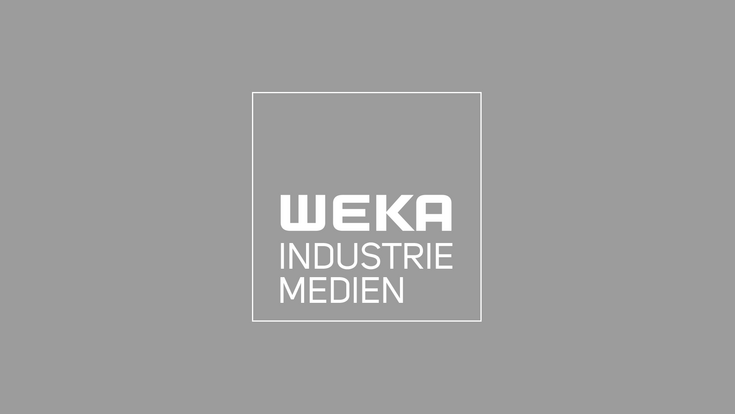
„Er schaut zwar einfach aus, aber ein Ski ist heute ein echtes „Hightech-Brettl“. Stephan Buchsteiner ist Manager Operations bei Amer Sports, darunter fallen die Markenschwestern Salomon und Atomic. Der gelernte Produktionstechniker ist mitverantwortlich für einen reibungslosen Ablauf in der Ski-Produktion von Altenmarkt. Im Salzburger Werk werden im Zwei-Schichtbetrieb bis zu 400.000 Paar Alpinski pro Jahr produziert. Die Bindung nicht miteinberechnet werden so pro Ski bis zu 30 Einzelkomponenten verbaut. Bei 1.100 unterschiedlichen Modellen und Längen eine echte Herausforderung besonders an die Anlageneffizienz. Seit zwei Jahren setzen die Salzburger deswegen intensive Schritte Richtung Systemvernetzung. Das große Ziel: Eine smarte Skiproduktion, die sich ganz von selbst steuern und regeln kann. Eine Industrie 4.0-Disziplin, der Buchsteiner und sein Team schon zum Greifen nahe sind. Denn erste Erfolge zeichnen sich bereits ab und machen diese Salzburger Produktionsstätte zu einem smarten Vorreiter. Schritt eins: Anlagenvisualisierung.
Eine Skiproduktion kann vereinfacht auf zwei Kernprozesse runtergebrochen werden. „Das Pressen und Schleifen“, wie es Buchsteiner nennt. Vor allem im Bereich des Schleifens sieht die Projektgruppe viel Potenzial für Industrie 4.0-Anwendungen. „In diesem Prozess können die sehr viele Schwierigkeiten auftreten“, erklärt der Amer Sports-Manager. „Ein Ski durchläuft dabei bis zu acht Schleifaggregate und erst nach einer finalen Qualitätsprüfung darf er in den Verkauf.“ Um hier die Anlageneffizienz zu erhöhen und vor allem Reaktionszeiten bei Störungen zu verkürzen, suchten die Salzburger nach einem passenden Produktionssystem. Alle nötigen Anlageninformationen sollten damit in Echtzeit visualisierbar werden. Seit 2013 zieht die vom Salzburger Systemhaus Copa-Data entwickelte HMI SCADA Software zenon die Fäden in der Altenmarkter Skiproduktion. Schöner Nebeneffekt: Neben der Anlagenvisualisierung konnten damit auch die Rüstzeiten reduziert werden. Dauerte früher das Wechseln der Schleifsteine fast 30 Minuten, sind die Anlagenbediener heute um fast ein Drittel schneller. „Kommt es wegen dieses Wechsels bei einer Linie zur Unterbrechung sind andere Anlagen und Mitarbeiter automatisch vorgewarnt“, erklärt Buchsteiner die Kommunikation der Linien über das Produktionssystem. „Nächster Schritt soll ein intelligentes Prüfsystem werden“, blickt der Amer Sports-Mann bereits in das nächste Jahr. Ganz nach dem Lean-Gedanken wollen sich die Salzburger ganze Schleifgänge sparen und somit die Schleifeffizienz weiter erhöhen. Wie? „Indem das Prüfsystem in Echtzeit den Qualitätsstatus des Skis nach jeder Schleifphasen abrufen kann“, erklärt Buchsteiner. Damit wüsste man sofort wann der benötigte Qualitätsstand erreicht sei und erspare sich unnötiges zusätzliches Schleifen. Auch ihren Materialbestand wollen die Skiproduzenten drastisch reduzieren. “Im Moment arbeiten wir in der Fertigung mit einem konstanten Sicherheitsbestand von 11 Tagen“, erklärt Buchsteiner. Über eine Schnittstelle ins ERP-System will man die Bestände besser verstehen beziehungsweise steuern und damit die Materiallogistik auf ein neues Level anheben. Das große Ziel: Die jetzigen Sicherzeiten um 25 Prozent reduzieren. Smarte Druckluft.
Auch in der Infrastruktur läuft’s bei den Salzburger schon so richtig smart. Dort sind alle Bereiche wie Stromverbrauch, Luftfeuchtigkeit und Temperatur bereits über eine Plattform miteinander vernetzt. Cleverster Vorreiter ist dabei der Druckluftbereich. Die Salzburger verpassten ihren Kompressoren eine äußerst clevere Steuerung. Warum, erklärt Buchsteiner so: „Für den Schleifprozess ist es unter anderem einen konstanten Druck zu haben. Früher konnten die Salzburger nur hoffen, dass ein Mitarbeiter einen Druckverlust frühzeitig bemerkte. Ansonsten hieß es „wieder alles von vorn“, so der Manager. Heute regelt ein autonomes System den Druckverlust und greift dabei auf eine intelligente Prioritätenliste zu. „Kommt es zu einem Druckverlust, schalten sich mittlerweile zwei Back-Up Kompressoren automatisch dazu“, so Buchsteiner. Da diese schwächeren Notfallvarianten aber das Luftvolumen nicht zur Gänze erbringen können, schaltet das System automatisch weniger wichtige Arbeitsprozesse kurzfristig ab. Industrie 4.0 ermöglicht den Skibauern nun auch eine optimale Anpassung an sich verändernde Geschäftsmodelle. So hat sich die Art der Nachbestellungen in den Vorweihnachtsmonaten wesentlich verändert. „Die Kunden bestellen immer später in immer kleineren Losen nach“, so Buchsteiner. „Da sind flexible Lösungen gefragt.“ Damit diese Just-In-Sequence-Produktion reibungslos abläuft, machen die Salzburger ihre Anlagen gerade fit für Losgröße 1. Die Hightech-Brettln sollen nämlich weltweit zeitgerecht unterm Christbaum liegen. (EB) Kurz und Knackig:
Das versteht Stephan Buchsteiner unter Industrie 4.0 Systemvernetzung: Vernetzung sämtlicher Information entlang der Supply Chain. Was ist für Sie das Unwort des Jahres in Zusammenhang mit Industrie 4.0?Schnittstellenproblematik: Nicht immer nur von Standards reden, sondern endlich welche durchbringen.