3D-Druck : Österreichs schnellstes Trainingsflugzeug setzt auf 3D-gedrucktes Treibstoffsystem
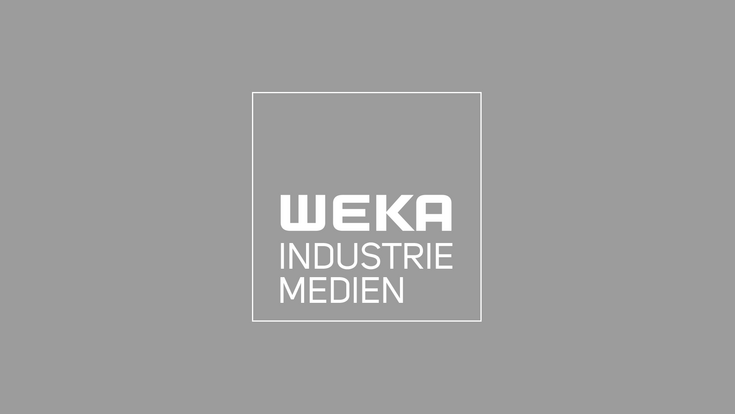
Hoch – und vor allem schnell hinaus. In Niederösterreich wird aktuell am schnellsten Trainingsflugzeug gearbeitet, das je in Österreich entwickelt wurde. Ermöglicht werden die Höchstgeschwindigkeiten durch oststeirisches Know-how: Durch den 3D-Druck von M&H wird das Treibstoffsystem aus lediglich drei Komponenten hergestellt.
Schon in wenigen Wochen steht der Jungfernflug der 750 PS starken Trainingsmaschine am Flugplan. Der Geschwindigkeit kommt dabei im doppelten Sinne eine wesentliche Bedeutung zu: Einerseits beläuft sich die reine Entwicklungszeit der niederösterreichischen Luftfahrtingenieure von CEA Design (CEAD) mit Hauptsitz ist Kottingbrunn auf rasante 18 Monate, andererseits ist auch der Turboprop-Trainer selbst für Höchstgeschwindigkeiten ausgelegt. Rund 550 Kilometer pro Stunde soll das Schulungsflugzeug, das speziell auch für die Ausbildung von Piloten konzipiert wurde, erreichen – ein schnelleres Trainingsflugzeug wurde in Österreich noch nicht entwickelt, bestätigt CEAD-Technikchef Clemens Knappert: „Wir sind mit Entwicklung und Produktion des Trainers beauftragt, der in dieser technologischen Qualität – auch was Materialien und Aerodynamik angeht – einzigartig ist.“ Heißt: Das aus dem besonders leichten Karbonmaterial hergestellte Flugzeug garantiert höchste Lebensdauer sowie maximale aerodynamische Güte.
3D-Druck aus Ilz
Die technologische Raffinesse der Turboprop-Maschine endet nicht an der Außenschale des Luftfahrzeugs – im Gegenteil. Knapp 1.000 Liter werden pro Flugstunde zwischen den vier Tanks mit drei Hauptpumpen befördert, die Rückenflugtauglichkeit des Flugzeugs erhöht die Komplexität zusätzlich. Zwischenzeitliches Ergebnis der Entwicklung war ein nicht aufzulösendes Wirrwarr an Spritleitungen und Kopplungsstücken auf engstem Bauraum, was die Ilzer 3D-Druck-Pioniere von M&H auf den Plan gerufen hat.Die oststeirischen Experten haben gemeinsam mit CEAD das 50-teilige Treibstoffsystem auf drei topologisch optimierte 3D-Druck-Komponenten reduziert. „Mehr Bauteile sorgen für mehr potenzielle Fehlerquellen sowie eine extrem komplexe Wartung im Fall von Undichtheiten. Auch strömungstechnisch sind eine derart hohe Anzahl an Verbindungselementen auf engstem Raum kritisch“, sagt M&H-Geschäftsführer Patrick Herzig. „Mit der additiven Fertigung können wir eine Vielzahl von Bauteilen auf eine Komponente reduzieren, da der Geometrie keine Grenzen gesetzt wird. Dadurch wird zusätzlich auch Gewicht eingespart, was im Fall der Luftfahrt ein entscheidender Vorteil ist“, sagt Herzig. Kostentechnisch sei der 3D-Druck in diesem Fall „mehr als konkurrenzfähig. Auf lange Sicht sogar günstiger“, sagt Auftraggeber Knappert. Denn: „Im Wirrwarr der Spritleitungen ist ein Leck mit hohem Umrüstaufwand verbunden. Nun verfügen wir über eine elegante, platzsparende Lösung“, so der CEAD-Technik-Chef.