Expansion : 3D-Druck Start-up Cubicure geht in die Spritzgussoffensive
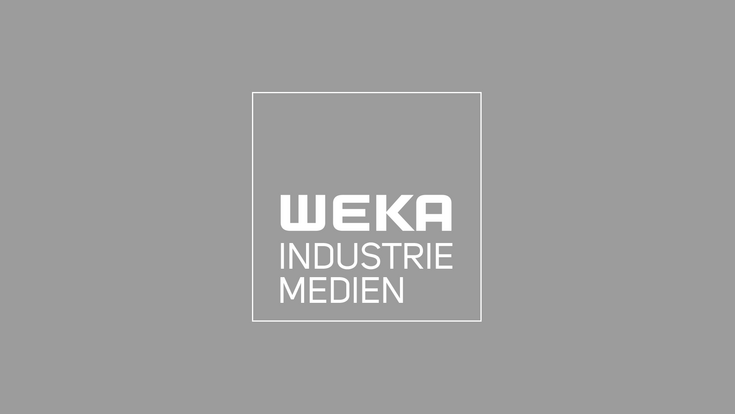
Erst vor wenigen Tagen ist man aus Frankfurt zurückgekehrt. Auf der formnext, dem internationalen (Messe-)Schaufenster für additive Fertigungstechnologien der Zukunft, präsentierte man nicht nur seine 3D-Drucktechnologie selbst, sondern gleich auch zwei neue Kunststoffvarianten, die zukünftig als „Standard-Druckmaterial“ bestimmte Anwendungsgebiete abdecken sollen. „Cubicure Precision“ und „Cubicure Evolution“ nennen sich die beiden hochviskosen Photopolymere mit guter Wärmeformbeständigkeit, die entweder (Precision) für absolute Präzisionsanwendungen, wie etwa den Druck von Mikrobauteilen, oder (Evolution) für die Fertigung funktionaler Prototypen, bei denen wiederum Festigkeit und Zähigkeit eine wichtige Rolle spielen, gedacht sind. Der gesammelten Aufmerksamkeit der Messeöffentlichkeit konnte sich Cubicure aber schon allein wegen seines revolutionären Hot Lithography-Verfahrens, mit dem erstmals Hochleistungsphotopolymere für den industriellen 3D-Druck verarbeitet werden können, sicher sein. Und so war es dann auch. „Die Messe ist für uns sehr, sehr gut gelaufen“, freut sich Markus Pfaffinger, zuständig fürs Business Development bei Cubicure. „Der Andrang und das Interesse der Besucher waren enorm, erfreulicherweise auch seitens vieler großer Unternehmen. Wir konnten während der formnext sogar die eine oder andere Maschine am Markt platzieren“, so Pfaffinger weiter.
Fertigungspartner für den Zusammenbau
Da passt es sehr gut, dass am Wiener Firmenstandort derweilen die ersten fünf verkauften Hot Lithography 3D-Drucker fertig zusammengeschraubt und für die Auslieferung vorbereitet wurden. Einer davon wird künftig am FH Campus Wien seine Dienste verrichten, ein anderer macht sich auf den Weg nach Übersee – zu einem US-amerikanischen Kunden. Da man beim Zusammenbau der Maschinen inzwischen aber an einige (vor allem platzbedingte) Kapazitätsgrenzen stößt, soll diese Arbeit im kommenden Jahr übrigens an einen Fertigungspartner ausgelagert werden. „Die Maschinenentwicklung und die Herstellung der Kunststoffe verbleiben natürlich weiterhin im Haus. Hier geht es einzig und allein um den Zusammenbau der Drucker“, erklärt Pfaffinger. Konkretere Details, oder gar den Namen des künftigen Fertigungspartners, will man an dieser Stelle freilich noch nicht verraten.
3D-Druck trifft Spritzguss
Dafür lässt man sich bei Cubicure aber bei der Materialentwicklung ein bisschen genauer in die Karten schauen. „Im Laufe des kommenden Jahres wollen wir unter anderem ein neues Hochtemperaturmaterial vorstellen“, erzählt Pfaffinger. Dieser Kunststoff soll problemlos mit Temperaturen von 250 bis 300 Grad zurechtkommen und sich damit beispielsweise ideal für die Herstellung von Spritzgusswerkzeugen eignen. Ein ebenso großes Thema werden im kommenden Jahr außerdem die so genannten Füllstoffe werden, die man den Kunststoffen beimischt, um ihre Eigenschaften (etwa tribologischer Art) zu beeinflussen und zu verändern. Generell bemühe man sich aber „das Portfolio in Sachen Standardmaterialien eng zu halten“, wie Pfaffinger betont. „Viele Kunden haben nämlich sehr spezifische Anforderungen, die eben nicht von Standardprodukten abgedeckt werden können. Und genau für diese Kunden möchten wir auch sehr spezifische Materialien entwickeln. Das ist ja auch eine unserer besonderen Stärken.“
Bauteilstrukturierung nach der Top-Down-Methode
Eine weitere Stärke von Cubicure steckt im Hot Lithography-Verfahren selbst. Nur mit dieser Technologie ist es derzeit möglich, die gewünschten Materialeigenschaften mit guten Oberflächen zu verbinden. Letzteres spielt vor allem dort eine entscheidende Rolle, wo das Bauteil im Einsatz von Flüssigkeiten oder Gasen umströmt wird. Kanten können dank Hot Lithography mit hoher Präzision gefertigt und damit auch ganz exakt abgebildet werden. „Mit einer Laserspotgröße von minimal 10 µm, können wir die Bauteile sehr fein strukturieren. Und auch die Schichtstärke ist bei unserem Drucker flexibel einstellbar“, betont Pfaffinger.
Die Bauteilstrukturierung erfolgt übrigens nach der Top-Down-Methode. Das heißt, die Belichtungseinheit belichtet das auf einer transparenten Fläche aufgetragene Rohmaterial von unten. Dadurch polymerisiert und haftet das Photopolymer selektiv an der von oben zugestellten Bauplattform. Ein weiterer großer Vorteil: Dieser Prozess ist enorm materialsparend und reduziert somit auch den Reinigungsaufwand. „Vereinfacht gesagt ist es unser Ziel, mit dem 3D-Drucker Spritzgussqualität zu liefern“, bringt es Pfaffinger auf den Punkt. Apropos Spritzguss. „Bei kleineren Bauteilen, so genannten Mikrobauteilen, sind wir schon jetzt in der wirtschaftlich sinnvollen Serienfertigung angekommen. Bei größeren Bauteilen reden wir aber nach wie vor eher von Kleinserien beziehungsweise funktionalen Prototypen.“