AutoForm bei Wesoba : Rückfederungen wettbewerbsrelevant kompensieren
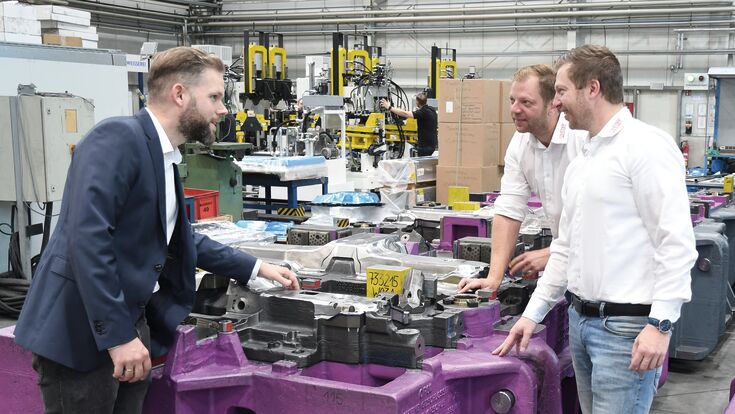
Wesoba sichert den Werkzeugbau bis zum Tryout systematisch mit Simulationstools von AutoForm ab. Damit kommt das Unternehmen aus dem erzgebirgischen Schwarzenberg schneller zum ersten Bauteil und agiert planungssicher sowie kosteneffizient.
- © Wesoba„Im Werkzeugbau konzentrieren wir uns auf Transfer- und Linienwerkzeuge für Stahl-, Edelstahl- und Aluminiumbauteile. Schwerpunkt ist das gezogene Teil mit komplexer Geometrie – hier entwickeln wir uns konsequent zum größeren Werkzeug weiter“, berichtet Geschäftsführer Georg Pfaff. Zunehmend geschieht dies auch für Teile aus hochfesten Stählen – extreme Toleranzen und hohe Oberflächenansprüche sind ohnehin zu erfüllen: „Diese Kombination erklärt, warum wir simulieren müssen. Erfahrungswissen und händisches Arbeiten reichen einfach nicht mehr aus.“ Daher baut Wesoba die Zusammenarbeit mit AutoForm konsequent aus, um Modell und Werkzeug immer besser übereinzubringen: „Wir sind jetzt die ersten Schritte in Richtung Oberfläche gegangen. In langfristigen Kooperationen werden wir diesen Weg mit unseren Kunden fortsetzen, sodass diese selbst einschätzen können, welcher Schritt als nächster möglich ist.“
Lesetipp: KI beim Schrauben-Großhändler garantiert sofortige Warenverfügbarkeit
AutoForm nimmt in dieser Konstellation mittlerweile eine besondere Rolle ein: Die Zusammenarbeit hatte zwar schon 2008 begonnen, richtig intensiv wurde sie jedoch vor etwa zwei Jahren. AutoForm stellt für Wesoba die Lösung dar, die Herstellbarkeit der Bauteile zu garantieren und den Kunden mit Gewissheit sagen zu können, ‚das funktioniert‘. So erhält man in Schwarzenberg frühzeitig im Fertigungsprozess die entscheidende Unterstützung auf dem Weg zum maßhaltigen Teil. Zudem verschafft AutoForm einen Zeitsprung in der Entwicklung. Speziell mit dem AutoForm-Compensator bekommt Wesoba eher die fertige Kompensation: Was früher mehrere händische Korrekturschleifen samt Konstruktionsänderung, Umprogrammierung, Schweißen, mechanischer Bearbeitung und Tryout erforderte, macht mittlerweile das Programm – und zwar schneller und genauer.
Vergleiche von Simulation und Werkzeug
Begonnen hat die intensivierte Zusammenarbeit mit Schulungen zu AutoForm Forming, die auf die Erstellung von Class-A-Flächen ausgerichtet waren. Bei einem Grauzonenteil, an dem geschult wurde, musste denn auch keine einzige Schleife gefahren werden: 97 % aller Messpunkte waren sofort in Ordnung. Im Anschluss wurde mit einem Radhaus für Mercedes-Benz gleich ein erstes Projekt umgesetzt und die Kompensation Schritt für Schritt gemeinsam aufgebaut. Beim Radeinbau gab es dann zunächst eine Abweichung zwischen Simulation und Praxis. In mehreren Runden wurde zusammen nach der Ursache geforscht, woher diese Abweichung stammt. Auch Fragen zur Auswertung am Bauteil sind geklärt worden. Schließlich war die Lösung gefunden und das Bauteil konnte produziert werden. Die Schulung, der Service und die Anwendung liefen sehr gut ab – mittlerweile wird ohne AutoForm-Compensator kein Teil mehr in Schwarzenberg gefertigt.
Der AutoForm-Compensator ordnet sich ein in eine Reihe von AutoForm-Tools, die Wesoba heute prozessbegleitend einsetzt. Zuerst wird dabei das Design eines Bauteils – mitunter schon vor Angebotslegung – auf Herstellbarkeit geprüft. Nach Rücksprache mit dem Kunden erfolgt anschließend die Simulation der Methode in AutoForm. Steht diese, wird das Werkzeug konstruiert und erstmals kompensiert, um etwaige Probleme der Herstellbarkeit herauszuarbeiten. Sind die Bauteile im Guss – ist das Werkzeug fertig – startet eine weitere Kompensation. Im nächsten Schritt liegt dann ein fertiges Ziehteil vor, von dem die Experten die Flächen scannen. Um diese Flächen zu bewerten, wird erneut der AutoForm-Compensator genutzt. Schließlich werden die Fräsflächen für die Beschneidwerkzeuge umgesetzt. Auf diese Art erfolgen prozessbegleitend immer wieder Vergleiche von Simulation und Werkzeug – bis das erste Teil vorliegt.
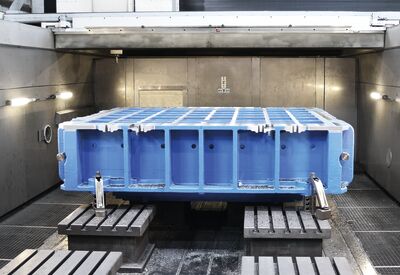
Standard im Automobilbau
Wesoba zieht aus der Arbeit mit dem AutoForm-Compensator im Wesentlichen drei Haupteffekte: Erst einmal nähert man sich damit immer mehr der Praxis an. Zudem werden Zeit und Kosten gespart, weil weniger Korrekturschleifen anfallen und schneller Ergebnisse vorliegen. In der reinen Kompensationsarbeit sind das pro Teil locker drei Wochen Arbeit. Drittens sind die Ergebnisse genauer als beim händischen Arbeiten. Dabei kann neben der Rückfederung in Werkzeuglage heute auch die in Fahrzeuglage bestimmt und auf diese Art die Schwerkraft berücksichtigt werden. Auch deswegen fällt das Fazit im Erzgebirge sehr positiv aus: „Ohne Tools wie den AutoForm-Compensator würden wir uns die immer größeren, komplexeren Teile ebenso wenig zutrauen wie die Sichtteile“, unterstreicht Christian Pfaff, der zusammen mit seinem Bruder das Unternehmen leitet. „AutoForm schafft aber auch Vertrauen – nicht nur, weil dem Kunden klar wird, was alles bei der Simulation zu beachten ist oder wie ausgewertet werden muss, sondern auch, weil AutoForm einfach Standard im Automobilbau ist.“
Das aktuelle Ziel von Wesoba ist übrigens, Werkzeug und Simulationsmodell immer genauer übereinanderzulegen. Zum Beispiel bei höchstfesten Stählen. Auch die tribologischen Werte aus dem TriboForm Plug-In könnten künftig dazu beitragen, kompliziertere Teile noch realitätsnäher zu simulieren. Gleichzeitig sollen die Simulationen vermehrt Stellgrößen aufzeigen, mit denen sich Problembereiche beeinflussen lassen. Nicht zuletzt wird Wesoba zukünftig die CAD-Arbeit mit dem AutoForm-ProcessDesignerfor CATIA beginnen, um auch bei der Konstruktion Zeit zu sparen.
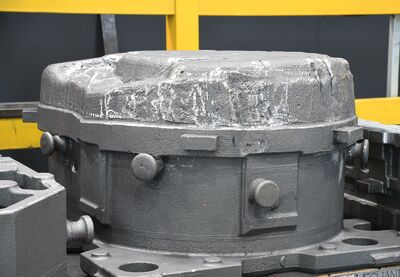