Anwenderbericht : Drexelius optimiert die Fertigung mit Ingersoll Werkzeugen
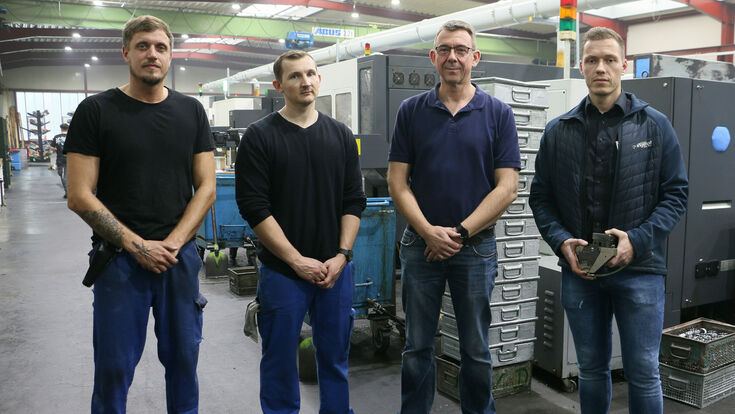
Konnten verschiedene Prozesse gemeinsam optimieren (v.l.): Tim Schiller (Einrichter Drexelius), Alexander Wolf (Fertigungsleiter Drexelius), Björn Hering (Geschäftsführer Drexelius) und Kevin Richstein (Technischer Berater Ingersoll).
- © Ingersoll Werkzeuge GmbHDas Unternehmen wurde 1965 von Wilhelm Drexelius in einer Scheune gegründet und später durch seine beiden Söhne weitergeführt. Mangels Nachfolge konnten die heutigen Geschäftsführer Björn Hering und Thomas Gutstein die Firma 2008 übernehmen. Beide sind gelernte Dreher ohne kaufmännischen Hintergrund, was Björn Hering nicht als Nachteil empfindet: „Im Endeffekt ist es am wichtigsten, zu wissen, was in der Fertigung passiert. Eine Maschine bedienen zu können ist wichtiger als die Zahlen. Dafür hat man seine Leute und bekommt auch über die Jahre ein Gefühl dafür.“ Hering war der erste Lehrling im Unternehmen gewesen und ist heute Chef seines früheren Ausbilders.
Aktuell zählt Drexelius insgesamt 35 Mitarbeiter. Über viele Jahre hinweg arbeiteten die beiden Geschäftsführer selbst in der Fertigung mit. Mittlerweile sitzt Hering fast ausschließlich im Büro, was dem Wachstum des Unternehmens geschuldet ist. Gutstein teilt sich seine Zeit in Produktion und Büroarbeit auf. Der Dreherei stehen auf einer Produktionsfläche von 2.100 Quadratmetern 21 Maschinen zur Verfügung, überwiegend vom Hersteller Nakamura. Alle sind mit Hauptspindel, Gegenspindel und Y-Achse versehen und verfügen über zwei oder drei Revolver. Diese Ausstattung ermöglicht Drexelius die Komplettbearbeitung aller Bauteile auf einer Maschine. Von der Stange werden Teile im Durchmesserbereich von 8 bis 100 mm gefertigt, die Maschinen sind durchweg mit Stangenladern versehen.
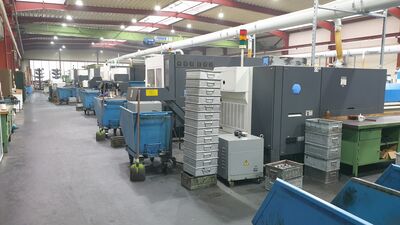
Typische Losgrößen bewegen sich zwischen 100 und 10.000 Stück, wobei der Hersteller drauf achtet, stets einen gewissen Anteil an großen Serien am Laufen zu haben. „Würden wir auf 21 Maschinen jeweils nur 100 Teile fertigen, kämen wir mit dem Programmieren und Rüsten nicht mehr hinterher“, so Björn Hering. Früher war das Unternehmen auch mal stark in der Fertigung von Prototypen und Musterteilen vertreten. Davon hat sich Drexelius nach und nach verabschiedet, weil es zunehmend schwerer wurde, den wachsenden organisatorischen Aufwand für Qualitätssicherung, Prüfberichte und Dokumentation umzusetzen. Wirtschaftlich sei das nicht mehr vernünftig darstellbar gewesen, so das Unternehmen.
Lockenwickler aus Holz
Ein Schwerpunkt bei den verarbeiteten Materialien liegt bei Edelstählen, in Finnentrop werden aber auch Teile aus anderen Stählen, wie etwa Automaten-, Einsatz- und Baustählen sowie Aluminiumlegierungen gefertigt. „Für ein Haarstudio haben wir auch schon mal Lockenwickler aus Holz gedreht“, berichtet Thomas Gutstein schmunzelnd. Drexelius hat einen breiten Kundenkreis. Einen großen Anteil haben Sanitär- und Armaturenhersteller, aber auch die Bereiche Landwirtschaft, Mess- und Regeltechnik, Maschinenbau und Medizintechnik werden beliefert.
Bewusst verzichtet wurde auf die Automobilbranche. Zu einer Ausnahme kam es allerdings 2021, als Drexelius einen Auftrag von einer anderen Dreherei übernahm, die Probleme hatte, ein Edelstahldrehteil für einen Motor in der verlangten Qualität und den erforderlichen Mengen herzustellen. Mit den vorhandenen Werkzeugen lief es allerdings auch bei Drexelius nicht auf Anhieb rund. Die Standzeit der zunächst eingesetzten Platten ließ zu wünschen übrig, die Oberflächenqualität passte nicht und am Drehteil zeigte sich Gratbildung.
„Diese Platten funktionieren“
Hilfesuchend wandte man sich an Ingersoll und bekam eine Lösung. Mit der Wendeschneidplatte DCMT 11T308 MT TT8020 aus dem Portfolio des Werkzeugherstellers aus Haiger erreichte der Anwender auf Anhieb die gewünschte Qualität und Produktivität. „Diese Platten funktionieren“, lautete die Rückmeldung aus der Fertigung. Weil man mit den Schneidplatten sehr zufrieden war, wurden sie in der Folge immer wieder als Problemlöser eingesetzt und nach und nach zogen weitere Werkzeuge von Ingersoll in die Fertigung ein, darunter auch Gewindeschneidplatten, Bohrer und Abstechwerkzeuge.
Lesetipp: Kern Micro HD bei Doceram zur Keramikbearbeitung
„Der Einsatz neuer Werkzeuge steht und fällt mit der Akzeptanz bei den Mitarbeitern“, weiß Björn Hering. Doch hier kam die Anregung, weitere Produkte von Ingersoll auszuprobieren, aus der Belegschaft, die von der Laufruhe der Ingersoll Werkzeuge sehr angetan war. Dass die Mitarbeiter gerne die besten am Markt verfügbaren Werkzeuge haben möchten, ist durchaus im Sinne der Geschäftsleitung, die den wirtschaftlichen Aspekt im Blick hat. Wenn Werkzeuge nicht gut arbeiten, tritt häufig hoher Plattenverschleiß auf oder die geforderte Oberflächenqualität ist nicht prozesssicher herzustellen. Zu Unruhe in den Abläufen kommt es auch, wenn Mitarbeiter ständig neue Parameter ausprobieren müssen, um halbwegs befriedigende Resultate zu bekommen.
Lange Späne beim Bohren
Bei einem Werksbesuch hat Kevin Richstein, technischer Berater bei Ingersoll, einen prüfenden Blick in die Container an den Maschinen geworfen und entdeckte dort sehr lange spiralförmige Bohrspäne. Sie entstehen beim Bohren in langspanende Materialien wie S355 oder C15 und waren Drexelius schon länger ein Dorn im Auge. Dass die Mitarbeiter alle halbe Stunde die Spänekübel leeren müssen, ist dabei noch das kleinere Problem. Lange Wirrspäne beeinträchtigen auch die Prozesssicherheit, können Probleme bei der Übergabe verursachen oder Bauteile zerkratzen. Richsteins Analyse: „Das bekommt Ingersoll besser hin!“
Mit dem QuadTwist führte er einen Wendeplattenbohrer für die bei Drexelius verlangten großen Durchmesser ein. Der Bohrer ist ein Kassettenwerkzeug, das nicht nur den aktuell benötigten Durchmesser von 63 mm realisiert, sondern im Bereich von 61 bis 65 mm verstellt werden kann. Damit ist der Anwender flexibel und kann bei Bedarf auch andere Bohrungen ausführen, ohne sich ein neues Werkzeug anschaffen zu müssen. Ein erster Test mit Standard-Wendeschneidplatten lieferte noch nicht das erhoffte Ergebnis, da sich die Maschinen bei Drexelius als nicht kräftig genug erwiesen und daher nicht im optimalen Leistungsbereich betrieben werden konnten. Ingersoll war jedoch imstande nachzulegen und brachte die PS-Variante seiner Schneidplatte ins Spiel, die mit einem speziellen Spanformer versehen ist. Damit wurde der QuadTwist tatsächlich zum Problemlöser und überzeugte die Einrichter mit sehr gutem Spanbruch und hohen Standzeiten.
Stabiles und schnelles Abstechen
Nachdem das Späneproblem beim Bohren gelöst war, wurde Kevin Richstein noch auf eine weitere Herausforderung aufmerksam: das Abstechen von Bauteilen. Vor allem bei großen Durchmessern kam es hier immer wieder zu Verläufen. Je näher das Stechschwert dem Mittelpunkt kam, desto schwieriger wurde sauberes Arbeiten. Richstein überließ Drexelius das Abstechsystem WinCut von Ingersoll. In der Fertigung wurde es gleich mit einem Problemteil getestet, einer Kappe aus S355 Baustahl, die vom Durchmesser 90 mm bis auf 0 abgestochen werden sollte. Umgehend wurde dem Werkzeughersteller positives Feedback gegeben, wie Thomas Gutstein berichtet: „Das WinCut-System hat uns mit seiner hohen Stabilität und Zuverlässigkeit überzeugt. Die Bauteile werden jetzt absolut gerade abgestochen. Obendrein können wir damit höhere Schnittwerte fahren.“
Der Zugewinn an Geschwindigkeit ist beträchtlich. Bei der Kappe etwa wurde die Bearbeitungszeit von 40 auf 20 Sekunden glatt halbiert. Das WinCut-System ist vom Aufbau her komplett anders als ein herkömmliches Stechschwert, wie es zuvor auch bei Drexelius verwendet wurde. Während ein Standardschwert in der Regel nur geklemmt wird, ist hier der dreieckige Schneideneinsatz fest mit dem Halter verschraubt und kann nicht weggedrückt werden. Die effiziente Kühlung des Stechsystems wurde durch 3D-Druck möglich. Über gewundene Kühlkanäle im Inneren gelangt der Kühlstrahl von oben und von unten auf die Schneide und sorgt für eine optimale Spänekontrolle und höhere Standzeiten.
Drexelius hat sich das System in zwei Größen für Durchmesser bis 80 mm und bis 120 mm zugelegt. Mit Ausnahme ganz kleiner Bauteile wird es inzwischen für alle Abstechvorgänge benutzt. Je nach Anwendung setzen die Werker Schneidplatten in den Ausführungen SFJ3 oder SFC3 ein, die mit unterschiedlichen Spanformern versehen sind. Mit dem Service von Ingersoll ist man in Finnentrop sehr zufrieden, wobei vor allem die schnellen Reaktionszeiten hervorgehoben werden.