Innovation des Monats : Superstahl fürs Auto
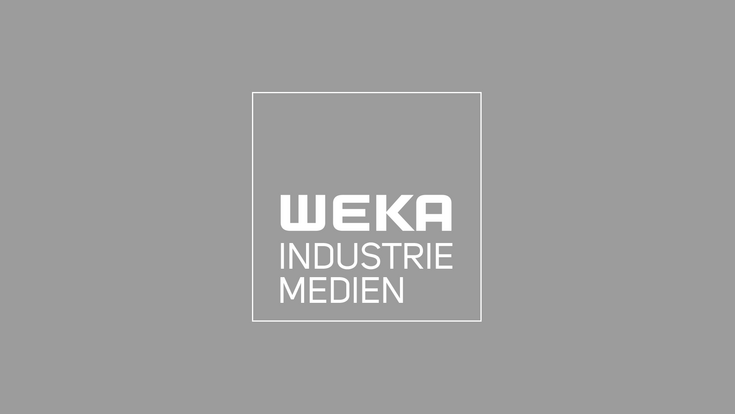
Als 2002 das Pflichtenheft zur Entwicklung eines neuen „Superstahls“ auf den Tischen der Forscher und Entwickler von voestalpine landete, war das der Startschuss für eine der wichtigsten Stahlinnovationen für die Automobilindustrie. Der neue presshärtende Stahl mit dem Markennamen „phs ultraform“ vereinte erstmals Materialeigenschaften, die zuvor in dieser Kombination für nicht realisierbar galten: perfekter Korrosionsschutz, maximale Sicherheit, beste Umwelteigenschaften, einfache Bearbeitbarkeit und Leichtigkeit. Das Projekt „phs“ war zugleich ein Musterbeispiel für das „Know-how-Netzwerk“ des voestalpine-Konzerns, weil daran eine Reihe von Unternehmen beteiligt waren und ihre jeweiligen Kompetenzen – vom Werkstoff über die Verarbeitung – eingebracht haben. voestalpine Stahl, Polynorm, Europlatinen Krems und voestalpine SADEF bildeten das Team, das dieses revolutionäre Stahlprodukt entwickeln und zur Marktreife bringen sollte. Am Ende steht nun ein Produkt mit ausgezeichneten Kaltumformeigenschaften bei höchster geometrischer Komplexität. Durch lasergeschweißte Platinen können verschiedene Werkstoffe eingesetzt werden, die den Leichtbau-Geniestreich ermöglichen. Voestalpine-Forschungs-Chef Peter Schwab: „Der Mut, ein Produkt zu entwickeln, von dem man zu Beginn gar nicht dachte, dass es möglich sein würde, hat sich voll ausgezahlt. Bereits nach kurzer Zeit konnten wir bedeutende Fortschritte erzielen. Heute ist der Einsatz von phs bei beinahe allen Automobilherstellern in Diskussion und von einigen haben uns bereits Bestellungen erreicht.“
Das Verfahren.
Die Nachfrage am Markt war dementsprechend hoch. Vor allem bei sicherheitsrelevanten Teilen werden die extrem guten Crash-Eigenschaften des neuen Stahls gerne eingesetzt. So nutzt seit kurzem BMW die phs-ultraform-Technologie. BMW nahm 2009 in seinem Werk in Dingolfing eine neue Presshärteanlage in Betrieb. Das dabei eingesetzte und mit der voestalpine entwickelte Verfahren ermöglicht eine Gewichtsreduktion von bis zu 23 Kilogramm pro Fahrzeug bei gleich hoher Sicherheit wie bei bisherigen Bauteilen. Pressgehärtet werden in der neuen Anlage hochfeste Karosseriebauteile wie Seitenschweller, B-Säulen oder Längsträger. Konkret werden bei dem neuartigen Verfahren die verzinkten Stahlbleche erst kalt gepresst und anschließend auf über 900 Grad Celsius erhitzt. Dann werden sie erneut von einem Werkzeug gepresst, das die Bauteile durch eine integrierte Kühlung mit 2.600 Liter Wasserdurchfluss pro Minute binnen Sekunden auf 70 Grad kühlt und dabei härtet. Die so behandelten Bauteile erreichen gegenüber unbehandelten Stahlblechen eine drei- bis vierfach höhere Festigkeit und werden anschließend im Karosseriebau mit konventionellen Schweiß- und Klebetechniken verarbeitet.
Auch Porsche setzt auf phs.
Den jüngsten Auftrag für diese Technologie erhielt die voestalpine vom Sportwagenhersteller Porsche. Zwei deutsche Unternehmen des voestalpine-Konzerns – voestalpine Polynorm und voestalpine Gutbrod – werden Sicherheitsbauteile, Bodenstrukturen sowie diverse anderen Strukturteile für Porsche-Sportwagen liefern. Bei den Sicherheitsbauteilen kommt unter anderem „phs ultraform“ zum Einsatz.