Schleifen : Wie sich Wärmeentwicklung beim Metallschleifen verhindern lässt
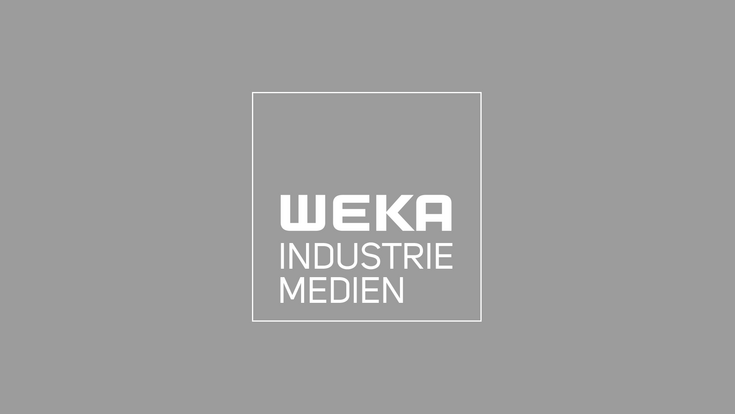
Es gibt die unterschiedlichsten Gründe, warum ein Werkstück geschliffen wird. Sei es, um das Werkstück in eine gewünschte Form zu bringen oder eine bestimmte Oberfläche zu erzielen, sei es, um Verschmutzungen oder unerwünschte Farbschichten zu entfernen. Eines ist allen Schleifprozessen gleich: Beim Schleifen entsteht Wärme, die zu Spannungen im Werkstück und Verfärbungen an der Oberfläche führen kann und im schlimmsten Fall das Werkstück unbrauchbar macht. Beim Schleifen von Metall entstehen Temperaturen bis zu 800 Grad Celsius, Prozesstemperaturen unter 200 Grad Celsius bezeichnen Fachleute als „kühles Schleifen“. Edelstahl zum Beispiel beginnt bei etwa 350 Grad Celsius sich zu verfärben.
Unterschiedliche Materialien
Die Temperaturentwicklung in einem Werkstück ist nicht nur abhängig vom verwendeten Schleifmittel und der Art des Schleifprozesses, sondern auch vom Material, das geschliffen wird. Gut wärmeleitende Materialien wie zum Beispiel Aluminium leiden nicht so stark im Gefüge, da die entstehende Wärme schneller vom Ort des Schleifprozesses abgeführt wird, dafür haben Sie aber oft einen niedrigeren Erweichungspunkt und neigen dann zum schmieren und plastifizieren. Schlechte Wärmeleiter wie Edelstahl rostfrei hingegen sind stark wärmeempfindlich, weil die Prozesswärme aus dem Schleifprozess nicht schnell genug aus der Schleifzone abgeführt wird. Es entstehen Anlauffarben, Gefüge-Veränderungen und die rostarme Eigenschaft geht an dieser Stelle verloren.
Grundsätzlich aber gilt: Beim Schleifen sind hohe Temperaturen nicht gewollt. Es gibt unterschiedliche Ansätze, die unerwünschte Wärme entweder möglichst schnell abzuleiten, zum Beispiel durch Nassschleifen, oder dafür zu sorgen, dass erst gar keine Wärme entsteht. Es gibt Beschichtungen für Schleifmittel, die Wärme reduzieren, oder man ändert den Schleifprozess, indem man weniger Druck ausübt oder die Geschwindigkeit des Schleifbandes reduziert. Dann entsteht zwar weniger Wärme, aber der Schleifprozess dauert auch länger. Man kann auch in mehreren Phasen schleifen und das Werkstück in den Pausen abkühlen lassen, aber das kostet Zeit und damit Geld.
Drei Ecken, zwei Schneiden
3M löst das Problem auf ganz andere Weise. Durch so genannte „Mikroreplikation“ schaffen es die Schleifexperten von 3M, beim Sintern des Schleifmittels exakt gleichförmige, dreieckige Schleifplättchen mit immer zwei aktiven Schneiden herzustellen. Diese präzisionsgeformten „PSG“ (precision shaped grain) Körner kommen in der Marke Cubitron II zum Einsatz. Diese völlig neuartigen Schleifkörner erzeugen beim Schleifen weniger Reibung sondern spanen und damit entstehen beim wesentlich schnelleren Schleifprozess auch sofort weniger Wärme, Anlauffarben, Gefüge-Veränderungen.
Aber was genau ist Mikroreplikation? Für die Herstellung von Schleifkörnern wird in der Regel das geleeförmige Ausgangsprodukt von Keramikkorn gesintert, d.h. gebacken, nicht geschmolzen. Das dadurch entstehende harte und sehr zähe Schleifmittel wird anschließend auf die gewünschte Korngröße gebrochen und auf das Trägermaterial aufgebracht. Durch die Brechung sieht jedes Schleifkorn anders aus und hat dementsprechend auch andere Eigenschaften. Diesen Prozess haben die Entwickler bei 3M modifiziert. Vor dem Sintern wird das Gelee aus Aluminiumoxid in kleine Formen gefüllt, ähnlich wie beim Plätzchen backen. Nach dem Sintern erhält man so absolut identische Schleifplättchen in Form von gleichseitigen Dreiecken. Durch elektrostatische Aufladung werden diese hochpräzisen völlig identischen Schleifkörner ausgerichtet und senkrecht auf das Trägermaterial aufgebracht.
Schneller schleifen
Durch dieses Verfahren schneiden bei jedem Schleifkorn immer zwei Kanten durch das Material, und zwar so lange, bis das freie Schleifkorn verbraucht ist. Und das hat in gleich zweifacher Hinsicht einen positiven Aspekt. Die beiden scharfen Kanten jedes der PSG Schleifkörner schneiden durch das Material und erzeugen beim Schleifen weniger Reibung, wodurch auch weniger Wärme entsteht. Und die definierten Schneiden der Schleifkörner beschleunigen den Schleifprozess insgesamt, da sie mehr Abtrag erzeugen. Das Ergebnis: Der Schliff ist fertig, bevor das Werkstück warm werden konnte.
Weniger Schleifkorn, mehr Abtrag
Man kann den Schleifprozess noch weiter verkürzen, indem man die Anzahl der Schleifkörner im Schleifmedium reduziert. Dabei gilt: weniger Schleifkorn ergibt höheren Abtrag, da der Druck auf jedes einzelne Schleifkorn größer wird. Dadurch reduziert sich die Dauer des Schleifens nochmals, allerdings verringert das gleichzeitig die Oberflächenqualität. Mehr Schleifkörner bedeuten weniger Abtrag und verlängern damit die Schleifzeit, es werden aber bessere Oberflächen erzielt. Cubitron II Schleifmittel sind deshalb bereits werksseitig in jeder Körnung je nach Schleifbandtype optimiert und es stehen für verschiedene Werkstoffe eine Reihe unterschiedlicher Bandtypen zur Verfügung. Bei der Auswahl hilft der Fachhandel.