Industrierobotik : Mobile Poleposition
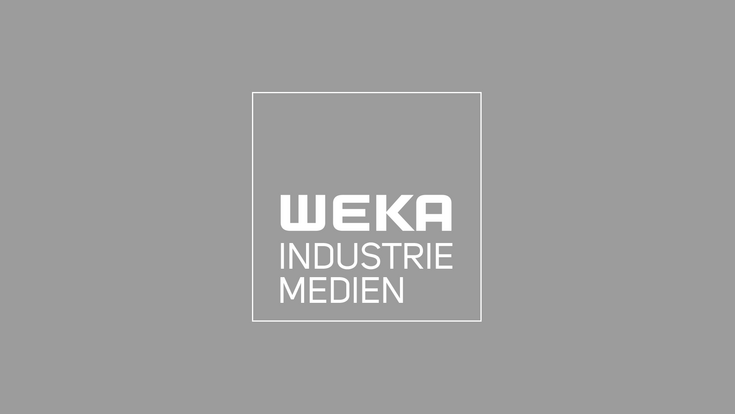
Die konkrete Vision ist schnell und einfach: „Um die Industrie ins Informationszeitalter zu holen, wird der Bedarf an Robotik-Know-how stark zunehmen“, fokussiert Wilfried Kubinger, Studiengangsleiter Mechatronik/Robotik der FH Technikum Wien, aktuell und prägnant den Ausgangspunkt. Was heißt das aber für den Roboter der Zukunft? „Vom schweren Industrieroboter, der – einarmig, energiehungrig und von einem Computer im mehrfachen PC-Format gesteuert – fest mit dem Boden verschraubt seinen monotonen Dienst verrichtet, ist der aktuelle Begriff von Robotik immer weiter entfernt“, berichtet Markus Pfaff von der Fakultät für Information, Kommunikation und Medien der FH Oberösterreich. Und an der Uni Innsbruck mischen Justus Piater und sein Institut für Informatik mit Schwerpunkt Intelligente Systeme noch eine Portion Menschlichkeit in das Zukunftsbild der Robotik: „Unsere Forschungsgruppe Intelligente und Interactive Systeme (IIS) zeigt, wie Roboter von Menschen lernen können, Objekte zu manipulieren.“ So erkennt der Arm eines Roboters beispielsweise, welche Kräfte beim Aufsetzen eines Gewindes notwendig sind, so ähnlich wie auch ein Mensch blind Gewinde eindrehen kann. „Diese Technik ist vor allem für die Optimierung von Industrierobotern interessant“, sagt Piater zum menschlichen Lernprozess der Maschine und ihrer Zukunft.
Mensch „teacht“ den Roboter.
Diese neuen Möglichkeiten bringen aber auch neue Herausforderungen – etwa zum Stichwort Mensch-Maschinen-Kooperation. „Hier sind neue Denkmuster in der Planung und in der Umsetzung hinsichtlich Einbindung der Roboter in die Gesamtanlage sowie Sicherheitskonzepte vonnöten“, erklärt Michael Bauer, Robot Sales Engineer KUKA Österreich, und ergänzt: „Großes Potential bieten weiters autonome Roboter auf beweglichen Plattformen, die dadurch gleichzeitig mehrere Maschinen bedienen oder unterschiedliche Bearbeitungsprozesse ausüben können.“ Daran wird schon intensiv getüftelt. Im Projekt KUKA moiros (KUKA mobile industrial robot system) wird an der Oberflächenbearbeitung eines XXL-Rotorblattsegments mit einer Länge von 10 m von Siemens Windpower Dänemark mobiler Robotereinsatz erforscht und optimiert. Hier agieren Roboter, die sich dorthin bewegen können, wo sie gebraucht werden, die auf mobilen Plattformen mit Hilfe von Umgebungs-Scannern frei und ohne feste Spurführung navigieren können – und dabei keine Menschen gefährden, denen sie unterwegs begegnen.
Kollege Roboter im Labor.
Auch in der Forschung hat der autonome mobile Roboter erfolgreich seinen Platz gefunden. Eine Innovation in der Life-Science-Branche präsentierte Yaskawa im April 2014 auf der Analytica: In einer Live-Demozelle übernimmt ein Roboter mit menschenähnlicher Statur und zwei Händen komplexe Probenvorbereitungen und bedient Analysegeräte – dort, wo eine klassische Automation bisher viel zu unflexibel und zu teuer war. Der Dual-Arm-Roboter CSDA10F, als Serienprodukt aus der Industrieautomation bekannt, wurde neu für Hygieneanforderungen im Laborbereich ausgelegt. Erste Installationen in der Biomedizin-Synthese (Cancer Drug Development) und in der chemischen Analytik (Probenaufbereitung) beweisen, dass dieser Roboter mit nahezu jeder vorhandenen Standard-Laborausrüstung und herkömmlichen Analysegeräten umgehen kann. Der Roboter eignet sich hervorragend für standardisierte Testabläufe, ist jedoch flexibel und kann schnell und einfach völlig neue Arbeitsabläufe dazulernen.
Co-Pilot beim Flugzeugbau.
Schon Realität oder noch Fiktion? Im Schritttempo fährt der Roboter am Flugzeugrumpf entlang, dabei trägt er gleichmäßig ein Dichtmittel gegen Korrosion auf. Umgeben ist der mobile Helfer von Facharbeitern, die montieren, bohren und prüfen. Noch ist ein solches Szenario Zukunftsmusik, aber schon in wenigen Jahren soll es Realität in den Werften der Luftfahrtindustrie sein: Im EU-Projekt VALERI – kurz für Validation of Advanced, Collaborative Robotics for Industrial Applications – entwickelt ein europäisches Konsortium einen mobilen, autonom arbeitenden Roboter, der eigenständig durch eine Produktionshalle fährt und Seite an Seite mit den Ingenieuren arbeitet. Ersetzen soll er die Fachkräfte nicht, sondern sie bei anstrengenden und monotonen Tätigkeiten entlasten und Inspektionsaufgaben übernehmen. An dem Vorhaben beteiligt sind Airbus DS, FACC AG, IDPSA, Prodintec sowie KUKA Laboratories und Profactor. Die Leitung des EU-Projekts liegt beim Fraunhofer Institut für Fabrikbetrieb und -automatisierung IFF in Magdeburg. Es wird mit rund 3,6 Millionen Euro gefördert. „Bei der Montage von Rumpfelementen müssen große Mengen von Dichtmitteln auf die Nahtstellen aufgetragen werden. Mobile Roboter können diese Arbeit sehr gut übernehmen“, erklärt José Saenz, der Projektverantwortliche am IFF und Gesamtkoordinator von VALERI. Auch hier gilt der Umkehrschluss im Maschineneinsatz: Der Roboter wird mobil, nicht das Werkstück! „Die Elemente eines Flugzeugrumpfs sind zu groß, um sie an einen herkömmlichen Produktionsroboter anzupassen, es muss umgekehrt gehen“, so Saenz, „der Roboter fährt an die gewünschte Stelle am Flugzeug.“ Bereits Ende dieses Jahres soll der Prototyp unter Laborbedingungen seine erste Fahrt aufnehmen. Für Oktober 2015 sind dann Tests unter realen Bedingungen anberaumt: In einer Pilotanlage von Airbus DS muss sich der mobile Assistent autonom bewegen, reale Flugzeugelemente erkennen und Aufgaben lösen.
Roboter fühlt mit Sensorhaut.
Können mobile Roboter fühlen? Die Systeme der „APAS family“ von Bosch zeigten auf der Hannover Messe im April 2014 eine Roboterinnovation, die wirklich und wörtlich bis „unter die Haut“ geht. Sie befreit Menschen von gefährlichen, anstrengenden, eintönigen und schmutzigen Arbeiten zugunsten höherwertiger Tätigkeiten, ist aber – anders als herkömmliche Industrieroboter-Systeme – mobil, flexibel und sogar ohne Abschirmung einsetzbar. Das Kernstück, der automatische Produktions-Assistent „APAS assistant“, hat eine mit Sensoren versehene Ummantelung, die Kollisionen verhindert. Er erkennt durch seine „Sensorhaut“, wann ihm sein menschlicher Kollege zu nahe kommen kann. Bevor er ihn direkt berührt, stoppt der „APAS assistant“, und er setzt seine Arbeit erst fort, wenn der Mensch den unmittelbaren Aktionsbereich des Systems verlassen hat. Der Roboter hat Rollen sowie eine leicht zu bedienende Arretierung. Dadurch ist er schnell und einfach an verschiedenen Orten in einer Produktion einsetzbar. Der sensitive Drei-Finger-Greifer kann eine Vielzahl komplex geformter Teile sanft oder fest greifen. Integrierte Kameras helfen ihm dabei, die Umgebung selbstständig zu erfassen, Teile eigenständig zu erkennen und präzise zu handhaben. Über ein Bedien-Touchpad kann der Maschinenbediener dem „APAS assistant“ Arbeitsabläufe als grafische Schritt-für-Schritt-Darstellungen der Aufgaben innerhalb kurzer Zeit beibringen. Einmal erlernte Aktionen werden vom Produktions-Assistenten gespeichert, sie können jederzeit auf Knopfdruck abgerufen werden.
Weiter auf Seite 2: Roboter als mobile Inspektoren
Wird der mobile Roboter auch zum Kontroll-Inspektor? Yes, he can! Wichtige Komponenten von Kraftwerken wie Turbinen, Pipelines, Kessel und Ventile müssen regelmäßig überprüft werden. Neben einer zerstörungsfreien Prüfung muss dabei eine lückenlose Dokumentation erstellt werden, die Veränderungen bei späteren Revisionen nachweisen kann. Als Ersatz für die übliche manuelle Ultraschalluntersuchung entwickelte die Areva-Tochter intelligeNDT Systems & Services (Erlangen) einen leichten und transportablen Roboterarm, der einen Ultraschall-Prüfkopf für die zerstörungsfreie Werkstoffprüfung aufnehmen kann – inklusive 3D-Dokumentation der Ergebnisse. Reinhold Zeilinger, Entwicklungs- und Fertigungsleiter Robotik bei iNDT, präzisiert die Vorteile: „Wichtigstes Kriterium der Entwicklung war neben der hohen Genauigkeit auch ein möglichst geringes Gewicht. Denn der Roboter muss auch schon mal per Hand auf eine Kraftwerksbühne in 20 m Höhe getragen werden, um dort prüfen zu können.“ Das gelingt, denn der transportable Roboterarm mit vier oder mehr Achsen bringt weniger als 10 kg auf die Waage. Damit kann er ohne Umbauten auch auf mehrfach gekrümmten und schrägen Oberflächen Stutzenschweißnähte überprüfen und Ultraschall-Arrays immer in die richtige Ausrichtung und an die richtige Position bringen. Montagezelle für E-Mobile. Die IBG/Goeke Technology Group hat auf der diesjährigen Hannover Messe ihre aktuelle Innovation iProcell vorgestellt. Dabei handelt es sich um eine flexible, vollautomatische Montagezelle für Elektrofahrzeuge. iProcell gewährleistet die vollständige Prozesskette – vom Entladen aus dem Container bis hin zur fertigen Montage. Die Weltneuheit bedingt dabei einen grundsätzlich veränderten Fahrzeugaufbau, der auf der Messe für Besucher bereits eindrucksvoll präsentiert wurde. Die Montage wird hier mittels eines völlig neuen Systems revolutioniert. Da mit iProcell ein Fahrzeug in einer optimierten Reihenfolge zusammengesetzt wird, verkürzt sich die Montagezeit signifikant. Mit Hilfe eines absoluten und stringenten Gleichteilsystems minimiert sich darüber hinaus die Bauteilevielfalt. Diese Tatsache wirkt sich auch auf die Anzahl der notwendigen Herstellerwerkzeuge aus. Matthias Goeke, geschäftsführender Gesellschafter der IBG/Goeke Technology Group, erklärt: „Durch die optimierte Nutzung von Gleichteilen können so in sekundär notwendigen Prozessen sowohl entstehende CO2-Belastungen als auch Herstellkosten reduziert werden. Weil neuartige und recycelbare Materialien, wie z. B. Bioverbundwerkstoffe, eingesetzt werden, wird es mit iProcell zudem möglich, eine besondere Nachhaltigkeit im Fahrzeug zu erreichen.“ So wird der mobile Roboter auch zum Helfer in der Umsetzung von Ökozielen. Packen mit Systemansatz. Auch erfolgreich etablierte stationäre Systeme werden immer mobiler, flexibler und autonomer. Im Laufe der letzten Jahre hat ABB daher den Übergang in ein neues Roboterzeitalter eingeleitet. Standardlösungen helfen, Komplexität zu reduzieren, und neue Werkzeuge machen die Implementierung von Robotersystemen so einfach wie nie zuvor. Zur weltweit größten und wichtigsten Fachmesse im Bereich Verpackungstechnik interpack präsentierte ABB im April 2014 eine Vielzahl von Technologien, die das zuvor Genannte herausstellen. Ein Beispiel dazu: Seit fast 15 Jahren ist der IRB 360 FlexPicker von ABB einer der führenden Roboter in der Technologie für Pick-&-Place-Applikationen mit Hochgeschwindigkeit. Basierend auf dieser Erfahrung umfasst die FlexPicker-Produktfamilie jetzt Varianten mit Handhabungskapazitäten von 1 bis 8 kg und Reichweiten von 800 bis 1.600 mm – das bedeutet, es gibt für fast jeden Bedarf einen IRB 360.